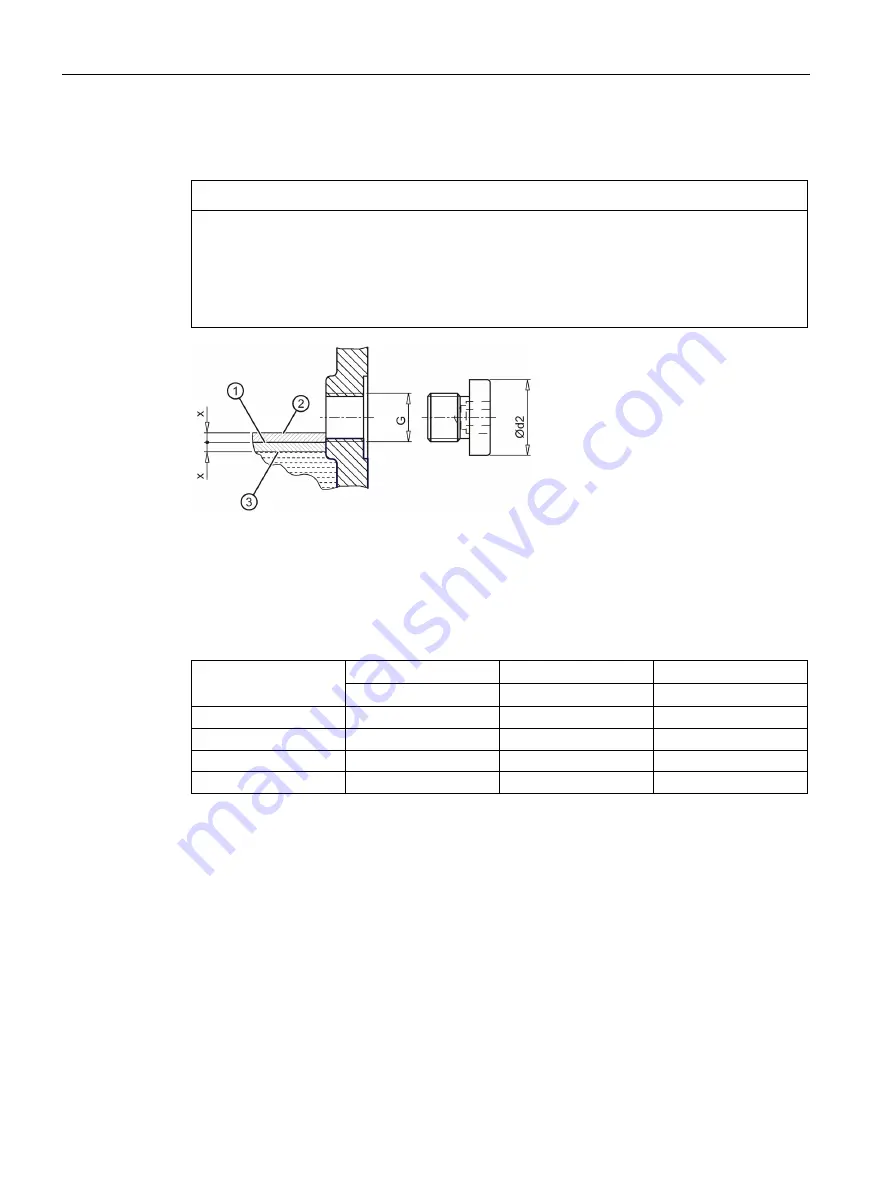
Service and maintenance
8.2 Checking and changing lubricants
BA 2515
44
Operating Instructions, 10/2016, A5E38123453A/RS-AB
8.2.2
Checking the oil level
NOTICE
The volume of gearbox oil changes with temperature
If the temperature rises, the volume increases. Where temperature differences and filling
quantities are significant, the volume difference can amount to several liters.
The oil level must therefore be checked while still slightly warm, approximately 30 minutes
after switching off the drive unit.
①
Specified oil level
②
Maximum oil level
③
Minimum oil level
Figure 8-1
Oil level in the gearbox housing
Table 8- 2
Minimum and maximum fill levels x
Oil level hole
∅
d2
Fill level x
Tightening torque
[mm]
[mm]
[Nm]
G 1/8"
14
2.5
10
G 1/4"
18
3
10
G 3/8"
22
4
25
G 3/4"
32
7
50
Procedure
1.
Switch off the power supply to the drive unit.
2.
Unscrew the oil level screw, see Mounting positions (Page 63). Oil escapes if the
maximum fill level is above the plug hole.
3.
Check the oil level. Observe the fill level x.
4.
Top up the oil level if necessary and check it again.
5.
Check the state of the sealing ring on the sealing element. If the sealing ring is damaged,
replace the sealing element with a new one.
6.
After checking, seal the gearbox immediately using the sealing element.
You have now checked the oil level in the gearbox housing.
Содержание MOTOX BA 2515
Страница 1: ......
Страница 2: ......
Страница 8: ...Table of contents BA 2515 8 Operating Instructions 10 2016 A5E38123453A RS AB ...
Страница 58: ...Disposal BA 2515 58 Operating Instructions 10 2016 A5E38123453A RS AB ...
Страница 75: ...Spare parts 11 2 Spare parts lists BA 2515 Operating Instructions 10 2016 A5E38123453A RS AB 75 ...
Страница 78: ...Declaration of Incorporation BA 2515 78 Operating Instructions 10 2016 A5E38123453A RS AB ...
Страница 79: ......
Страница 80: ......