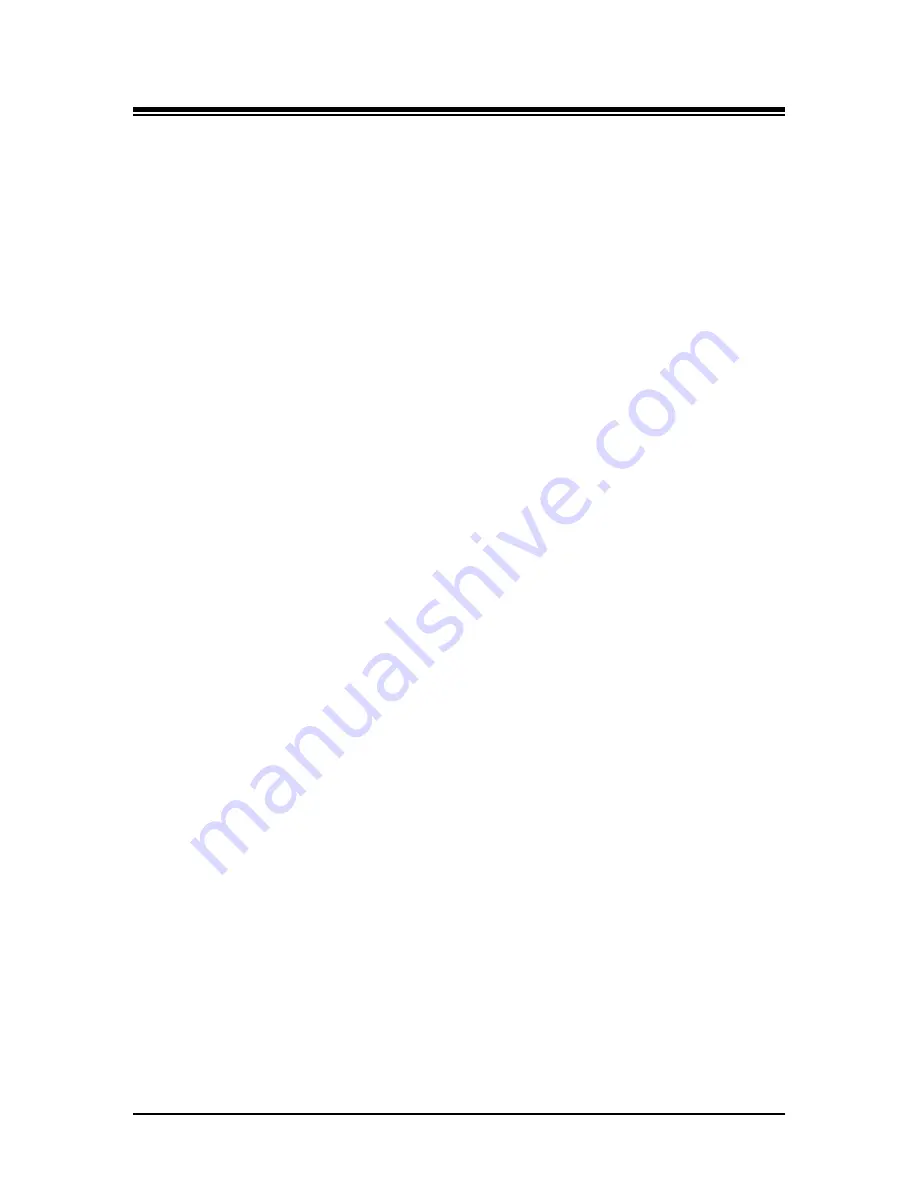
Turbine Package Operators Manual
Chapter 1
Turbine Package System Overview
1-7
Power Turbine Outer Casing and Interduct Assembly
The Power Turbine Outer Casing and Interduct Assembly are attached to the CT Center Casing
and Bearing Housing and the Spoke Frame Assembly. It provides the mounting for the PT1
Stator assemblies with the Exhaust Diffuser bolted to the Spoke Frame Assembly/PT Support
Assembly.
Power Turbine Bearing Housing
The exhaust diffuser and support assembly from the outer casing rigidly support the Power
Turbine Bearing Housing. The power turbine exit rotor shaft is supported in two tilting pad
journal bearings and provided with main and reverse thrust bearings.
Exhaust Diffuser
The lagged Exhaust Diffuser, mounted from the turbine pressure casing provides diffusion of the
exhaust gases for the exhaust ducting system.
Auxiliary Gearbox
The auxiliary Gearbox is mounted via an adapter ring directly off the gas generator inlet bearing
housing and driven from the gas generator shaft. It contains the necessary auxiliary drives for
the hydraulic starter motor and its associated clutch, and the main lubricating oil pump.
Cooling and Sealing Air System
Compressor air is used for sealing at labyrinth seals and cooling of high temperature
components. Refer to the
COOLING AND SEALING AIR SYSTEM DIAGRAM – SGT-400
(MW-2-1)
located in this Manual Volume. Medium pressure air, taken from the bleed band at
the seventh stage of the compressor, is used to:
•
Pressurize the inlet labyrinth seal.
•
Pressurize the labyrinth seals located either side of the compressor turbine journal
bearing to prevent stage ten high-pressure air entering the bearing housing.
•
Pressurize the labyrinth seals of the PT and cool the turbine discs.
Stage ten high-pressure bleed air taken from before the compressor exit guide vane is used to:
•
Balance the medium pressure air used to pressurize the labyrinth seals at the compressor
journal bearing.
•
Cool the turbine rotor discs and the interstage diaphragm.
Compressor exit air is used to:
•
Cool the CT1 and CT2 nozzle assemblies via holes in the nozzle inner and outer carrier
rings into the cooling tube of each nozzle followed by discharge into the gas stream by
trailing edge slots.
•
Cool the CT1 and CT2 rotor blades via their triple pass convection system prior to being
ejected into the gas stream.
Used medium pressure air is vented to atmosphere through the secondary breather system.
Used stage ten high-pressure air is vented into the exhaust system through the primary breather
system.