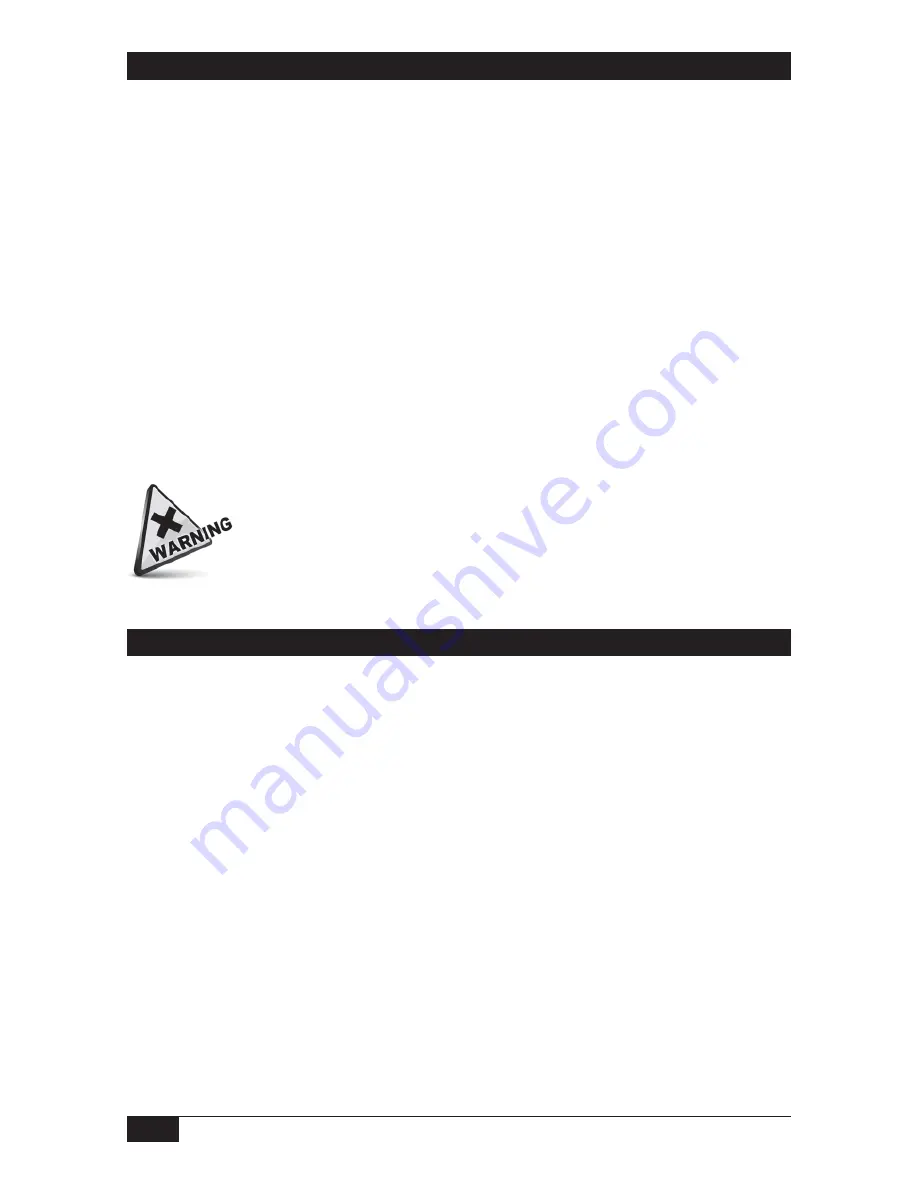
2/8
Form 1630 (09.18) ©SOR Inc.
Installation
If continuous operation is required during inspection or maintenance, a bypass
must be installed.
Inspect the regulator for any damage, foreign substances, or blockages.
Clean all pipelines to remove dirt and scale prior to installation.
Apply pipe compound to the male pipeline threads. Use caution to prevent the
sealant from getting inside the regulator.
Install the regulator as close as possible to the instrument or tool it will be
servicing and orient it such that the direction of gas flow is from the “IN” to the
“OUT” connection as marked on the body.
For best drainage, position the drain valve until it is at the lowest point on the drip
well housing. Positioning of the drain valve may be improved by rotating the drip
well with respect to the body.
The exhaust port should be kept free and unplugged. Rotating the bonnet relative
to the body may change the vent hole orientation. Exhaust may be remotely vented
by installing tubing to the ¼” NPT port (“E” Accessory – Tapped Exhaust).
The 1267AFR may vent some gas to the atmosphere. If integrated into a
hazardous system, this vented gas could accumulate and if ignited it could
cause personal injury, death, or equipment damage. For use in a hazardous
system, the regulator must be vented to a remote and safe location. The vent
line or stack opening must be protected from condensation or clogging.
Calibration
Before turning on air supply, loosen the adjusting screw by rotating it counter-
clockwise. Do this until there is no compression in the control spring.
Apply air supply, and tighten adjusting screw by rotating it clockwise. Tightening
the screw will increase the output pressure. Pressure should always be monitored
during startup to ensure that the regulator isn’t over-pressured.
Once desired pressure setting is reached, tighten the locknut to maintain the
calibration and prevent accidental adjustment.