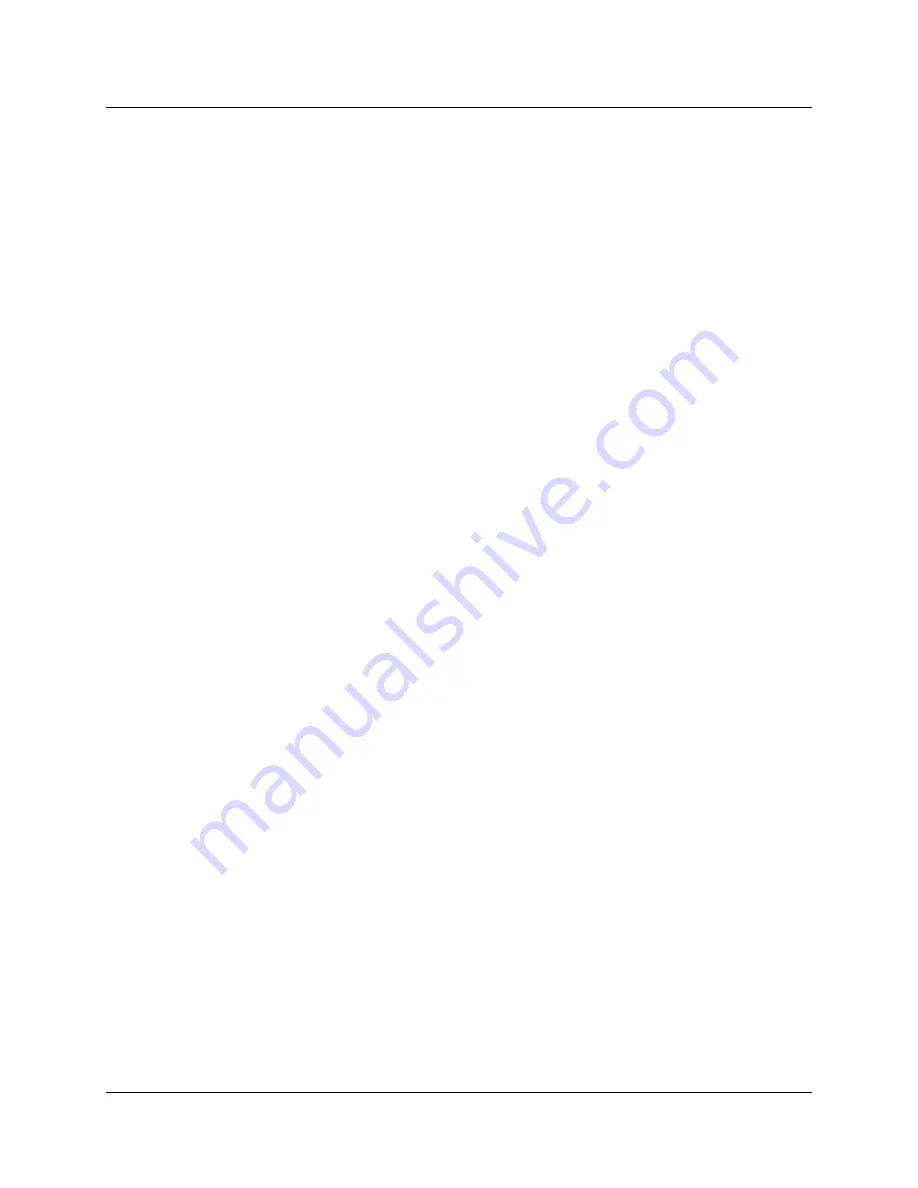
Technical Instructions
LMV Series
Document No. LV3-1000
Section 5
Page 8 SCC Inc.
2.
The stopping method (after the run / stop contact is opened) should be set to "Coast to Stop" to let
the motor coast to a stop after post-purge.
3.
Reverse operation (the ability to reverse the motor with an input) should be disabled.
4.
Configure the VFD to accept an external run / stop signal via a dry contact on the relay wired to the
LMV3 blower motor starter output.
5.
The VFD should be able to do a "flying start" so that the VFD will not try to stop a free-wheeling
blower wheel before starting the wheel spinning again. Blower wheels frequently free-wheel due to
draft and other factors.
6.
