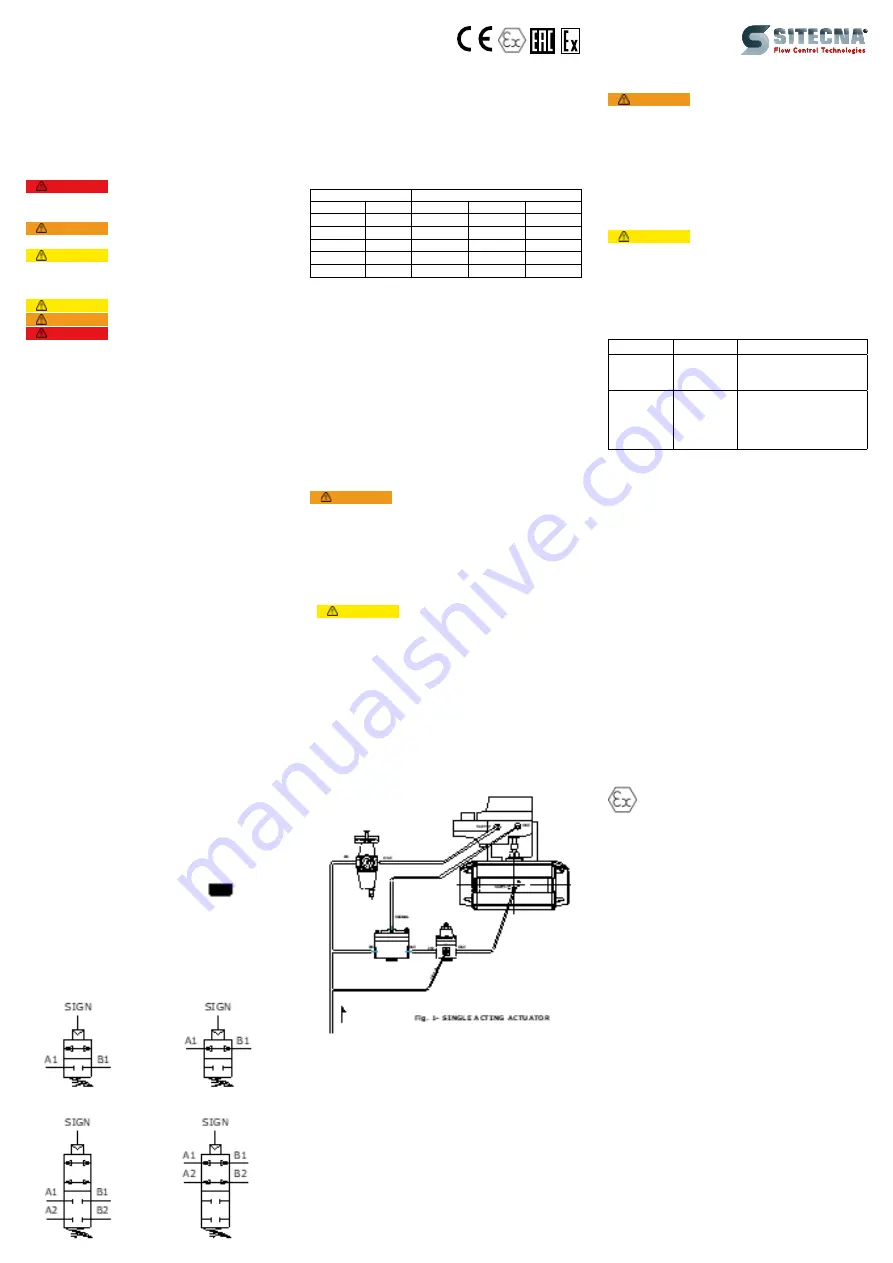
1.INTRODUCTION
Throughout this manual there are a number of HAZARD
WARNINGS that must be read and adhered to in order to
prevent possible personal injury and/or damage to equi-
pment. Three signal work “DANGER”, “WARNING” and
“CAUTION” are used to indicate the severity of a hazard,
and are preceded by the safety alert symbol.
Danger
Denotes the most serious hazard and is
used when serious injury or death WILL result from misuse
or failure to follow specific instructions.
Warning
Used when serious injury or death MAY
result from misuse or failure to follow specific instructions.
Caution
Used when injury or product/equipment
damage may result from misuse or failure to follow specific
instructions.
Caution
It is the responsibility and duty of
Warning
all personnel involved in the installation,
Danger
operation and maintenance of the equi-
pment on which this device is used, to fully understand the
procedures by which hazards can be avoided.
The compatibility of the product is the responsibility of
the person who designs the equipment or decides its
specifications.
Only personnel with appropriate training should operate
machinery and equipment.
Do not service or attempt to remove the machinery or
equipment until safety is confirmed.
2.DESCRIPTION
Lock Up Valve, LK04 sense the main supply pressure and
shuts down the air flow when the pressure is lower than set
-
ting level to avoid system shutdown or damages to pipeline.
