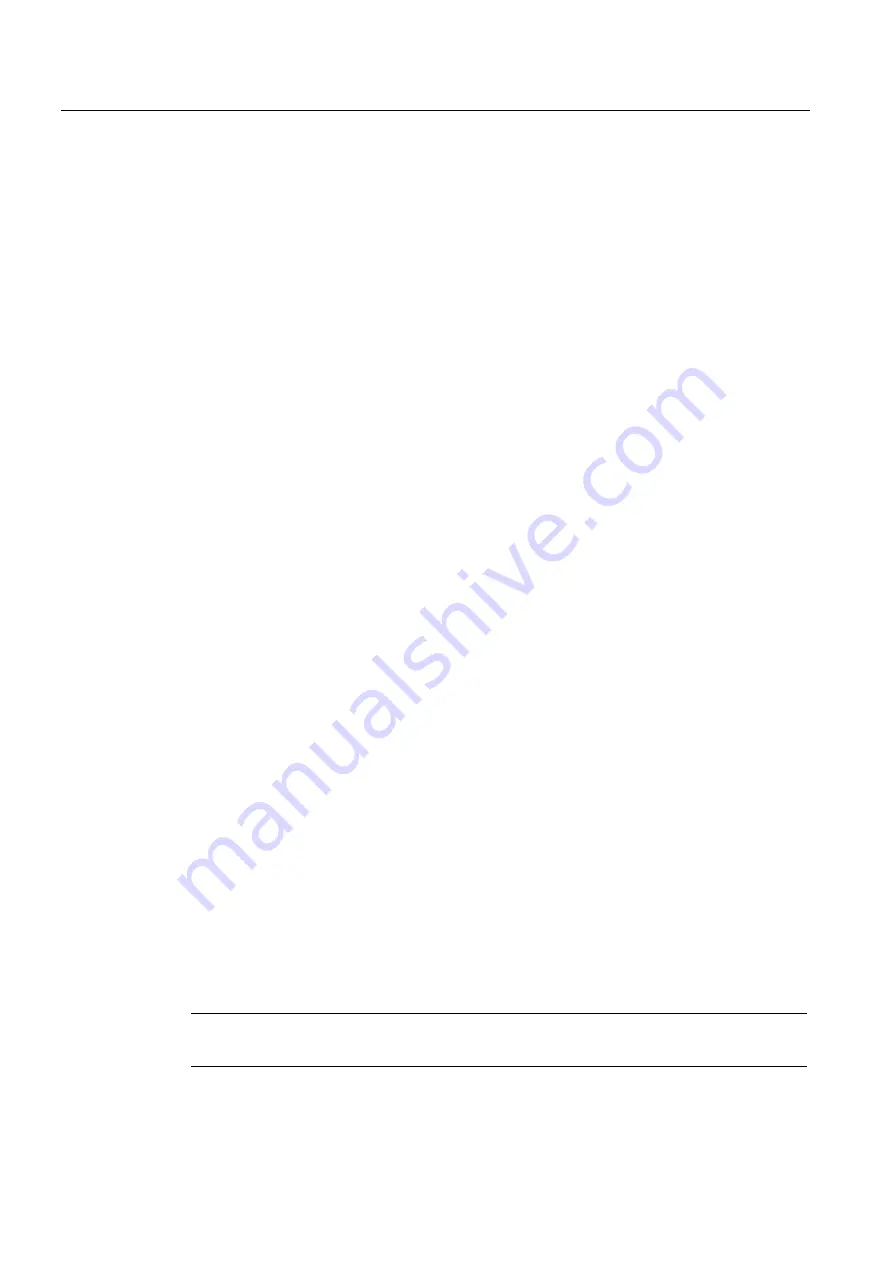
Functions
7.8 Logger Control
FUS1010 IP65 NEMA 4X & IP66 NEMA 7
126
Operating Instructions, 01/2013, A5E02951520-AC
4.
To transmit Logger contents to external device via the serial port press <ENTER>.
5.
To stop printout press <Left Arrow>.
Circular Memory
In its default mode, the Logger collects data until its memory becomes full. At that time the
flow meter suspends datalogging and cannot resume until the Logger memory is cleared
(see Clear Logger command). Circular Memory allows the Logger to "‘write over" its oldest
records when memory reaches full capacity. If you enable [Circular Memory], you are
assured of always collecting the most recent data. But also remember that you will lose the
oldest Logger reports and that further invoking of [Circular Memory] deletes the current
contents of the Logger.
