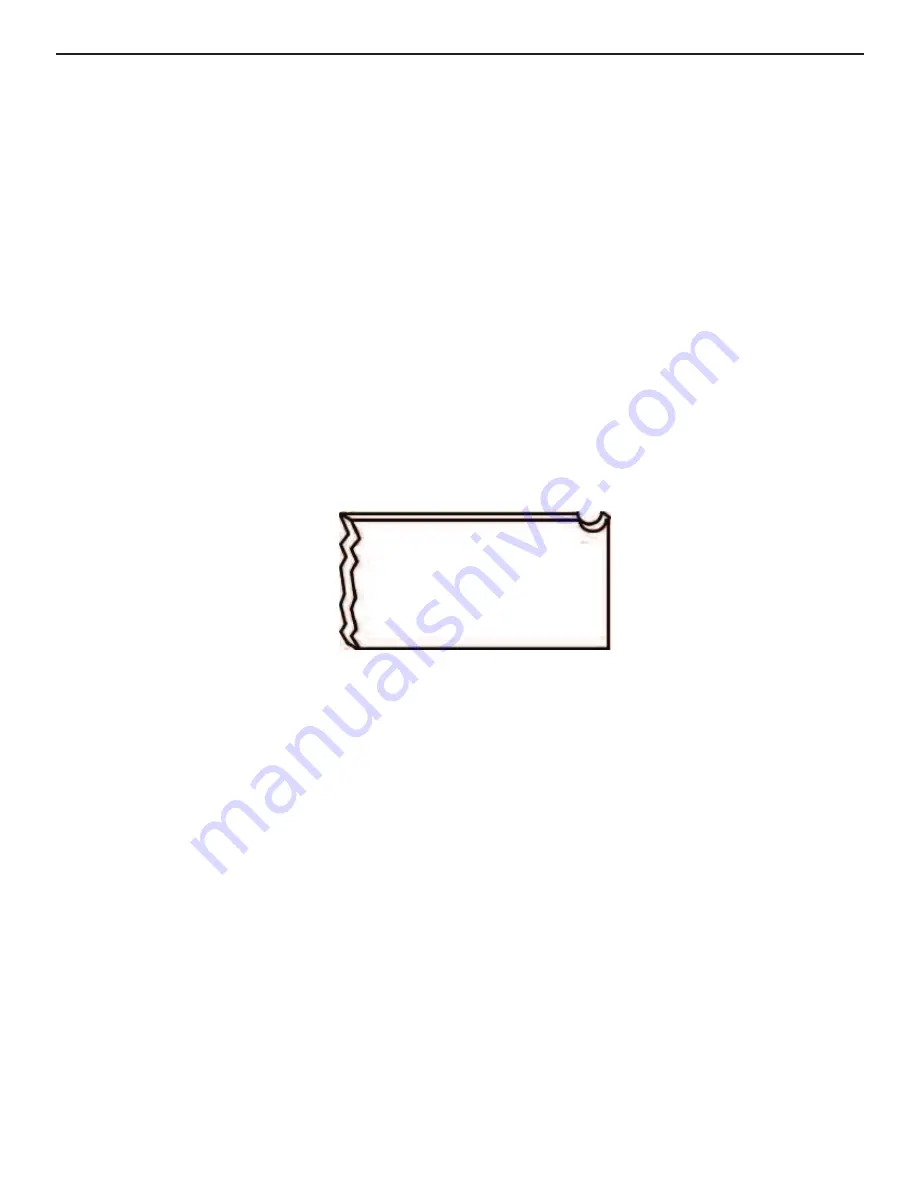
Bits for Turning and Machining Brass
Brass tends to pull or drag when machined. It's best to machine it on dead center with
the top rake in the horizontal plane of the lathe centers. Softer than steel, brass needs
less support for the cutting edge. Brass cutters require an almost flat top angle and can
gain greater angle keenness only in increased side and end rakes. It is often advisable to
hone the cutting edges of cutters used to machine brass.
Note: All roundnose cutters are ground with flat tops and equal side rakes because they
are fed across the work, to both right and left.
Special Chip Craters and Chipbreakers
When grinding cut-off blades, and occasionally on other cutter bits where the material's
extreme hardness or toughness makes it difficult to control the chip leaving the work, it
sometimes helps to grind a smooth, round crater just behind the cutting edge. This serves
as a chip guide and starts the chip curling smoothly (Figure 9.7).
Figure 9.7 A crater starts the chip curling smoothly.
Using a Center Gauge to Check V-Thread Forms
It may be convenient to grind a standard cutter bit for thread cutting, especially for
cutting standard 60° V-threads. When grinding an ordinary square cutter into a thread
cutting tool, take care to ensure a true thread form. The easiest way is to use an
ordinary center gauge for a standard V-thread tool or a special thread gauge for special
thread forms.
To grind a cutter for an ordinary V-thread, grind first the left side of the tool, then the
right side, to 30°. Be careful to grind equally from both sides to center the toolpoint. Then
test for true form by inserting the newly ground point in the closest-sized V in a standard
center gauge (Figure 9.8). Examine the gauge and cutter before a light. When the cutter
is ground perfectly, no light streak shows between tool and gauge. Use a grinding chart
for other rakes.
9-4
Or Visit www.smithy.com
Grinding Cutter Bits for Lathe Tools
Содержание Midas 1220 XL
Страница 6: ......