3. OPERATION
When signal pressure is greater than setting pressure le-
vel, upper diaphragm (8) is pushed upward by signal pres-
sure. As it gets pushed upward, vent port through lower
diaphragm (10) opens, so signal pressure pushes down
lower diaphragm (10). Lower diaphragm (10) pushes pu-
sh-shaft (11) and push-shaft (11) pushes disk-seat (13),
which supplies pressure will vent out through Lock Up Val-
ve. Opposingly, when signal pressure is less than setting
pressure level, upper diaphragm (8) is pushed downward
and lower diaphragm (10) will block signal-in port. Ball (7)
will be detached from upper diaphragm (8) and the pressure
will be exhausted
AISI316 and Aluminum Alloy Lock-up valve - 1/4”NPT
INSTALLATION, REGULATION & MAINTENANCE INSTRUCTIONS
4. PNEUMATIC DIAGHRAM
Fig.2 Double lock-up
5. TECHNICAL FEATURES
Medium: compressed air, inert gases, sweet and sour gase-
Port thread: 1/4”NPT
Max suply pressure: 10 bar
Max signal/output: 7 bar
Materials: Body SS316L or copper free aluminum alloy
Internal parts Stainless Steel
MATERIAL
TEMPERATURE
DIAPHRAGM
SEALS
TRANSPORT
STORAGE
OPERATING
NBR
NBR
-20°C...+80°C -20°C...+80°C -20°C...+80°C
FKM
FKM
-25°C...+90°C -25°C...+90°C -25°C...+90°C
EPDM
EPDM
-40°C...+80°C -40°C...+80°C -40°C...+80°C
FVMQ
FVMQ
-55°C...+90°C -55°C...+90°C -55°C...+90°C
HNBR
HNBR
-55°C...+90°C -55°C...+90°C -55°C...+90°C
6.TRANSPORTATION & STORAGE
The preferred storage location is a clean, dry and protected
warehouse. If the components have to be stored outside,
precautions should be taken to keep valves clean and dry.
For storage temperatures, refer to the table in paragraph
“TECHNICAL FEATURS”.
To avoid contamination of impurities during the storage period,
don’t remove thread protection caps; remove them just before
the installation phase.
7. INSTALLATION
Warning
Before performing any work, read this ma-
nual and study all figures. Assure yourself that you understand
and you can do what is required in each step. Failure to follow
these instructions may affect quick release valve operation and
may result in exposure to personal injury.
Before installing the valve, set and block the machine or equi-
pment in a secure position; close the air shutoff valve and
exhaust air from air lines and disconnect all electrical power.
•
Caution
It is recommendable to check its condi-
tions before the installation.
• Install the Lock-up valve to achieve the desired switching re-
sults. Connect the control pressure line to either SIGN port.
The port labelled port A1 (single LK) A2 (double LK) is the
inlet connections and ports B1 (single LK) B2 (double LK) is
the outlet connections.
• Apply a good grade of pipe compound to the external pipe
threads before making connections, making sure not to get
the pipe compound inside the switching valves.
• Install tubing fitting or piping into the threaded NPT inlet and
signal connection on the body and into the threaded NPT
outlet connection.
8. TESTING
• With proper installation completed and downstream equi-
pment properly adjusted, slowly open the upstream and
downstream shut-off valve (when used) while using pressu-
re gauges to monitor pressure.
• If outlet pressure adjustment is necessary, monitor outlet
pressure with a gauge during the adjustment procedure.
The lock-up valve is adjusted by loosening the hex nut (20),
if used, and turning the adjusting screw (3) clockwise to in-
crease or counterclockwise to decrease the outlet pressure
setting. Retighten the hex nut to maintain the adjustment
position.
10. MAINTENANCE
Warning
Before performing any work, read this
manual and study all figures. Assure yourself that you un
-
derstand and can do what is required in each step. Failure
to follow these instructions may affect quick release valve
operation and may result in exposure to personal injury.
Before uninstalling the valve, set and block the machine or
equipment in a secure position; close the air shutoff valve
and exhaust air from air lines; disconnect all electrical power.
A.Ordinary maintenance
Caution
The LK should be periodically checked
for proper functioning:
• Clean the LK from impurities and dirt;
• Visually check of the integrity of the body and cup of LK;
• Check that there aren’t leakages;
• Check the correct functionality of the LK.
B. Troubleshooting
Issue
Possible Cause
Fixes
when the signal
is off, the valve
is open
valve seat
Check valve seat or contact
SITECNA technical support for more
information
leakage / high
bleed
bonnet or
retainer screws
valve o-ring
diaphragm
assemblies
Tighten the bonnet or retainer screws
If damaged, replace valve,
o-ring and diaphragm or contact
SITECNA technical support for more
information
11. MARKING ACORDING TO 2014/34/UEAtex
For using these equipment in potentially explosive atmo-
spheres, it is recommended - for the installation and the
maintenance operation - to use tools and instruments that
can produce only a single spark (for instance: screwdrivers,
spanners). Avoid use of tools that can produce sparks like
disk saw or grinder
Action must be taken to put to earth the units through a su-
itable connection, checking that all the metal components
(fittings and pipe line) have to be equitable potential.
Equipment have to be installed in the corresponding zone
according to the marking.
II 2G Ex h IIC T6/T5 Gb X
II 2D Ex h IIIC T85°C/T100°C Db X
After replacing the LK “TESTING” phase
Fig.1 Single Lock-up
C. Disassembly
• Disassemble in general accordance with the item
numbers on exploded view.
D. Mantainance
1. Place the diaphragm assembly (8) on the body
(13) for single LK or (23) for double LK. Push down
on the diaphragm assembly.
2. Stack the ball (7) and control spring (6) onto the
diaphragm assembly (7).
3. Install the cover (2) and screw adjusting (3) on the
body.
4. Install the six screws (4).
5. Lubricate the adjusting screw (3).
E.Assembly
• Assemble in general accordance with the item
numbers on exploded view.
NOTE: special conditions for safe use (X conditions)
Before performing any work, read this manual and assure
yourself you understand. X at the end of ATEX sobstitutes
T amb for series VB, DP, VSR, RF, LK, SCLP, T F, FLGSS, VP,
SLHF, SLVP, SLSC, PV. T amb depeends on used seals,
based on the following correspondance:
NBR=-20°C...+80°C, FMK=-25°C...+90°C,
EPDM= -40°C...+80°C, FVMQ & HNBR= -55°C...+90°C