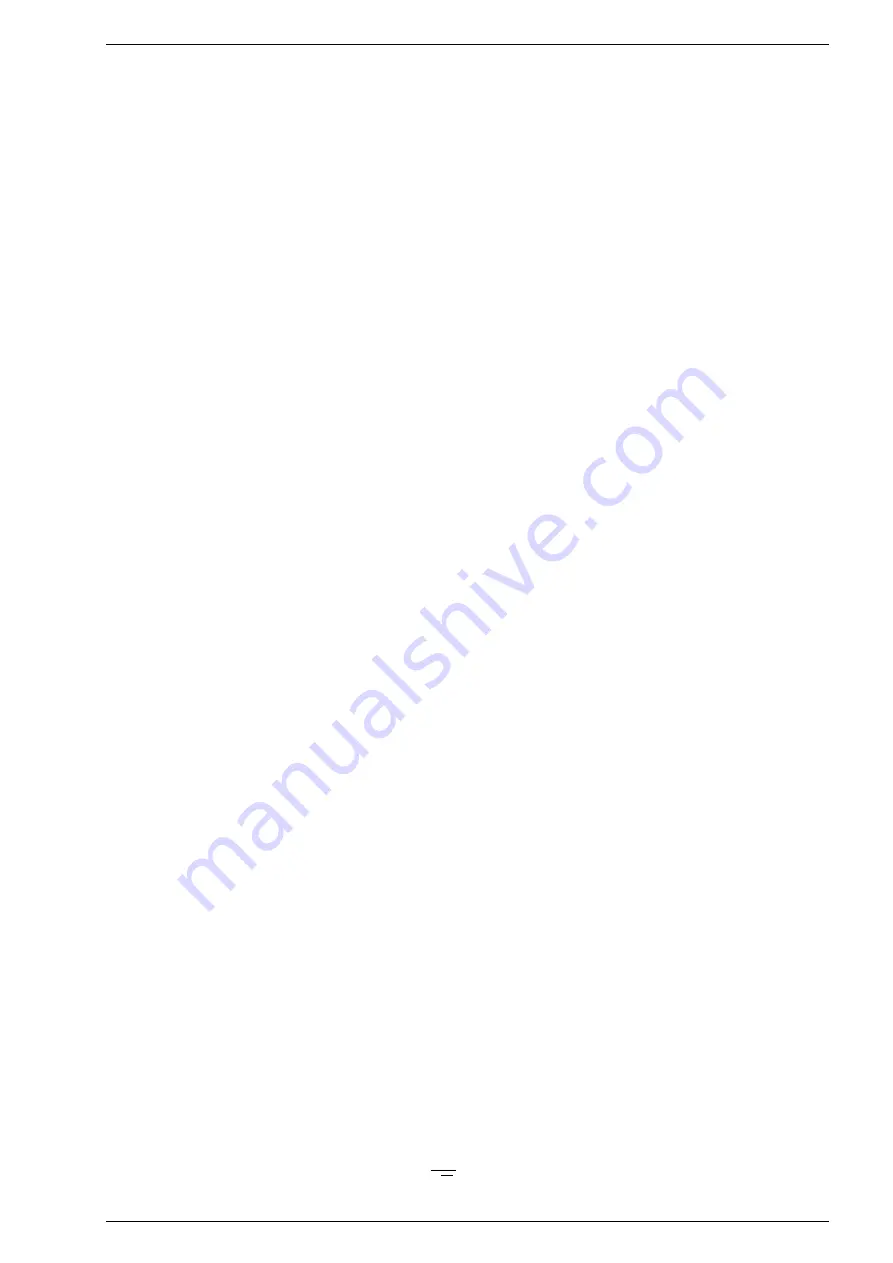
2.1
BOILER ROOM
The boiler room should feature all the char-
acteristics required by standards governing
liquid fuel heating systems.
2.2
BOILER ROOM
DIMENSIONS
Position the boiler body on the foundation
bed, which should be at least 10 cm high.
The body should rest on a surface allowing
shifting, possibly by means of sheet metal.
