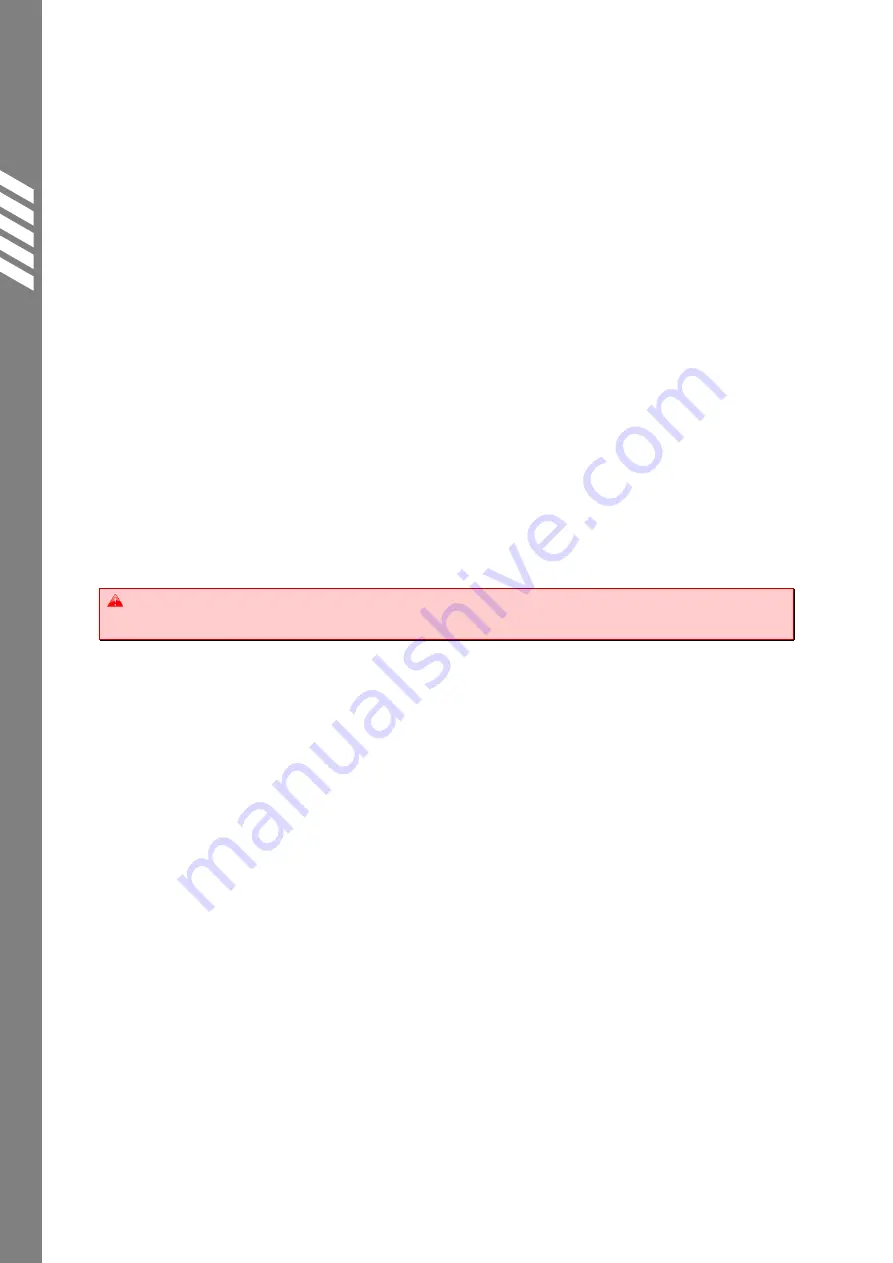
a.
The mast being bent or damaged, jamming one of the mast rollers.
b.
Part of the tipping track being bent or misaligned, interfering with the correct
movement of the tipping roller.
c.
A worn or misaligned tipping roller.
d.
Lack of lubrication of the rollers or mast sliding block.
e.
Poorly lubricated or broken lifting chains.
3.
With the cradle lowered, rectify the problem by lubricating, straightening and/or
realigning the mechanical components as required. If the mast or another major
component is bent, you may need to contact your agent for support.
4.
Test the machine to see if the cradle now lifts correctly. Run the machine through
several complete tipping cycles to ensure the problem has been fully resolved.
5.
If the machine is still not operating correctly, contact your agent.
3.4.2
Cradle jams while lowering
There are two types of problem which can prevent the cradle from lowering when the
LOWER button is pressed:
electrical
and
mechanical
faults.
3.4.2.1
Electrical fault
When the LOWER button is pressed, the motor contactor
should emit a ‘click’ sound. If it does
not, the problem is likely be an electrical fault. Observe the following procedures to rectify
the problem.
This procedure should only be carried out by an authorized, certified electrician,
following 3-phase electrical safety procedures.
1.
Open the control cabinet cover.
2.
Using a multimeter, check that the motor contactor is receiving an electrical signal. If
not, check the wiring and repair any breaks.
3.
Test the machine to see if the cradle now lifts correctly. Run the machine through
several complete tipping cycles to ensure the problem has been fully resolved.
4.
If the machine is still not operating correctly, contact your agent.
3.4.2.2
Mechanical fault
If the cradle starts to move but jams, the problem may be a mechanical fault. Observe the
following procedures to rectify the problem.
1.
If possible, lower the cradle to ground level and remove the bin.
2.
Attempt to visually identify the cause of the jamming. The most likely problems are:
a.
The mast being bent or damaged, jamming one of the mast rollers.
b.
Part of the tipping track being bent or misaligned, interfering with the correct
movement of the tipping roller.
c.
A worn or misaligned tipping roller.
d.
Lack of lubrication of the rollers or mast sliding block.
e.
Poorly lubricated or damaged lifting chains.
3.
With the cradle lowered, rectify the problem by lubricating, straightening and/or
realigning the mechanical components as required. If the mast or another major
component is bent, you may need to contact your agent for support.