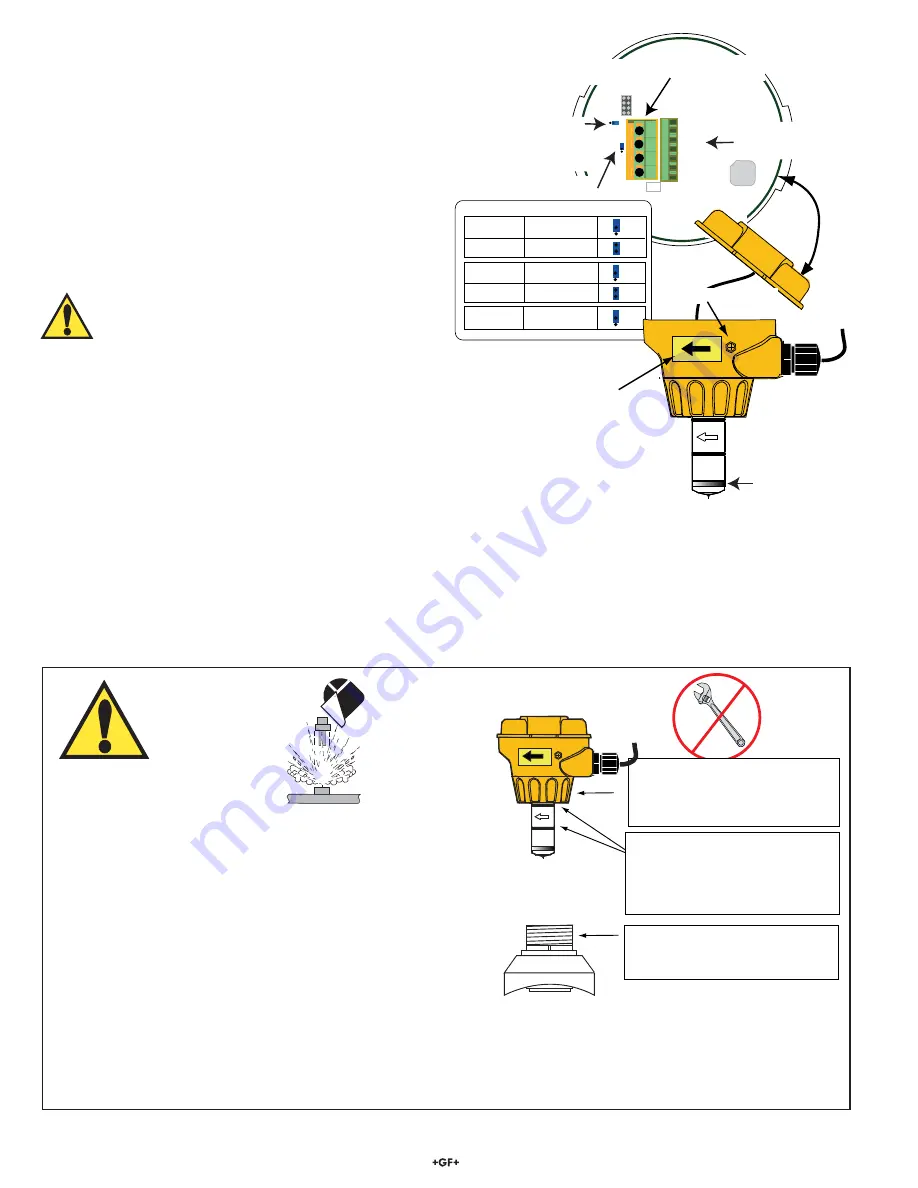
4
2551 Magmeter
Important:
•
The directional arrow on the sensor body MUST be pointed DOWNSTREAM for best performance.
•
The FLOW arrow decal can be placed directly on the pipe to identify the direction of
fl
ow.
•
Use a cable gland or a liquid tight connector to seal the cable ports from water intrusion.
•
The yellow housing may be reversed to align the conduit ports as required.
•
If the Magmeter is installed on a vertical pipe, the conduit ports should be turned to point downward.
This will prevent condensation from being channeled into the enclosure.
•
Use plumber's tape or a suitable sealant on cable ports.
5. Hardware
Con
fi
guration
Whether using the 2551-XX-11 (frequency or digital S
3
L output)
or the 2551-XX-12 (with 4-20 mA output), the wiring terminals
located on the inside of the yellow cover are identical. All of the
connections from the Magmeter to external equipment (PLC,
Datalogger, Chart Recorder, Flow meter, etc.) are made at the
large 4-position terminal connector.
When the cover is removed the wiring from the sensor can be
seen connected to the smaller terminal block. These connections
should always remain connected to prevent inadvertent damage
or miswiring.
The terminals on the 2551 Magmeter are designed for conductors
from 16 AWG to 22 AWG.
WARNING!
If the second conduit port is used, carefully drill the opening.
(The plastic is too strong to be punched out.)
•
Secure the Magmeter in a vise to prevent damage or injury.
•
The plastic inside the port is very thin. Do not allow the drill
to penetrate too deeply and damage the Magmeter wiring.
1
2
3
4
JP2
White
Yellow
Red
Black
Brown
Blue
Not used
The factory connects
the sensor cable to the termin
inside the yellow cover.
This blue jumper selects
frequency output or
S
L serial data output
in the 3-2551-XX-11
(Not used on 4-20 mA models)
3
The user must connect output cables to
this 4-terminal block.
JP2 is for factory use only.
MAKE NO CONNECTIONS.
Use the yellow decal to mark
the direction of flow on the pipe
Set this blue jumper according to the pipe size.
External Earth Ground Terminal
Sensor Type
Pipe Size
Jumper Position
2551-P0/T0/V0/W0
½ in. to 2½ in.
DN15
to
DN65
2551-P0/T0/V0/W0
3 in. to 4 in.
DN80
to
DN100
2551-P1/T1/V1/W1
5 in. to 6 in.
DN125
to
DN150
2551-P1/T1/V1/W1 8
in.
DN200
2551-P2/T2/V2/W2
10 in. to 12 in.
DN250
to
DN300
Sensor grounding ring
3-9000.392-1
Liquid tight connec
(one supplied)
Flow
FAILURE TO FOLLOW THESE INSTRUCTIONS MAY RESULT IN
THE SENSOR BEING EJECTED FROM THE PIPE!
•
DO NOT USE ANY TOOLS ON THE RETAINING CAP. HAND
TIGHTEN ONLY.
•
THE O-RINGS CAN BE LIGHTLY LUBRICATED TO FACILITATE
INSERTION INTO THE PIPE FITTING. DO NOT USE
PETROLEUM-BASED LUBRICANTS!
•
DO NOT USE THREAD SEALANT OR LUBRICANTS ON THE
RETAINING CAP OR ON THE PLASTIC FITTING THREADS.
•
IF LEAKING IS OBSERVED FROM THE RETAINING CAP, IT INDICATES DEFECTIVE OR WORN O-RINGS ON THE
SENSOR. DO NOT ATTEMPT TO CORRECT BY FURTHER TIGHTENING.
WARNING!
The O-rings can be lightly
lubricated to facilitate insertion
into the pipe fitting.
DO NOT USE petroleum-based
lubricants on O-rings!
DO NOT USE thread sealant
or lubricants on the fitting
threads.
Do not use any tools to
tighten the yellow retaining cap.
DO NOT USE thread sealant or
lubricants on retaining cap!
Flow