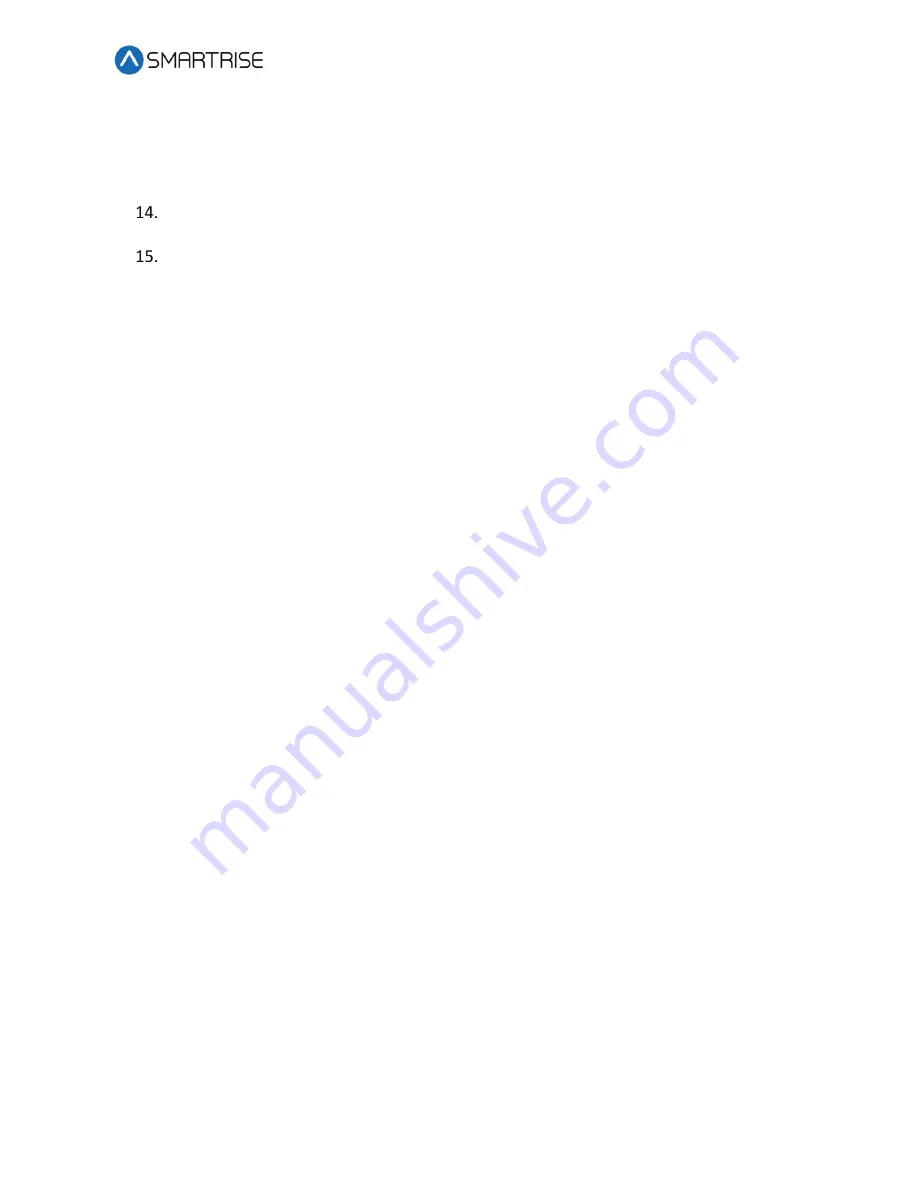
Drive Startup Manual DSD412
March 5, 2020
©2020 Smartrise Engineering, Inc. All Rights Reserved
Page 11
a.
If the encoder feedback is in phase upon first powering up, go to step 14.
b.
If the encoder feedback is out of phase upon first powering up may be out of phase
upon first power-up, remove line power and swap
the encoder A and A- wires. Go to
step 14.
Reapply line power and command the car to move. The car should now move at the
programmed Inspection Speed.
Is the motor running in a reverse direction from what is commanded?
a.
If the motor is running in the forward direction, the process is complete.
b.
If the Motor is running in a reverse direction from what is commanded, swap the
field (+) and (-) wires. It may be necessary to swap the encoder A and A- wires after
changing the field wires. The process is complete.
Shuddering at High Speed
At times, shuddering may occur. If shuddering at high speed occurs, verify the following
conditions:
•
Motor voltage vs. transformer secondary input voltage – Recommendation is that the
transformer secondary voltage be at a minimum equal to the rated armature VDC. For
best results that account for sagging utility, etc., VAC = 1.05 x VDC is a better number to
use.
•
Make sure that the motor weak field current is adjusted so that with full load up at
rated speed yields the rated armature VDC used above.
•
Rope resonance – Use the high speed / low speed bandwidth adjustments (#39 & 40).
Reduce the setting of the high speed and width to maybe 50% of that for low speed. Set
the gain change speed (#105) at 25-50% of rating. Elevator speeds of 350-500 with 2:1
roping can be problematic. Using the notch filter may help (#190, 191).
•
Make sure there is no slop / backlash in the encoder coupling and that the encoder is
not wobbling or vibrating.
•
Keep Tach Rate Gain (#107) at zero.
•
Verify the correct motor and encoder data, perform diagnostics (#998) and self-tune
(#997), and use the values for self-tune (#4, 6, 51) by copying them from (#613, 614,
615) and then turning #2 to ON.
•
Reduce motor armature response (#8) to 250 r/sec.
•
Make sure there is a ground bonding wire from motor frame to drive chassis.
•
Make sure the encoder is electrically insulated from the motor shaft and frame.
•
If using a friction wheel encoder, make sure both surfaces are perfectly round.
Содержание DSD412
Страница 1: ......
Страница 2: ...Page intentionally left blank...