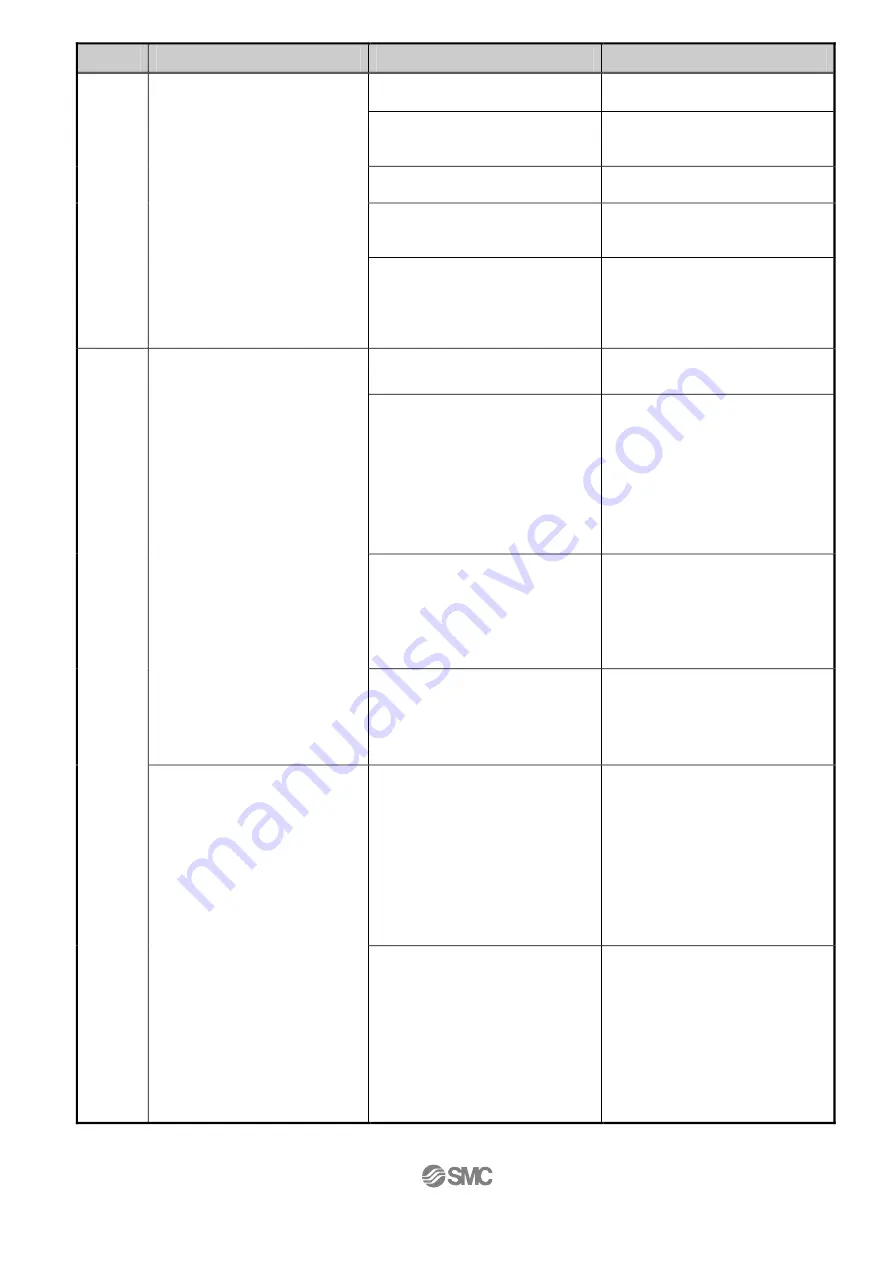
- 47 -
No.
Phenomenon
Cause
Countermeasure
5) The cable is not connected
or has been disconnected.
Confirm that the cable is connected
correctly. /See 4. Wiring of cable on p.32
6) It was not the intended origin position
because the actuator pinched the
work-
piece during the“return to origin”.
Remove the work-piece and restart
the return to the intended origin
position.
7) Wrong input [0] is input as the
positioning force.
Check the step data.<Moving force>
/See 3.3.Step data setting method on p.23
8) The step data position is not
changed correctly after the return
to origin direction is changed.
Check the step data.
<Position>
/See 3.3.Step data setting method on p.23
9) Because the operation of the
step data is set to [INC/relative],
the table comes into contact with
an external object and does not
move due to continuous operation.
Check the step data.
<Position>
/See 3.3.Step data setting method on p.23
2
Operation not completed
/ During operation
(Not always, but may happen
occasionally)
Alarm for “Step data ALM2/code:
1-051
” is generated.
↓
<Procedure of restart>
Input the “reset” signal.
1) Command invalid
(unregistered) step data.
Check if the step data is valid
(registered).
2) Different input signal to the
expected step number is inputted
to the controller, because of a too
short an interval between the
input signal of “IN*” and the
“Drive” or inputting the signals at
the same time.
Add an interval of 15ms (the
recommendation is 30ms) or more
between the input signals.
/
See
“Operating procedure input / output signals
for each op
eration type” on P.27
3) Different input signal to the
expected step number is inputted
to the controller, because the
input signal time was too short.
Add an interval of 15ms (the
recommendation is 30ms) or more
between the input signals.
/
See
“Operating procedure input / output
signals for each operation type” on P.27
4) Different input signal to the
expected step number is inputted to
the controller, caused by PLC or
other device.
Check that the step number is
inputted correctly for the required
motion.
- Operation completed by
unexpected motion.
- No alarm
/ During operation
(Not always, but may happen
occasionally)
1) Different input signal to the
expected step number is inputted
to the controller, because of a too
short an interval between the
input signal of the “IN*” and the
“Drive” or inputting the signals at
the same time.
Add an interval of 15ms (the
recommendation is 30ms) or more
between the input signals.
/
See
“Operating procedure input / output
signals for each operation
type” on P.27
Note) Recommend to check the
“OUT” output signal for more secure
operation.
2) Different input signal to the
expected step number is inputted
to the controller, because the
input signal time was too short.
Add an interval of 15ms (the
recommendation is 30ms) or more
between the input signals.
/
See
“Operating procedure input / output
signals for each operation type” on P.27
Note) Recommend to check the
“OUT” output signal for more secure
operation.
2021-05-20 10:32
DW913599