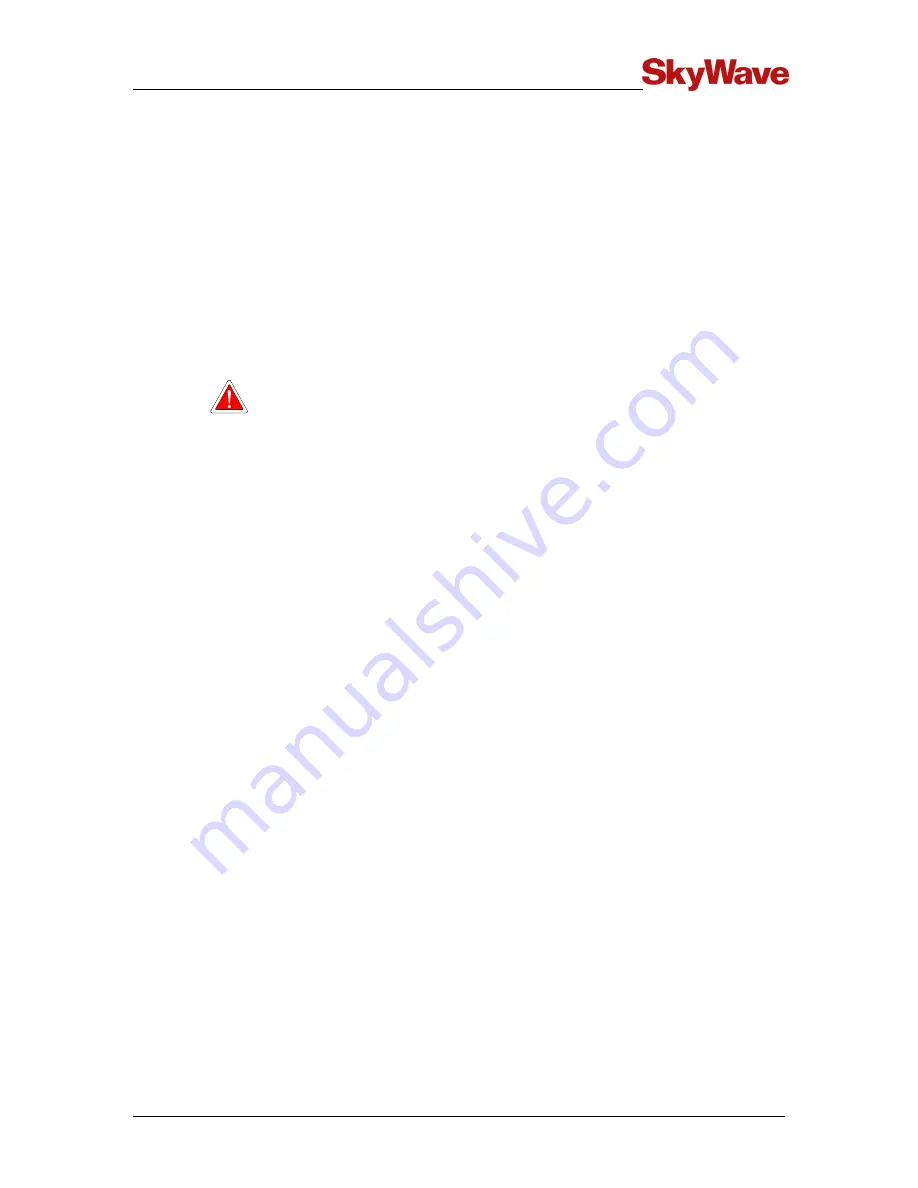
IDP 800 Terminal Series - Hardware Guide
T209, Version 01 48 © SkyWave Proprietary
Note:
The Solution Provider is responsible for providing mounting instructions if the
mounting is to be done using tools or configurations that are different from the
ones described in this document.
Note:
It is the installer’s responsibility to comply with local electrical codes.
Various options are available to mount the terminal:
Drill Mount (Section 4.6.1)
VHB Mount (APPENDIX F)
Custom Bracket Mount (Section 4.6.2)
4.6.1 Drill Mounting Holes
CAUTION
These steps are only needed if a mounting bracket is not used.
The mounting surface must be rigid and flat to prevent distorting
the terminal. Damage may otherwise occur.
1.
Use the terminal as a template to mark the location of the six mounting holes.
2.
Drill the six mounting holes using the drill with the 4.5 mm bit.
3.
Secure the terminal to the mounting surface through the drilled holes using the six
M4 (8-32) screws and torque to
1.4 N-m (12 in-lb)
.
4.
Continue with the steps, below, for Apply Dielectric Grease.
4.6.2 Custom Bracket Guidelines
SkyWave recommends customers follow the guidelines below if building their own
custom bracket.
All hardware must be 18-8 stainless steel.
The bracket should be either CRCQ steel (minimum 18 GA) outdoor power coat
with phosphate pre-treatment or aluminum (3 mm, 1/8” thick) with #8 stainless
steel PEM studs (16 mm, 5/8” long).
To prevent unnecessary mechanical stress the bracket must be sufficiently rigid
to maintain flatness or the terminal enclosure seal or structural integrity may be
compromised.
The bracket design must take into consideration the guidelines outlined in
Section 4.3.
The hardware used to secure the terminal must include a flat washer to spread the
fastener load, and a lock washer to prevent loosening under vibration.
Apply the recommended torque to the hardware used to secure the terminal.
The mounting bracket may also be designed to include features (such as a formed
bridge lance) that can be used to secure a cable, using a cable tie for connector
strain relief and cable management. This additional tie down feature is beneficial
where cable tie down points are not located on the asset near the terminal.
Once the bracket has been built, attach the terminal to the bracket before continuing with
the next section.