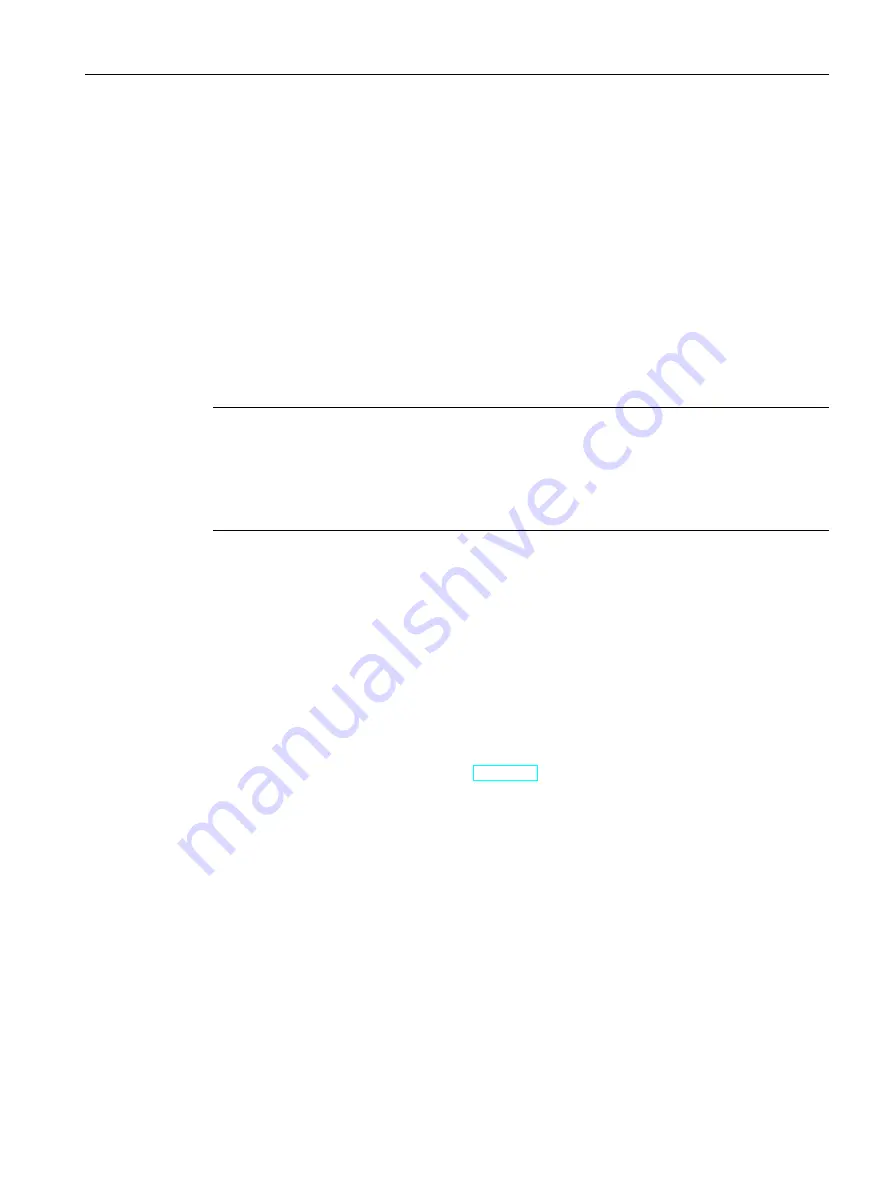
When you use the backup function of the master, the master automatically supplies the saved
parameters to the new device during device replacement.
You have the following setting options for device replacement:
• Backup&Restore
You have set the master port to Backup&Restore. The new device behaves as the replaced
device because the master has saved the last parameter change with the backup function.
• Restore
You have set the master port to Restore. The new device applies the parameter settings
that were saved in the master at the time of the last backup.
If you have made parameter changes since the last backup, these are not saved in the
master and are not available to the new device.
The behavior of the new device can deviate from the behavior of the replaced device. This
may be useful if you want to make short-term plant optimizations but do not want to save
them in the plant backup.
NOTE
Field calibration of sensors
When you are using sensors that must be adapted to specific rated conditions on site (field
calibration), you must repeat this calibration after replacing the device.
The backup does not include the data of the field calibration. After repeating the field calibra
tion, the new device works just like the replaced device.
Replacing a master
Replacing a master during operation is a rather rare scenario. Here, too, longer plant
downtimes are to be avoided. Replace a device quickly and avoid incorrect settings. Devices
can also be replaced by operators without special knowledge and aids.
You can save the configuration and parameter data of the master and the devices connected
to the master in the CPU and download this information to the new master after the
replacement.
When using an S7-CPU, you can use function blocks for this purpose.
You can find additional information on function blocks in the section Data access of the
automation system and the HMI device (Page 26).
29
Integration into the automation system
3.4 Replacing a master or device during operation
IO-Link system
Function Manual, 07/2022, A5E31637677-AC