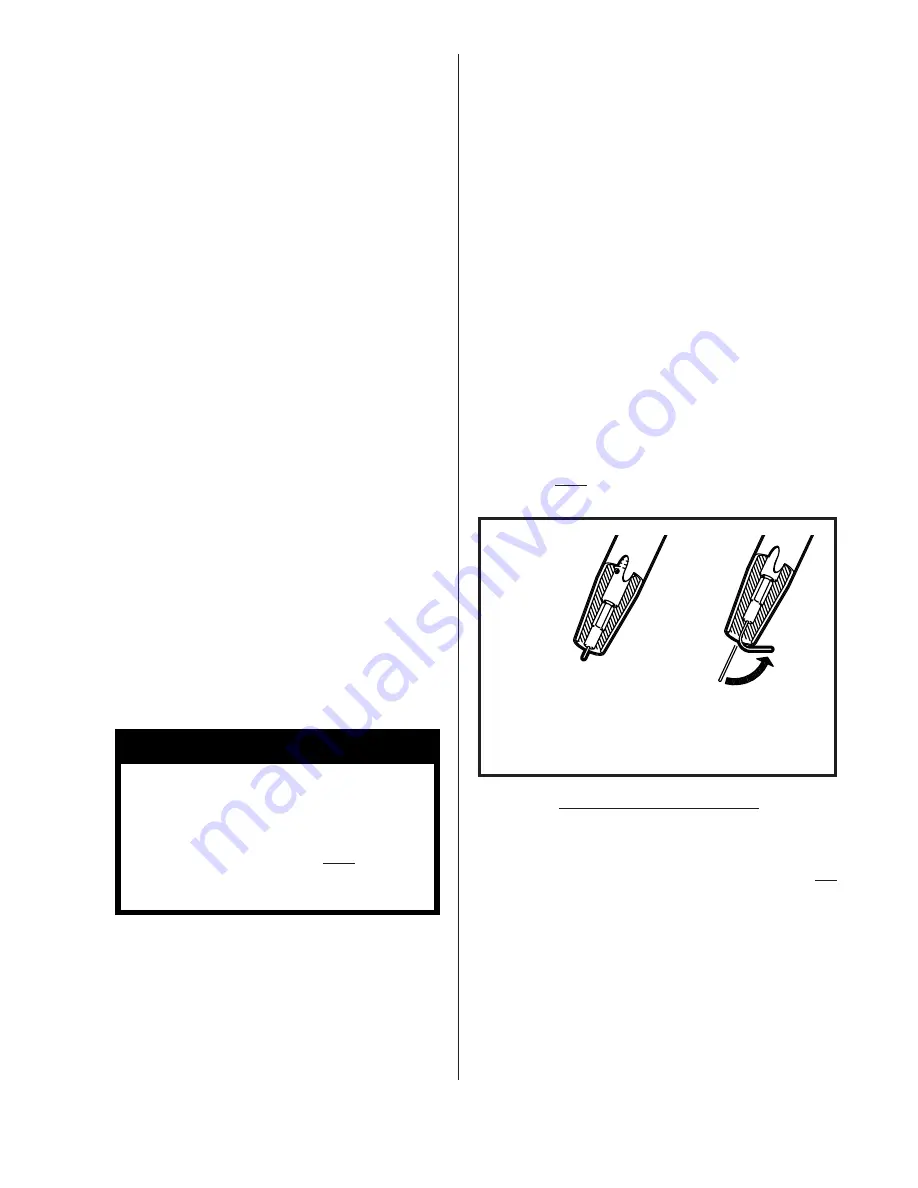
Snap-on Tools Corporation Kenosha, WI 53141-1410
7
FITTING AND THREADING THE ELECTRODE
WIRE (Cont.)
FITTING AND THREADING THE ELECTRODE
WIRE (Cont.)
Thread the electrode wire
through the inlet guide, over
the feed roll and into the outlet
guide. Ensure that the wire
locates in the feed roll groove.
Do not allow the wire on the
spool to loosen.
Close and relatch the pressure
roll arm.
Stretch the torch cable straight
out in front of the machine
making sure there are no kinks.
Remove the nozzle and contact
tip from the torch.
Turn on the circuit breaker on
the front of the machine. The
cooling fan will start and the
"ON" indicator light will illu-
minate. Set the MIG/TIG VOLTAGE
control switch to "MIG 3" and the
WIRE SPEED control to "5". Pull
the trigger on the MIG torch.
The wire feed system will start
and wire will be fed through the
cable liner and torch. If the
wire does not feed, or appears to
slip, tighten the pressure roll
arm adjusting nut. Feed the wire
until it protrudes from the
front of the torch approximately
six inches.
CAUTION
Keep hands and face away
from the front of the torch
and do not allow the wire to
contact ground. The wire
is electrically HOT when
the torch trigger is actu-
ated.
8.
9.
10.
11.
Install the contact tip over the
protruding wire and tighten it
firmly using a proper size
wrench. Make sure the tip is the
correct size for the wire being
used.
Install the nozzle on the torch.
For steel, the contact tip
should be flush or stick out up
to 1/16 inch beyond the end of
the nozzle. For aluminum, the
contact tip should be recessed
1/8 to 1/4 inch inside the
nozzle. Using wire cutters,
trim off the wire so the stickout
is approximately 1/4 inch for
steel or 1 inch for aluminum.
For aluminum, the end of the wire
should be bent over so it does
not JAM into the work. This is
called a "scratch start".
12.
13.
FOR ALUMINUM:
CONTACT TIP
RECESSED 1/8" - 1/4"
FOR STEEL:
CONTACT TIP
FLUSH WITH NOZZLE
1/4"
STICK-OUT
1"
STICK-OUT
FIG. 9. WIRE STICKOUT - STEEL, ALUMINUM
For steel welding only, spray
anti-spatter compound inside
the nozzle and on the outside of
the contact tip. For aluminum or
stainless steel welding, NO
anti-spatter compound can be
used as it will contaminate the
weld.
14.