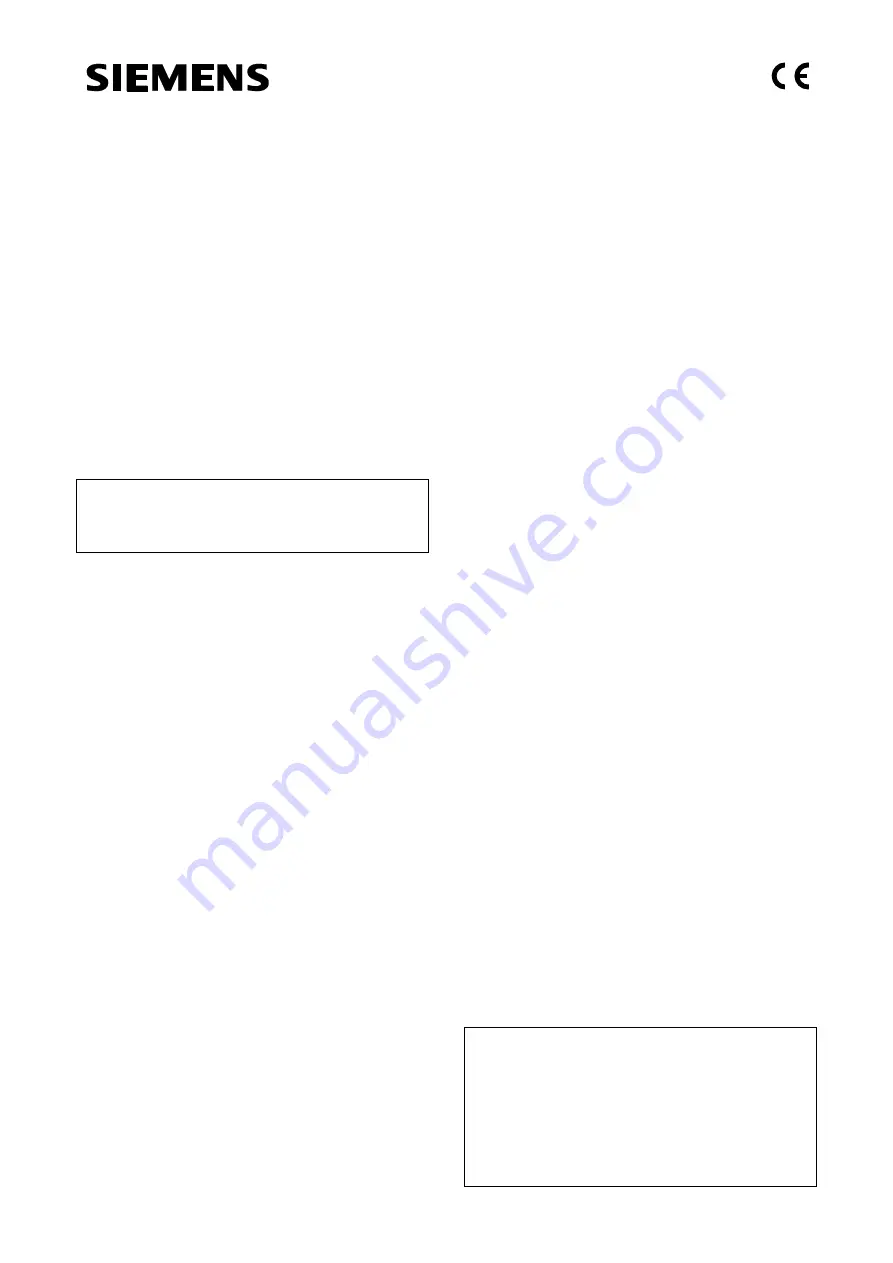
______________________________________________________________________________________
Siemens
Bestell-Nr./Order No. 2KG1900-3AA00-0AA0
5/15
04.2003
Deutsch / English / Français
Ident-N
r. 206 2
3
9 44
English
Information on safety and commissioning
for low voltage geared motors
(in accordance with L. V. Directive 73/23/EEC)
Angular geared motors
Type 2KG13
Sizes W1 to W0
1 General
information
This documentation must be read carefully before installing
and putting the product into operation. We assume no liability
for damage and malfunctions resulting from failure to comply
with these notes on safety.
Electric geared motors have dangerous voltage-carrying and
rotating components as well as surfaces that may become hot.
All work involved in the transport, connection, commissioning
and regular maintenance must be carried out by
qualified,
responsible specialists
(note VDE 0105; IEC 364). Improper
behaviour may result in serious
injury and damage to prop-
erty
. The applicable
national
,
local
and
works regulations
and requirements
must be complied with.
Geared motors are
components
for installation in machinery
in terms of the Machinery Directive 89/392/EEC.
Commissioning
must not take place until it has been verified
that the end product conforms with this guideline (please note
EN 60204-1).