To setup and enable Circular Memory:
1.
The Logger Mode menu must have the [Memory] menu cell selected.
2.
Logger items must be selected (e.g., Site ID, Date, Time, etc.).
3.
All active channels/paths in the Channel Setup menu must be disabled. To disable active
channels, select the [Channel Enable] menu cell and then [No].
4.
In the Logger Control menu, select [Circular Memory].
5.
Press <Right Arrow> to access the [Circular Memory] option list.
6.
Move the cursor to [Yes] by pressing <Up/Down Arrow>.
7.
To store selection press <ENTER>.
8.
Lastly, re-enable the channels/paths that you disabled earlier to begin logging.
Est LogTime Left
Est LogTime Left is a "view-only" menu cell that shows an estimate of the amount of Logger
time remaining in hours and minutes. This menu cell becomes active after you enable
datalogging. Selecting [Circular Memory] and/or event-based datalogging (see Logger
Setup), blanks the [Est LogTime Left] field and is based on the log interval and data
selections made in the Logger Setup.
Clear Logger
If you use the Logger in its default mode, eventually you will use all the memory available for
Logger storage. When this occurs, you will not be able to log more data until you free up the
memory. The [Clear Logger] command erases ALL stored Logger data. Therefore, you
should evaluate the currently stored data, and print any valuable information before using
this command.
Note
Saved Sites also consume Logger RAM.
Содержание FUS1010
Страница 83: ...Connecting 5 7 Sensor Wiring FUS1010 IP65 NEMA 4X IP66 NEMA 7 82 Operating Instructions 01 2013 A5E02951520 AC ...
Страница 153: ...Functions 7 14 Reflexor FUS1010 IP65 NEMA 4X IP66 NEMA 7 152 Operating Instructions 01 2013 A5E02951520 AC ...
Страница 224: ......
Страница 225: ......
Страница 226: ......
Страница 227: ......
Страница 228: ......
Страница 229: ......
Страница 230: ......
Страница 231: ......
Страница 232: ......
Страница 233: ......
Страница 234: ......
Страница 235: ......
Страница 236: ......
Страница 237: ......
Страница 238: ......
Страница 239: ......
Страница 240: ......
Страница 241: ......
Страница 242: ......
Страница 243: ......
Страница 244: ......
Страница 245: ......
Страница 246: ......
Страница 247: ......
Страница 248: ......
Страница 249: ......
Страница 250: ......
Страница 251: ......
Страница 252: ......
Страница 253: ......
Страница 254: ......
Страница 255: ......
Страница 256: ......
Страница 257: ......
Страница 258: ......
Страница 259: ......
Страница 260: ......
Страница 261: ......
Страница 262: ......
Страница 263: ......
Страница 264: ......
Страница 265: ...21614 C 1011NFPS 7 ...
Страница 266: ...1011NFPS 7 C 21614 ...
Страница 267: ...1011NFPS 7 C 21614 ...
Страница 268: ...21614 C 1011NFPS 7 ...
Страница 269: ......
Страница 270: ......
Страница 271: ......
Страница 272: ......
Страница 273: ......
Страница 274: ...21614 C ...
Страница 275: ......
Страница 276: ......
Страница 277: ...1012TN 7 INSTALLATION DRAWING 1010 SERIES TRANSDUCERS AND MOUNTING TRACKS 21614 C ...
Страница 278: ...1012TN 7 INSTALLATION DRAWING 1010 SERIES TRANSDUCERS AND MOUNTING TRACKS 21614 C ...
Страница 279: ...1012TNH 7 INSTALLATION DRAWING 1010 SERIES TRANSDUCERS AND MOUNTING TRACKS 21614 C ...
Страница 280: ...1012TNH 7 INSTALLATION DRAWING 1010 SERIES TRANSDUCERS AND MOUNTING TRACKS 21614 C ...
Страница 281: ......
Страница 282: ......
Страница 283: ......
Страница 284: ......
Страница 285: ......
Страница 293: ...Glossary FUS1010 IP65 NEMA 4X IP66 NEMA 7 228 Operating Instructions 01 2013 A5E02951520 AC ...
Страница 297: ...Index FUS1010 IP65 NEMA 4X IP66 NEMA 7 232 Operating Instructions 01 2013 A5E02951520 AC ...