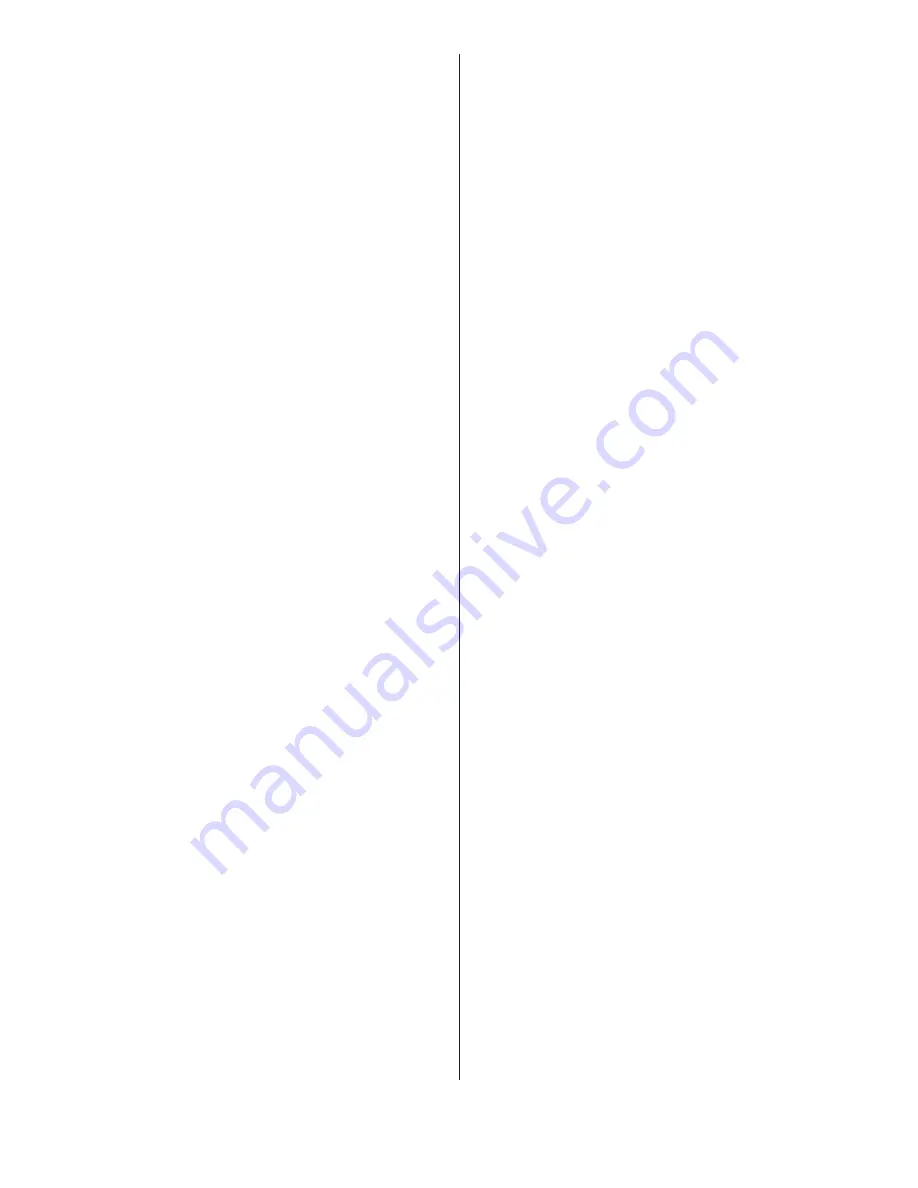
Snap-on Tools Corporation Kenosha, WI 53141-1410
3
SPECIFICATIONS (Cont.)
DESCRIPTION
The MM140SL consists of a combi-
nation MIG welding power source and
remote feed unit, a MIG torch with
10 foot cable, a fifteen foot feeder
control cable, a fifteen foot work
cable with clamp, a twenty foot
power input cable, a gas regulator -
flowmeter, a torch accessory kit,
and a built-in cylinder rack and
industrial wheel kit.
Welder controls are simple and
clearly marked. The output voltage
is controlled by a twelve position
tap switch, providing 4 TIG and 8
MIG voltage selections. Wire feed
speed is controlled by the wire
speed potentiometer.
A SPOT WELD control switch and
adjustable timer circuit provides
Consumable MIG Spot Welding capa-
bilities of light gauge steel.
SPECIFICATIONS
PART NUMBER:
MM140SL
INPUT POWER REQUIREMENTS:
Voltage
115 volts AC
Phase
single phase
Frequency
50/60 hertz
Current
(see below)
OUTPUT POWER @ 100% Duty Cycle:
15 Amps Input Current=
100 Amps
20 Amps Input Current=
120 Amps
30 Amps Input Current=
140 Amps
DUTY CYCLE TIME PERIOD:
10 minutes
OPEN CIRCUIT VOLTAGE:
18 - 33 volts DC
ARC VOLTAGE:
14 - 26 volts DC
WELD CURRENT RANGE:
30 - 140 amps
REMOTE FEED UNIT
Input Voltage
28 VAC
Wire Feed Speed Range:
50-800 IPM
DUTY CYCLE - SPOT WELDING:
30 X 2 second spots per 10 minute
period
SPOT WELD TIME:
0 TO 3 seconds
WIRE TYPES:
mild steel,
stainless steel, aluminum,
bronze, flux cored,
flux cored - gasless
WIRE SIZES:
.023" - .045" steel,
3/64" aluminum,
(.023" - 3/64" alum. w/spool gun)
.030" - .035" bronze,
.035" - .045" flux cored
(gas shielded or gasless)
SHIELDING GASES:
For Steel
CO2 or Argon/CO2 mix
For Aluminum, Bronze
Argon
For Stainless Steel
98% Argon/2% Oxygen
For Flux cored
CO2 or
Argon/CO2 mix
DIMENSIONS:
Height
32-1/4 in.(81.9 cm.)
Width
14-1/2 in.(36.8 cm.)
Depth
26-1/4 in.(66.7 cm.)
Weight
155 lbs.(70.4 kg.)
TORCH SPECIFICATIONS
NECK ANGLE:
60 degrees
LEAD LENGTH:
10 feet
OVERALL LENGTH:
10 feet
COOLING METHOD:
gas (air)
RATING - DUTY CYCLE:
With Argon/CO2 gas
150 amps @ 100%
With CO2 gas
200 amps @ 100%