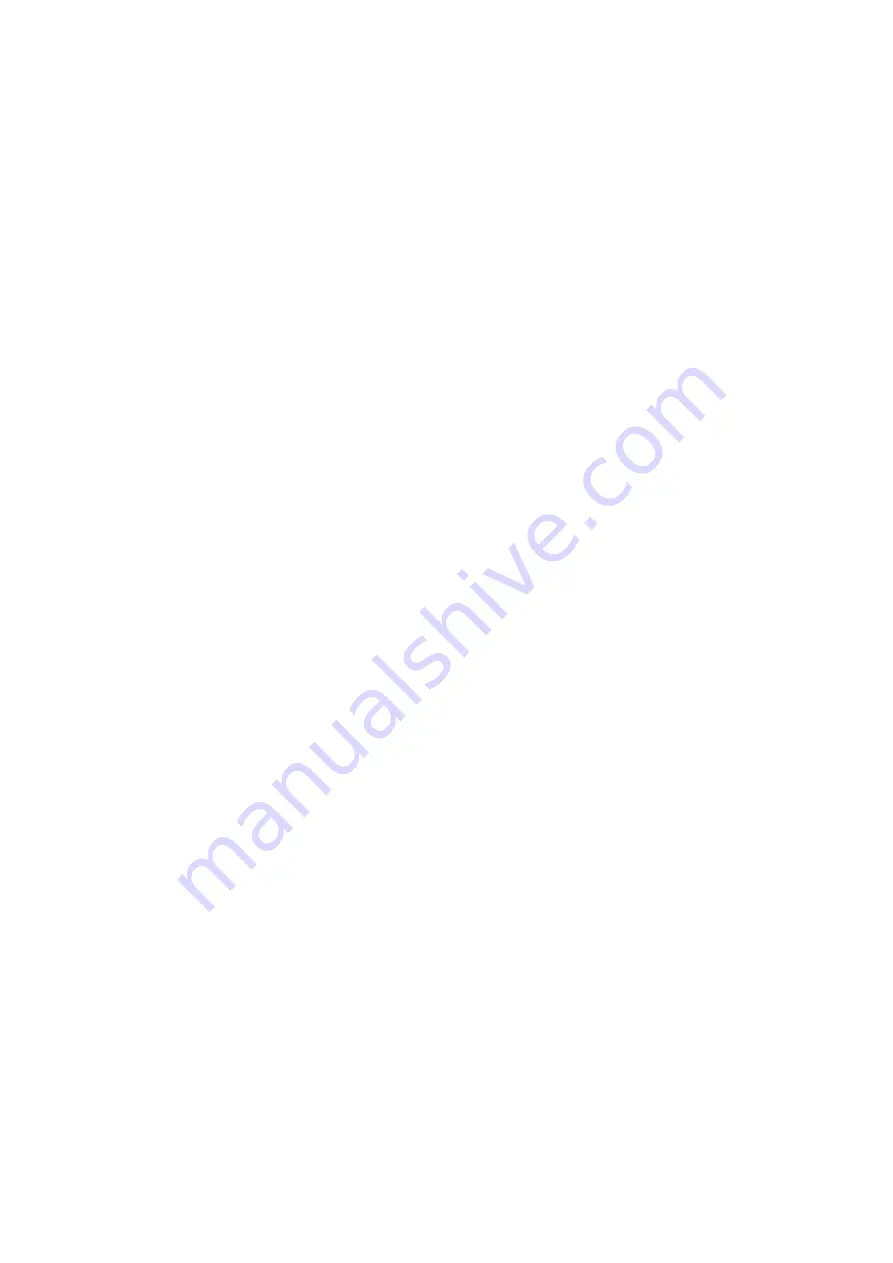
Page
16
Document Number: 0072
Rev. 09
CONTROLLED COPY
8.1.5 Stab Plate Connectors
•
Compliance
One half of a stab mate connector pair must be allowed to float so that misalignment tolerances
can be accommodated.
•
Mate/De-Mate Speed
The connectors have been designed to operate across a wide range of mate / de-mate speeds
with POWER OFF. There is no practical limit to the speed at which the connectors maybe
mated or de-mated, however as a guide:
a) Mating speed should not exceed 1 m/s.
b) De-mating speed should not exceed 5 m/s
•
Pre-Mating Checks
Before mating, the receptacle connector should be checked for debris. The connectors have
been designed to accommodate sand and silt contamination, however large pieces of debris
should be removed using a water jet.
•
Partial Disconnection
Partial disconnection with the contact pin remaining between the primary and secondary
diaphragms is not recommended. In this condition the level of insulation between the contact
pin and socket contact is reduced and the connector is relying on the primary seals within the
plug. There is also an increased risk of insulation break down at increased voltages.
•
Interrupted Connection
Interrupted connection (i.e. Partial mate to full de-mate) can be carried out without any adverse
affect to connectors, as long as the power is off.
•
Cathodic Protection:
Stainless steel 316L (UNS S31603) connectors must be connected to the CP (Cathodic
Protection) system at all times. Siemens recommends that Super Duplex stainless steel (UNS
S32550) connectors are isolated from the CP system to reduce the possibility of hydrogen
embrittlement.
Содержание SpecTRON 5
Страница 1: ......