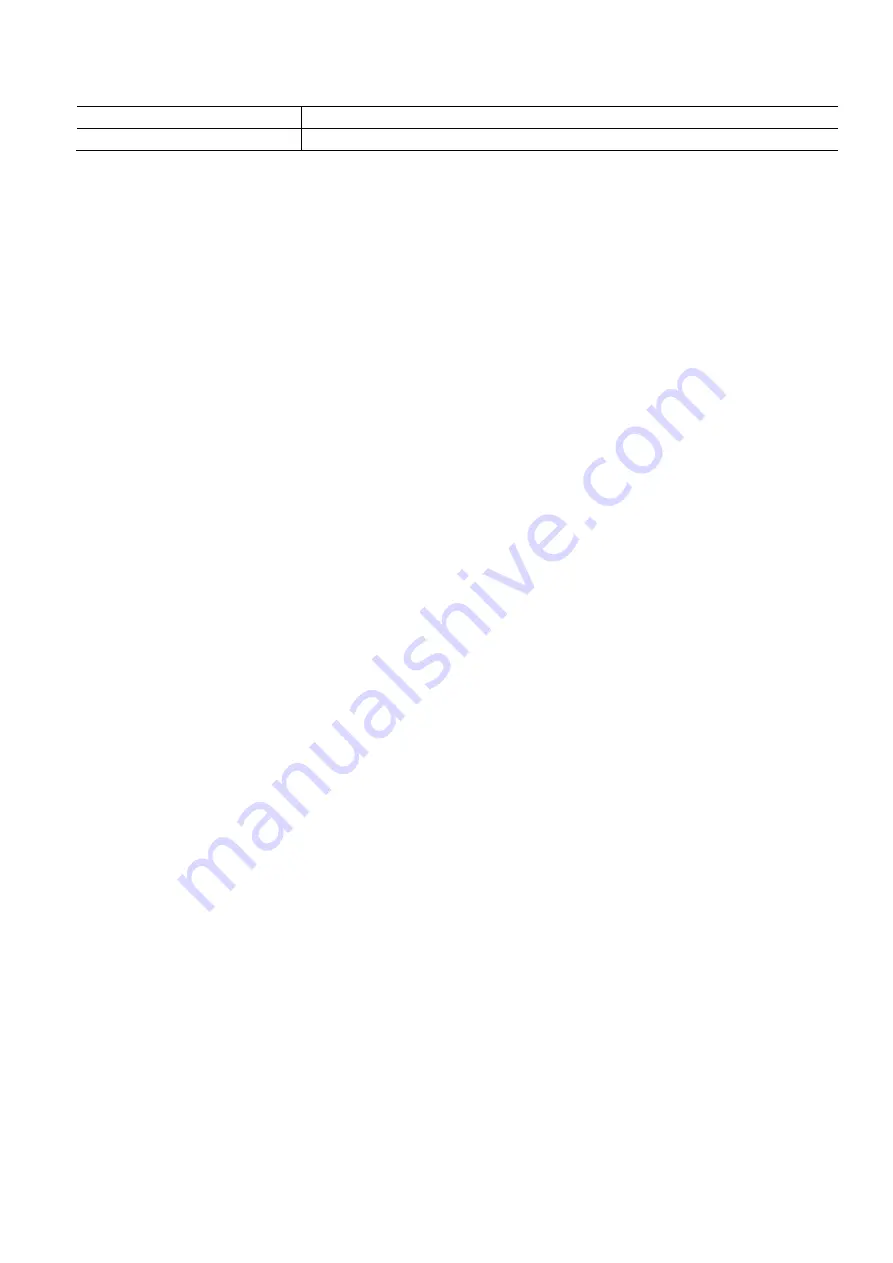
27
Water Level Gauge
Through external EMS
Diesel Generators
Through external EMS
6.4.1 Connecting the EMS over RS485 or Ethernet
EMS can choose to use RS485 or Ethernet access, depending on the user's specific application, as
shown in the figure below.
RS 485 Port
The front door of the storage converter is embedded with touch screen Management Unit. User
interface can be seen at its back. The position number of RS485 communication interface in the HMI (Touch
Screen) is J23. It is led to terminal strip ports 9 and 10. Users can transfer serial port signal to the one which
can be processed by PC via interface converter (such as RS485 transferred to RS232). The storage converter
could be set and commissioned alone via background software. It can read operation and warning
information. Corresponding settings, startup and shut down operations can be conducted.
Ethernet Port
The monitoring panel integrates Ethernet port with position numbered as RJ25 that can be seen in the back
of the touch screen. It supports Modbus TCP/IP protocol and has its own IP address. Ethernet connection
requires a switch router, and fixed IP needs to be set. Connecting cables are twisted pair (namely network
cable). The storage converter are connected to the switch router, and the switch router is connected to
remote control computer. The state of the storage converter can be monitored and controlled in real time
after setting IP address and port number in the monitoring computer.
6.4.2 Connecting a BMS over CAN
When directly connecting to the BMS, the communication port is default as CAN as shown below.
If the BMS use Ethernet communication port, a Ethernet-CAN protocol converter is needed . That
Ethernet-CAN protocol converter should be bought by the user and its beyound Sinexcel’s scope of
supply.
The DC-DC cabinet communicates with battery management unit (BMS) to monitor battery state
information, give an alarm and provide fault protection for battery according to the battery state and
improve the safety of storage battery. It supports CAN communication. In particular, the position
number of CAN communication interface can be seen in the back of HMI (Touch screen). It is led to
terminal strip ports 7 and 8.
6.5 Check after installation
After installation of PCS, please inspect all aspects according to the checklist in the Installation Manual.
Any failure to complete the checklist might void the warranty.
Содержание PDC-100K
Страница 1: ...User Manual DC DC Converter...