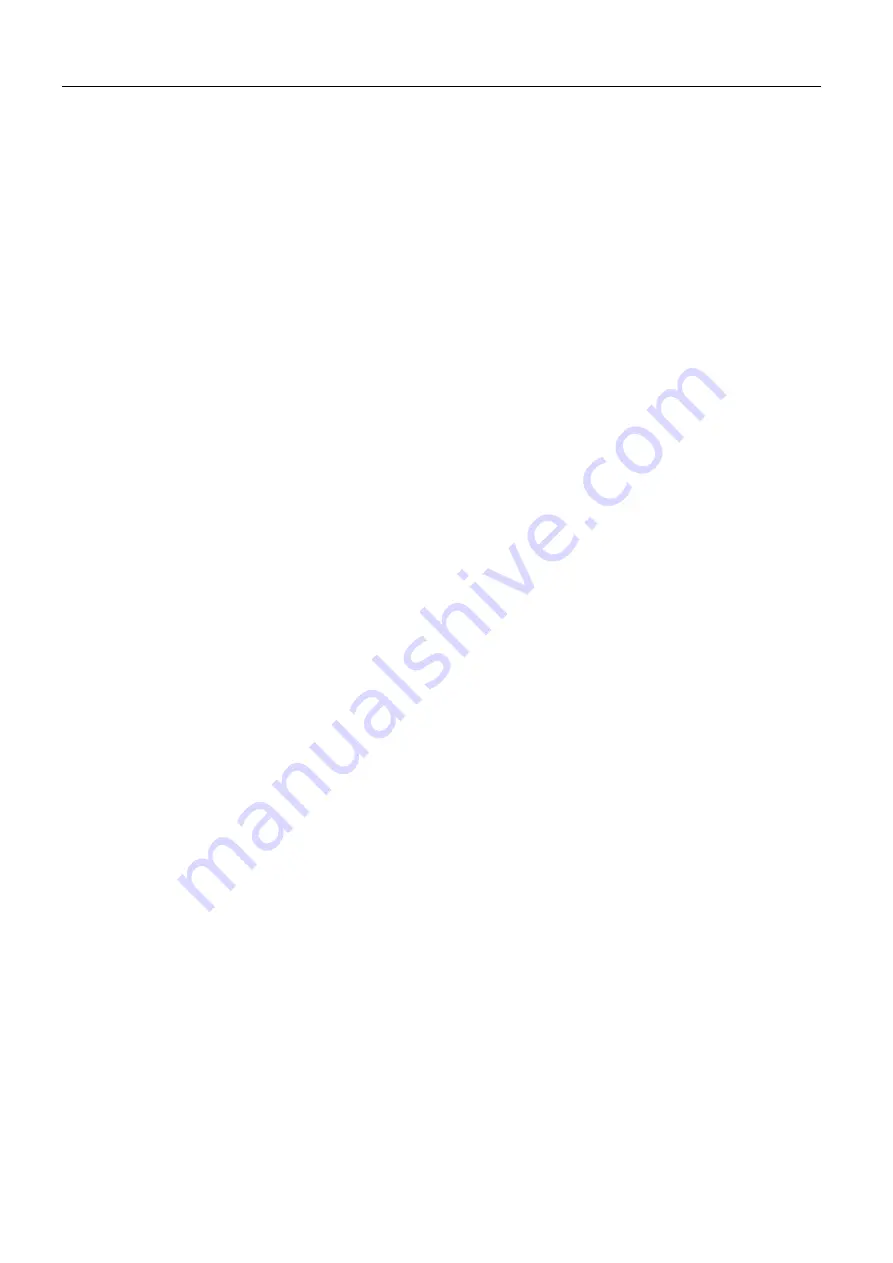
Installing/connecting
SITRANS FPS200
16
Operating Instructions, 08/2019, A5E46744245-AB
For flow rate measurement in humid gases, installation of separators and discharge valves is sensible to catch and
remove the condensate.
5.6.4
Installation position and piping for measurement in steam
For flow rate measurement in steam use two condensation vessels. They must be at the same height. Usually, the
condensation vessels as well as the initial shut-off valves are part of the delivery of primary elements for steam.
Dependent on pressure and temperature, initial shut-off valves for the connection of the differential pressure pipes
dispose of a cutting-ring or a welding connection. The differential pressure transmitter (not always included in the
delivery) should be installed below the pipe. The differential pressure pipes have to be strictly monotonic decreasing
from the primary element to the differential pressure transmitter. The decline should indicate at least 4°. If the
differential pressure pipe is accurately dimensioned it is guaranteed that no air pockets falsify the measurement in
those pipes.
To guarantee a correct measurement, the lines between the differential pressure transmitter and condensate
vessels must be completely filled with water on either side (water seal).
Usually, the filling is effected by filling valves. To fasten the assembling, we recommend a 5-valve-manifold for
measurements in steam because the filling valves are integrative part of these equipments. For maintenance works,
additional valves as well as blowout valves can be used.
5.7
Check of the installation
After assembling, we recommend to confirm with another qualified person. Especially, the following points should
be checked:
•
Is the primary element damaged?
•
Is the identification of the primary element correct?
•
Do the temperature and pressure of the process, the ambient temperature, the scope of measurement, …
correspond to the specification of the device?
•
Is the indication of the flow direction on the primary element corresponding to the real flow direction?
•
Is the right positioning for the transmitter being chosen (according to the transmitter type, use and
specifications of the medium?
•
Is the right sealing according to process conditions being used?
•
Are all screws tightened up?
•
Are the differential pressure pipes assembled correctly and connected correctly between primary element
and differential pressure transmitter (+ and -)?
•
Are all screws of the differential pressure pipes and the shut-off-valves tightened up?
(This list may not be complete.)