Leave a clearance between the boiler and
the wall of at least 0.60 m, and between the
top of the casing and the ceiling of 1 m
(0.50 m in the case of boilers with incorpo-
rated D.H.W. tank).
The ceiling height of the boiler room should
not be less than 2.5 m.
2.3
CONNECTING
UP SYSTEM
When connecting up the water supply to
the boiler, make sure that the specifications
given in fig. 1 are observed.
All connecting unions should be easy to dis-
connect by means of tightening rings.
A closed expansion tank system must be
used.
2.3.1
Filling the
water system
Before connecting the boiler, thoroughly
flush the system to eliminate scale which
could damage the appliance.
Filling must be done slowly to allow any air
bubbles to be bled off through the air valves.
In closed-circuit heating systems, the cold
water filling pressure and the pre-charging
pressure of the expansion vessel should be
no less than or equal to the height of the
water head of the installation (e.g. for water
head of 5 meters, the vessel pre-charging
pressure and installation filling pressure
should be at least 0.5 bar).
2.3.2
Characteristics
of feedwater
Water supplying the heating circuit must
be treated in accordance with UNI-CTI
8065 standards.
It is absolutely essential to treat water in
the heating system in the following cases:
– For extensive systems (with high con-
tents of water).
– Frequent addition of water into the
system.
– Should it be necessary to empty the sys-
tem either partially or totally.
2.3.3
D.H.W. storage tank
The
ESTELLE HE
boilers may be matched
with the separate boiler units.
The glass enamelled D.H.W. storage tank
comes with a magnesium anode to protect
the boiler and an inspection flange for
checking and cleaning.
The magnesium anode must be checked
annually and replaced if it is worn.
Fit a safety valve calibrated to 6 bar on the
tubing of the cold water supply to the boiler
unit.
An case the system pressure is excessive
fit an appropriate pressure reducer.
If the safety valve calibrated to 6 bar fre-
quently intercepts, fit an expansion vessel
with a capacity of 8 litres and a maximum
pressure of 8 bar.
The tank should be of the membrane type,
made of natural rubber “caoutchouc”, which
is suitable for foods.
2.4
CONNECTING UP FLUE
The flue is of fundamental importance for
the proper operation of the boiler; if not
installed in compliance with the standards,
starting the boiler will be difficult and there
will be a consequent formation of soot, con-
densate and encrustation.
The flue used to expel combustion products
into the atmosphere must meet the follow-
ing requirements:
– be constructed with waterproof materi-
als, and resistant to smoke temperature
and condensate;
– be of adequate mechanical resilience and
of low heat conductivity;
– be perfectly sealed to prevent cooling of
the flue itself;
– be as vertical as possible; the terminal
section of the flue must be fitted with a
static exhaust device that ensures con-
stant and efficient extraction of products
generated by combustion;
– to prevent the wind from creating pres-
sure zones around the chimney top
greater than the uplift force of combus-
tion gases, the exhaust outlet should be
at least 0.4 m higher than structures
adjacent to the stack (including the roof
top) within 8 m;
– have a diameter that is not inferior to
that of the boiler union: square or rec-
tangular-section flues should have an
internal section 10% greater than that of
the boiler union;
– the useful section of the flue must con-
form to the following formula:
S
resulting section in cm
2
K
reduction coefficient for liquid fuels:
– 0.045 for firewood
– 0.030 for coal
– 0.024 for light oil
– 0.016 for gas
P
boiler input in kcal/h
H
height of flue in meters, measured
from the flame axis to the top of the
flue reduced by:
– 0.50 m for each change of direc-
tion of the connection union
between boiler and flue;
– 1.00 m for each metre of union
itself.
2.5
ELECTRICAL CONNECTION
(fig. 6)
The boiler is fitted with an electricity cable,
and requires a 1ph - 230V - 50Hz power
supply through the main switch protected
by fuses.
The room thermostat (required for
enhanced room temperature control)
should be installed as shown in fig. 6.
Connect the burner with the cable supplied.
NOTE: Device must be connected to an
efficient earthing system.
SIME declines all responsibility for injury
caused to persons due to failure to earth
the boiler.
Always turn off the power supply before
doing any work on the electrical panel.
38
P
S
= K
√
H
2
INSTALLATION