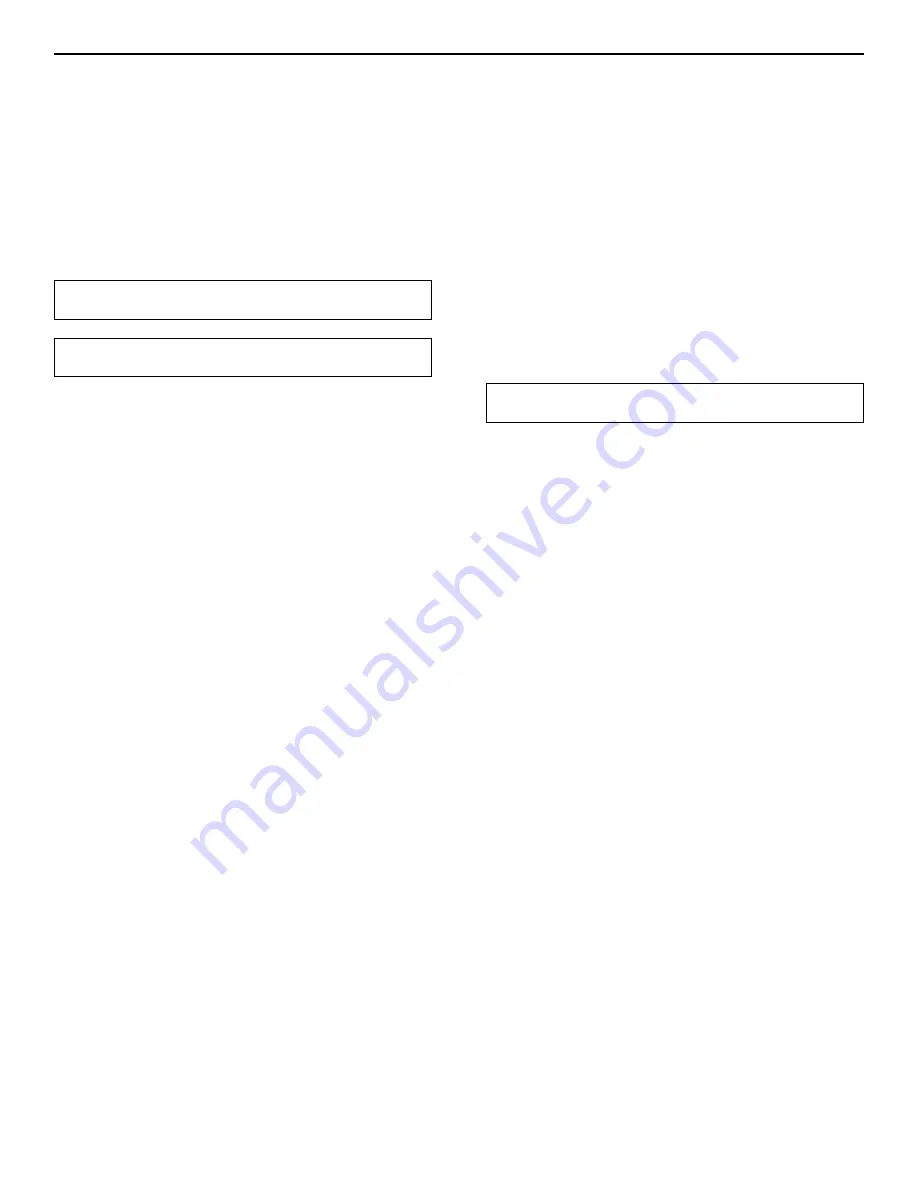
EUTECTIC EC-10 DV
14
Recent investigations of boilers which were installed in hard
water areas, revealed that mineral deposits had accumulated
at the bottom of the heat exchanger. In addition, sludge, scale
and other solid contaminants were present in boilers installed
in older systems or where the water was supplied from a well.
This accumulation —observed to be 64 mm (2-1/2”) or more –
creates an insulating layer that drastically affects boiler
efficiency by reducing the transmission of heat through this
primary transfer surface and causes extreme metal
temperatures that eventually crack the heat exchanger.
RECOMMENDATIONS:
On all installations in hard water areas:
1. The system should be thoroughly inspected for leaks which
must be repairedhowever minor they may be.
2. The initial water charge of the system must be treated to reduce
its hardness to an acceptable level.
3. Where a continuous fresh supply of hard water is fed to the sys-
tem as with process or steam boilers, it is essential that:
a) The feed water is treated to reduce the level of hardness to a
point where no significant deposition occurs in the boiler.
OR
b) The treated boiler water circulates through a closed circuit
heat exchanger which in turn will heat the distribution system
water.
In addition to the aforementioned, older systems and those
supplied from wells may require that a filter or strainer be incor-
porated in the circuit at some point on the return line closest to
the boiler. Suitable water treatment filters are commercially
available for this purpose.
Note:
DOMESTIC TANKLESS HOT WATER COILS ARE HIGHLY
SUSCEPTIBLE TO THIS CONTAMINATION
THE TERMS OF THE BOILER WARRANTY WILL NOT APPLY TO
FAILURES ENCOUNTERED UNDER THESE CIRCUMSTANCES.
WE STRONGLY RECOMMEND THAT YOU CONVEY THIS VITAL
INFORMATION TO ALL PARTIES CONCERNED.
APPENDIX D
WATER QUALITY
APPENDIX E
A low water cut-off may be required by local codes. If the boiler
is installed above the radiation level, a low water cut-off device
must be installed in all instances. Do not install an isolation
valve between the boiler and the low water cut-off.
a. Seal any unused openings in the common venting system.
b. Visually inspect the venting system for proper size and
horizontal pitch and determine there is no blockage or
restriction, leakage, corrosion and other deficiencies which
could cause an unsafe condition.
c. Insofar as is practical, close all building doors and windows
and all doors between the space in which the appliances
remaining connected to the common venting system are
located and other spaces of the building. Turn on clothes
dryer and any appliance not connected to the common
venting system. Turn on any exhaust fans, such as range
hoods and bathroom exhausts, so they will operate at
maximium speed. DO NOT operate a summer exhaust fan.
Close fireplace dampers.
d. Place in operation the appliance being inspected Follow the
lighting instructions. Adjust thermostat so appliance will
operate continuously.
e. Test for spillage at the draft hood relief opening after 5
minutes of main burner operation. Use the flame of a match
or candle, or smoke from a cigarette, cigar or pipe.
f. After it has been determined that each appliance remaining
connected to the common venting system properly vents
when tested as outlined above, return doors, windows,
exhaust fans, fireplace dampers and any other gas burning
appliance to their previous conditions of use.
g. Any improper operation of the common venting system
should be corrected so the installation conforms with the
National Fuel Gas Code, ANSI Z223.1-latest edition or CSA
B149.1-00 for natural gas and propane. When resizing any
portion of the common venting system, the common
venting system should be resized to approach the
minimum size as determined using the appropriate tables
in Appendix G in the National Fuel Gas Code, ANSI Z223.1-
latest edition or CSA B149.1-00 for natural gas and
propane.
APPENDIX F:
REMOVAL OF EXISTING BOILER FROM COMMON VENT SYSTEM