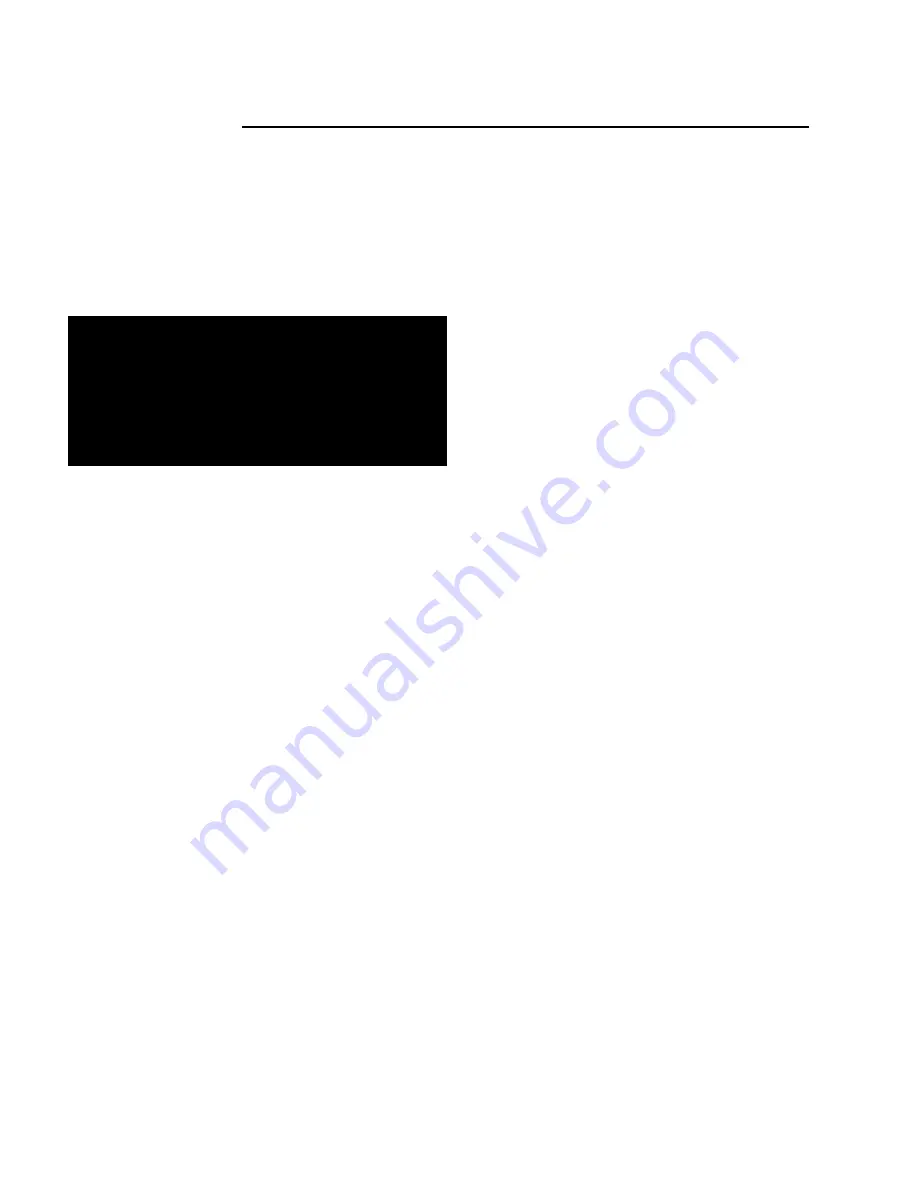
19
This boiler has been designed to provide years of
trouble free perfor mance in nor mal installations.
Examination by the homeowner at the beginning of each
heating season, and in mid-heating season, should
assure continued good performance. In addition, the
boiler should be examined by a qualified ser vice
professional at least once every year.
NOTE: Do not draw water from heating system for
cleaning. Minerals in the water can build up on the
heat transfer surfaces and cause overheating and
subsequent failure of the cast iron sections.
NOTE: Do not obstruct the flow of combustion and
ventilation air.
NOTE: If boiler is equipped with a low water cutoff,
follow manufacturer's maintenance instructions.
BEFORE EACH HEATING SEASON
1. Remove and inspect draft hood and vent piping
(connecting draft hood to chimney or vent) for
obstructions, soot accumulation, rust or corrosion. Clean
and replace as necessary. Check tightness of joints;
seal all joints where necessary.
2. Check boiler flue passageways in the boiler sections
for any blockage or soot accumulation. Remove draft
hood, jacket top and flue collector. Using a flashlight,
examine all flue passageways.
a. If passageways are free of soot and obstructions,
replace flue collector and seal with furnace cement.
b. If passageways need cleaning, remove burners as
described in paragraph 3 below. Insert long-handle
bristle flue brush down between section tubes and
upward through sections from combustion chamber in
both diagonal directions to remove carbon from
finned surfaces. Vacuum debr is. Replace flue
collector and seal with furnace cement.
c. Reinstall jacket top panel and draft hood.
3. Check and clean burner assembly. Remove burner
access panel. Lift burners up and to rear until burners
are disengaged from orifices. Brush top of burners with
soft bristle brush and blow out with air or vacuum.
4. Check gas manifold for proper position and
reassemble burners to the manifold. Line up holes in
burners with the orifices, and slide assembly back into
position. BE SURE TO REINSTALL BURNERS WITH
BURNER PORTS ON THE TOP SURFACE (UPRIGHT).
5. When a low water cut-off has been utilized, follow the
manufacturer’s maintenance instr uctions. As a
minimum, test the operation of electronic controls at
least once a year. Remove, clean and inspect the probe.
If the LWCO fails to operate proper ly it must be
replaced. Float type controls should be flushed once a
month during the heating season.
6. Follow "System Start-Up & Adjustments" procedures
in Section 3 of this manual.
Steam Boiler Cleaning Instructions
The following procedures must be followed on initial
start-up and if the presence of sediment, sludge or
impurities hamper proper boiler operations.
1. With gate valves closed on supply and return lines,
start burner and allow boiler to become pressurized so
that the pressuretrol may be adjusted and set for limit
cut-off desired (normally about 3 psi). Turn off burner
and allow pressure to drop to 0 psi., then proceed with
the following cleaning procedure.
2. Remove the pressure relief valve.
3. Add caustic soda (lewis lye) through this opening at
the rate of one pound per thousand square feet of
radiation capacity. Scout, Squirk or similar steam boiler
cleaners may be used instead of lye. Tr isodium
phosphate (1/4#) is also an excellent cleaner.
4. Provide pipe connection (full size) from pressure relief
valve opening to a convenient drain to serve as a vent.
5. Fill the boiler with a manual fill valve until water starts
to trickle from this pipe.
6. Fireboiler at sufficient rate to generate and maintain
steam. Entrained water and impurities will then discharge
(with steam) from open vent. Add water as necessary so
that the low water cutoff does not shut off burner.
SECTION 4: MAINTENANCE
DANGER:To avoid fire and explosion hazards: Do
not store anything against the boiler or allow dirt or
debris to accumulate in the area immediately
surrounding the boiler. Keep boiler area clear and
free from combustible materials, gasoline and other
flammable vapors and liquids. Lint, paper or rags
must not be allowed to accumulate near the burners.
Do not place clothing on boiler to dry.
TO TURN OFF APPLIANCE
1. Set the thermostat to lowest setting.
2. Turn off all electric power to the appliance if service is to be performed.
3. Turn gas control knob counterclockwise to "OFF". Do not force.