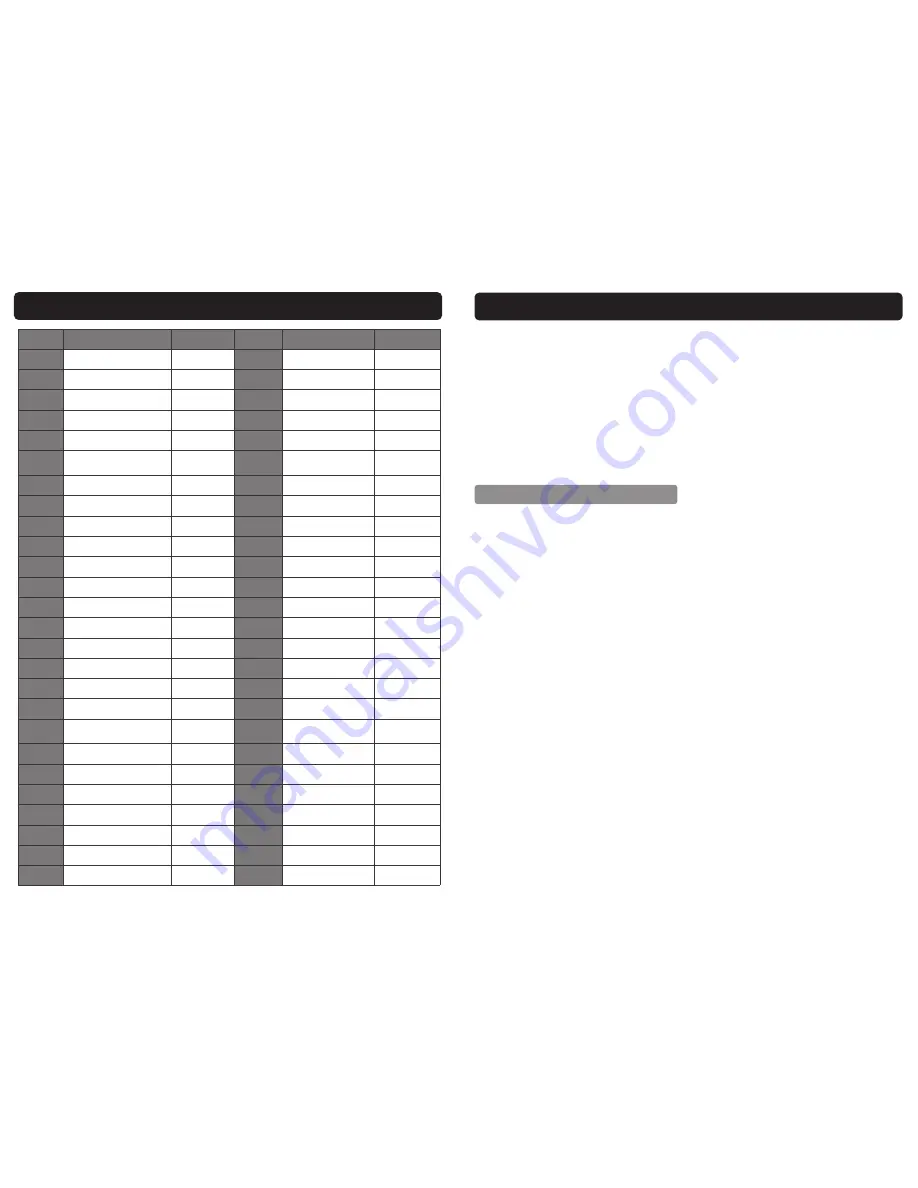
28
Ref. No.
Description
Sip Part No.
Ref. No.
Description
Sip Part No.
1.
Support for wire feeder
WE02-00308
27.
Output load small PCB WE02-00334
2.
Top cover
WE02-00309
28.
Output busbar
WE02-00335
3.
Power transformer
WE02-00310
29.
