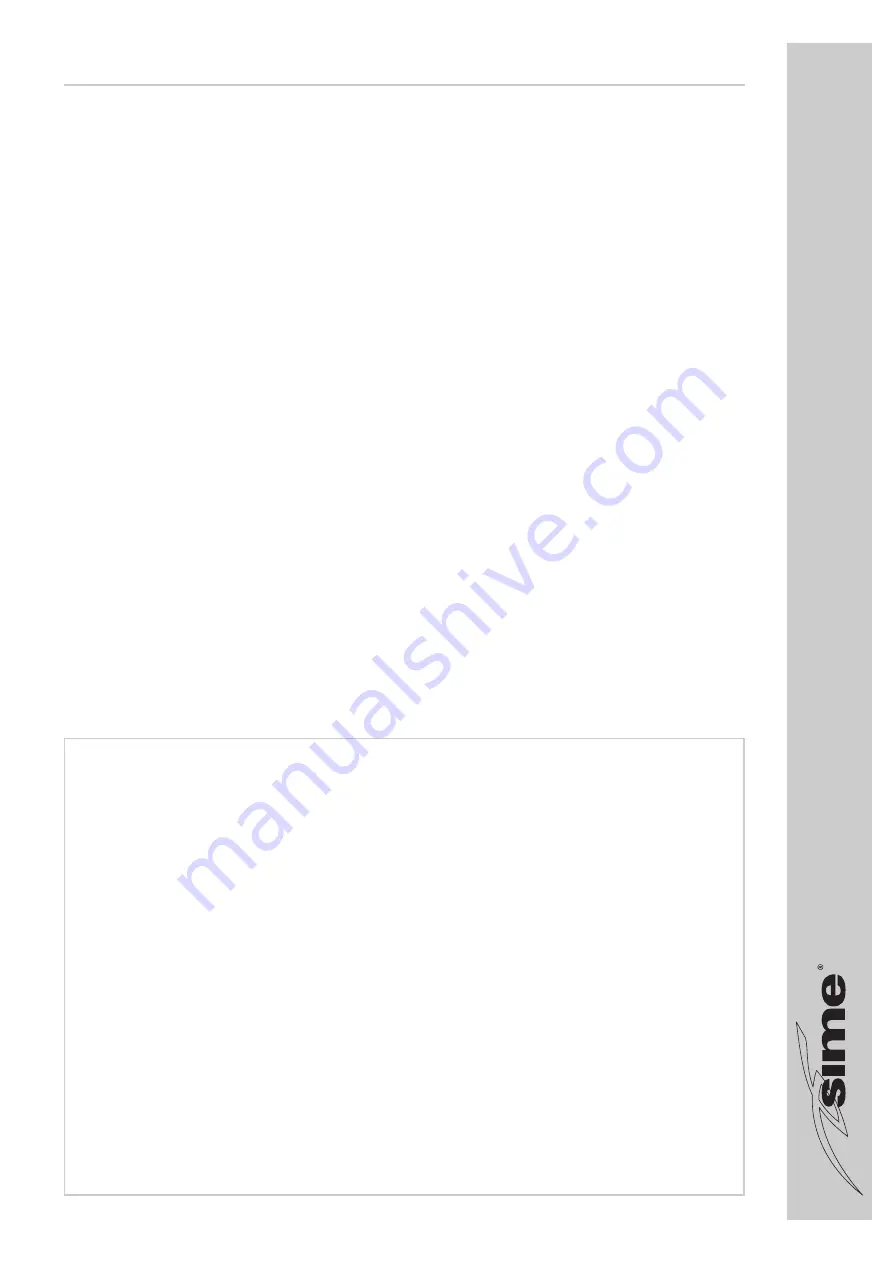
INSTALLER’S INSTRUCTIONS
CONTENTS
1
DESCRIPTION OF THE BOILER
. . . . . . . . . . . . . . . . . . . . . . . . . . . . . . . . . . . . . . . . . . . . . . . . . . . . . . . . . . . . . . . . . page 22
2
INSTALLATION
. . . . . . . . . . . . . . . . . . . . . . . . . . . . . . . . . . . . . . . . . . . . . . . . . . . . . . . . . . . . . . . . . . . . . . . . . . . . . . . . page 31
3
FEATURES
. . . . . . . . . . . . . . . . . . . . . . . . . . . . . . . . . . . . . . . . . . . . . . . . . . . . . . . . . . . . . . . . . . . . . . . . . . . . . . . . . . . . page 35
4
USE AND MAINTENANCE
. . . . . . . . . . . . . . . . . . . . . . . . . . . . . . . . . . . . . . . . . . . . . . . . . . . . . . . . . . . . . . . . . . . . . page 32
IMPORTANT
It is advisable to check the following before turning on the boiler for the first time:
– Check that there are no liquids or flammable materials in the immediate vicinity of the boiler.
– Check that all electrical connections are secure and that the earth wire is connected to a proper grounding
system.
– Open the gas cock and check the seal on all connections, including the burner connection.
– Check that the boiler is set up to run on the type of gas available.
– Check that the discharge channel of the combustion waste is free.
– Check that gate valves are open, if there are any.
– Check that the heating system has been filled with water and that air has been bled out of it.
– Make sure that the circulator is not blocked.
– Purge the system, bleeding off the air present in the gas pipe by operating the pressure relief valve on the
gas valve inlet.
FONDERIE SIME
Co. Ltd based in Garbo Str. 27, Legnano (VR) in Italy certifies that their high-temperature water
boilers are CE labelled according to the Gas directives 30/396/ CEE and are equipped with a safety thermostat,
with a maximum calibration of 110 C,; furthermore they are
excluded
from the field defined by the Directive PED
97/23/CEE because these products meet the requirements provided in the article 1 comma 3.6 of the same
Directive.
EK
O
OF - EN
GLIGH