Ramp times - the VFD should be set to slightly faster ramp times compared to the LMV3 ramp times
(LMV3 parameters
522 Ramp Up VSD, 523 Ramp Down VSD
and
544 ModulationRamp
). For
example, if the LMV3 VSD ramp up time is set to 40 seconds, the ramp up time in the VFD should be
set no longer than 35 seconds. The same is true with the ramp down time. A 5 second differential
will work well in most situations.
Note: If short ramp times are necessary with large blowers (heavy blower wheels), a braking
resistor may be necessary. See the braking resistor explanation on the previous pages.
7.
Ramps must be linear with the 0-10 VDC signal. S-shaped ramps and PID / filtering on the 0-10 VDC
signal will cause speed faults on the LMV3.
8.
The VFD analog input signal should be configured for a 0-10 VDC signal and it should be spanned so
that 0 VDC = 0Hz and 10 VDC = 62 Hz (for blowers designed for 60 Hz power). The additional 2 Hz is
to make sure that full blower speed is achievable even with a 9.5 VDC standardization (see
standardization section below).
9.
The motor nameplate data must be entered for the motor that the VFD is connected to.
10.
Some VFDs have a feature that will stop ramping the drive if a critical limit in the drive is
approached. On some VFDs, this feature is referred to as "stall prevention". Two common limits are
the maximum amperage drawn and the DC bus voltage. Stall prevention, while protecting the drive,
can cause speed faults with the LMV3 due to the drive ceasing to ramp in concert with the LMV3. If
a braking resistor is used, stall prevention can typically be deactivated.
11.
For Vector VFDs, perform at least a static auto-tune so that the VFD "learns" the characteristics of
the motor it is connected to. A static auto-tune does not require that the load (blower wheel) be
disconnected since the load is not spun. Some dynamic auto-tunes require that the load (blower
wheel) is disconnected.
12.
If a braking resistor is being used, the braking resistor will typically have a high temperature switch.
The drive should be programmed and wired so that a braking resistor over temperature will cause
the drive to shut down.
Содержание LMV3 series
Страница 1: ...Combustion Controls LMV3 Linkageless Burner Management System www scccombustion com ...
Страница 2: ...Intentionally Left Blank ...
Страница 18: ...Technical Instructions LMV Series Document No LV3 1000 Section 1 Page 14 SCC Inc Intentionally Left Blank ...
Страница 20: ...Technical Instructions LMV Series Document No LV3 1000 Section 1 Page 16 SCC Inc Intentionally Left Blank ...
Страница 26: ...Technical Instructions LMV Series Document No LV3 1000 Section 1 Page 22 SCC Inc Intentionally Left Blank ...
Страница 40: ...Technical Instructions LMV Series Document No LV3 1000 Section 2 Page 12 SCC Inc 2 4 Wiring Diagrams ...
Страница 41: ...LMV Series Technical Instructions Document No LV3 1000 SCC Inc Page 13 Section 2 ...
Страница 42: ...Technical Instructions LMV Series Document No LV3 1000 Section 2 Page 14 SCC Inc ...
Страница 43: ...LMV Series Technical Instructions Document No LV3 1000 SCC Inc Page 15 Section 2 ...
Страница 44: ...Technical Instructions LMV Series Document No LV3 1000 Section 2 Page 16 SCC Inc ...
Страница 45: ...LMV Series Technical Instructions Document No LV3 1000 SCC Inc Page 17 Section 2 ...
Страница 46: ...Technical Instructions LMV Series Document No LV3 1000 Section 2 Page 18 SCC Inc ...
Страница 76: ...Technical Instructions LMV Series Document No LV3 1000 Section 3 Page 28 SCC Inc Intentionally Left Blank ...
Страница 102: ...Technical Instructions LMV Series Document No LV3 1000 Section 4 Page 24 SCC Inc Intentionally Left Blank ...
Страница 158: ...LMV Series Technical Instructions Document No LV3 1000 SCC Inc Page 24 Section 6 Intentionally Left Blank ...
Страница 178: ...Technical Instructions LMV Series Document No LV3 1000 Section 7 Page 18 SCC Inc Intentionally Left Blank ...
Страница 190: ...Technical Instructions LMV Series Document No LV3 1000 Section 8 Page 10 SCC Inc Intentionally Left Blank ...
Страница 223: ...Intentionally Left Blank ...