Front panel
WE02-00336
4.
power filter
WE02-00311
30.
Plastic frame surround WE02-00337
5.
Main PCB
WE02-00312
31.
Dinse socket
WE02-00338
6.
Mounting plate
WE02-00313
32.
Wire feed Control
socket-6 Pin
WE02-00339
7.
3 Phase rectifier bridge
WE02-00314
33.
Potentiometer knob
WE02-00340
8.
Gas bottle retaining chain WE02-00315
34.
Handle
WE02-00341
9.
Mains power cable
WE02-00316
35.
Control panel
WE02-00342
10.
Cable gland
WE02-00317
36.
Output reactor / choke WE02-00343
11.
back pane
WE02-00318
37.
Inductance Filter
WE02-00344
12.
Leakage protection switch WE02-00319
38.
left side panel
WE02-00345
13.
Switch bracket
WE02-00320
39.
Main transformer
WE02-00346
14.
Fan
WE02-00321
40.
Heatshield
WE02-00347
15.
Perspex Insulating Screen WE02-00322
41.
Heatshield insulator
WE02-00348
16.
right-side plate
WE02-00323
42.
IGBT
WE02-00349
17.
Heatsink
WE02-00324
43.
IGBT busbar
WE02-00350
18.
Fast Recovery Diode
WE02-00325
44.
Common inductor
WE02-00351
19.
Output rectifier board
WE02-00326
45.
Wire feed PCB
WE02-00352
20.
Rear wheel - single
WE02-00327
46.
PWM PCB
WE02-00353
21.
Bottle carrier
WE02-00328
47.
Capacitor fixing panel WE02-00354
22.
Heatsink bracket
WE02-00329
48.
Capacitor filter
WE02-00355
23.
Bottom
WE02-00330
24.
Bottom baffle plate
WE02-00331
25.
Swivel Castor wheel
WE02-00332
26.
Heatsink Insulator
WE02-00333
PARTS LIST - WELDING INVERTER 05776
9
SAFETY INSTRUCTIONS….cont
Ventilation must be adequate to remove the smoke and fumes during welding
(see the relevant safety standard for acceptable levels).
Toxic gases may be given off when welding, especially if zinc or cadmium coated
materials are involved, welding should be carried out in a well ventilated area
and the operator should always be alert to fume build-up.
Areas with little or no ventilation should always use a fume extractor.
Vapours of chlorinated solvents can form the toxic gas phosgene when exposed
to U.V radiation from an electric arc. All solvents, degreasers and potential
sources of these vapours must be removed from the arc area.
Severe discomfort, illness or death can result from fumes, vapours, heat, oxygen
enrichment or depletion that welding (or cutting) may produce. This will be pre-
vented by adequate ventilation or using a fume extractor.
NEVER
ventilate with
oxygen.
Lead, cadmium, zinc, mercury, beryllium bearing and similar materials when
welded may produce harmful concentrations of toxic fumes. Adequate ventila-
tion must be provided for every person in the area. The operator should also
wear an air supplied respirator, for beryllium both must be used.
Metals coated with or containing materials that emit toxic fumes should not be
heated unless coating is removed from the work surface. The area should be well
ventilated or the operator should wear an air supplied respirator.
Work in a confined space only while it is being ventilated and if necessary whilst
wearing an air supplied respirator.
Gas leaks in a confined space should be avoided, leaking gas in large quantities
can change oxygen concentration dangerously.
DO NOT
bring gas cylinders into
a confined space.
VENTILATION
Avoid oily or greasy clothing, a spark may ignite them.
Hot metal such as electrode stubs and work-pieces should never be handled
without gloves.
First aid facilities and a qualified first aid person should be available for each shift
unless medical facilities are close by for immediate treatment of flash burns to
the eyes and skin.
Flammable hair products should not be used by persons intending to weld.
Warn bystanders not to watch the arc and not to expose themselves to the weld-
ing arc rays or to hot metal.