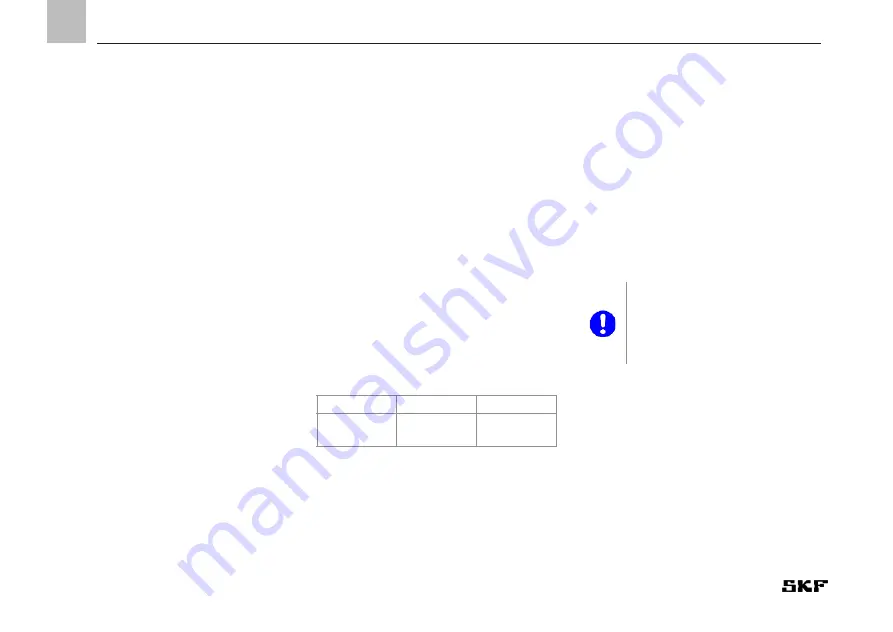
EN
10. Maintenance
- 44 -
951-171-016
Version 03
10.1 Maintenance of gear unit
The gear units are largely maintenance-free
and primed with synthetic oil. Carry out the
following activities in the indicated intervals
in order to avoid damages.
Every 500 working hours:
Visual control for leakages (radial sealing
ring)
Every 5 years:
Change the synthetic oil against new syn-
thetic oil of the same specification.
10.1.1 Required oil quality
Synthetic oil of the specification ISO VG 320
suitable for the operating temperature
range.
10.2 Motor maintenance
10.2.1 Inspection of the bearings
After a longer period of standstill or storage
the bearing grease of the motor must be
checked and replaced, if necessary, before a
new start-up.
10.2.2 Required grease quality
Lithium-saponified rolling bearing grease
suitable for the operating temperature
range.
10.2.3 Replacement of the bearing grease
Given normal load conditions (operation
at nominal speed and under normal envi-
ronmental conditions) replace the bearing
grease as follows.
Motor
bipolar
multipolar
service
hours
10,000
20,000
In case of deviating conditions, e.g. operation
with a frequency converter, the replacement
interval reduces in accordance with the per-
centage deviation of the actual speed from
the nominal speed of the motor.
To replace the bearing grease proceed as
follows:
• Implement the safety measures as speci-
fied in chapter 12 Repairs.
• Provide access to the bearing and remove
old grease from bearing.
• Clean the bearing with suitable solvents.
• Provide the bearing with new grease.
Fill only two thirds of the bearing
th grease. Filling the bearing and
the bearing lid fully with grease
increases the bearing tempera-
ture and results in higher wear.
• Properly reinstall the bearing lid and any
other detached parts again.
Содержание LINCOLN ZPU 01 Version E
Страница 57: ...Notes ...