2
Intended use and guarantee
These geared motors are intended for commercial installa-
tions. They comply with the harmonized standards of the
EN 60034 (VDE 0530)
series. Utilization in areas subject to
explosion hazards is not permitted.
The geared motors are rated for ambient temperatures of
–10 °C to +40 °C
and site altitudes
≤
1000 m
above sea level.
Any contradictory information on the rating plate
must
be ob-
served.
The conditions on site must correspond to
all
rating
plate specifications.
Wearing parts are not subject to the guarantee. Guarantee
claims must be made by quoting the order number to Siemens
immediately on detecting the defect.
The guarantee is rendered invalid, for example, in the event of:
• inappropriate
use,
•
faulty devices or equipment connected or attached to
the product which are not part of our scope of sup-
plies and services,
•
use of non-genuine spare parts and accessories,
•
refurbishment or modification of the product unless
approved in writing by Siemens.
All technical information, data and instructions for operation
contained in these notes on safety were up-to-date on going to
print and are compiled on the basis of our experience and to
the best of our knowledge.
We reserve the right to incorporate technical modifications
within the scope of further development of the geared motors
which are the subject of this document. Therefore, no claims
can be derived from the information, illustrations and descrip-
tions contained in these notes on safety.
3 Transport
and
storage
The drive is supplied as an assembled unit. Additional equip-
ment may be supplied in separate packaging.
In the case of any damage determined after delivery, the
transport company must be notified immediately; if necessary,
the plant is not to be put into commission. During transporta-
tion,
all
lifting eyes available in the geared motor are to be u-
sed and be done up tight when fitted! They are designed and
built for the
weight of the geared motor only
. Do not add any
additional loads. If necessary, use suitable, adequately dimen-
sioned transporting means (for example, rope guides).
Remove
existing
shipping braces
before commissioning; and
re-use for subsequent transport.
Geared motors must be stored as follows:
•
in dry places with low temperature fluctuations
•
in their service position
•
protected against dust and moisture
•
on a wooden support
•
free from vibration (no impacts)
Drives must not be stacked on top of each other.
Unless otherwise agreed in the purchase contract, standard
conservation is guaranteed for a period of 6 months. The gua-
rantee period begins on the day the unit is delivered.
Contact Siemens if geared motors are to be stored for periods
longer than 6 months.
Before commissioning, measure the insulation resistance. If
values <1kOhm per volt of rated voltage are measured, the
windings must be dried out.
4 Installation
Before installing the motor, check whether it has suffered any
damage in transit or while in storage, such as deformation,
breakage, corrosion or leaks.
A canopy is recommended for designs with the air inlet from
the top; and with the air inlet from the bottom, a cover must be
provided by the customer
to prevent any foreign bodies from
falling into the fan.
The site at which the geared motor is installed must be de-
signed in such a way that
•
air may circulate to allow heat to be exchanged and
heated air is not directly sucked in again,
•
no residue from operating processes can accumu-
late on the geared motor, fall between the drive ele-
ments or damage the sealing ring,
•
the oil inlet and outlet and rating plate are accessi-
ble.
The oil quantity depends on the mounting position. Before in-
stalling the geared motor, check whether it will be operated in
the mounting position specified on the rating plate (
see Fig. 1
to 5
).
Gearbox size W1 – W4 (2KG131 to 2KG134):
These gearbox sizes are not vented.
If the gearbox has to
be vented (non-standard design), the oil inlet screw at the
highest point of the gearbox must be replaced by the breather
valve (tightening torque 5 Nm).
Gearbox size W5 – W0 (2KG135 to 2KG130):
A breather valve is supplied as standard. This must be fitted at
the highest point of the gearbox in place of the oil inlet screw
(tightening torque 15 Nm).
The support or flange surface must be designed in such a way
that no forces are transmitted to the gearbox housing as a re-
sult of mounting distortions. The following conditions must be
met by the bolted connections to the supporting structure to
ensure the correct functioning of the unit:
Tightening torques for
foot
connection
(mounting codes B3, B6, B7, B8, V5, V6)
Gearbox
Bolt
Washer Tightening
optional Bolt Tightening
size
torque
torque
DIN 912 or 931 DIN 125
Locking
grade 8.8
Nm
bolt Nm
W1
4xM8
A 8,4
25
4xM8 35
W2
4xM10
A 10,5
51
4xM10 75
W3
4xM10
A 10,5
51
4xM10 75
W4
4xM12
A 13
87
4xM12 115
W5
4xM12
A 13
87
4xM12 115
W6
4xM16
A 17
215
4xM16 300
W7
4xM16
A 17
215
4xM16 300
W8
4xM20
A 21
430
4xM20 720
W9
4xM24
A 25
670
-
-
W0
4xM30
A 31
1500
-
-