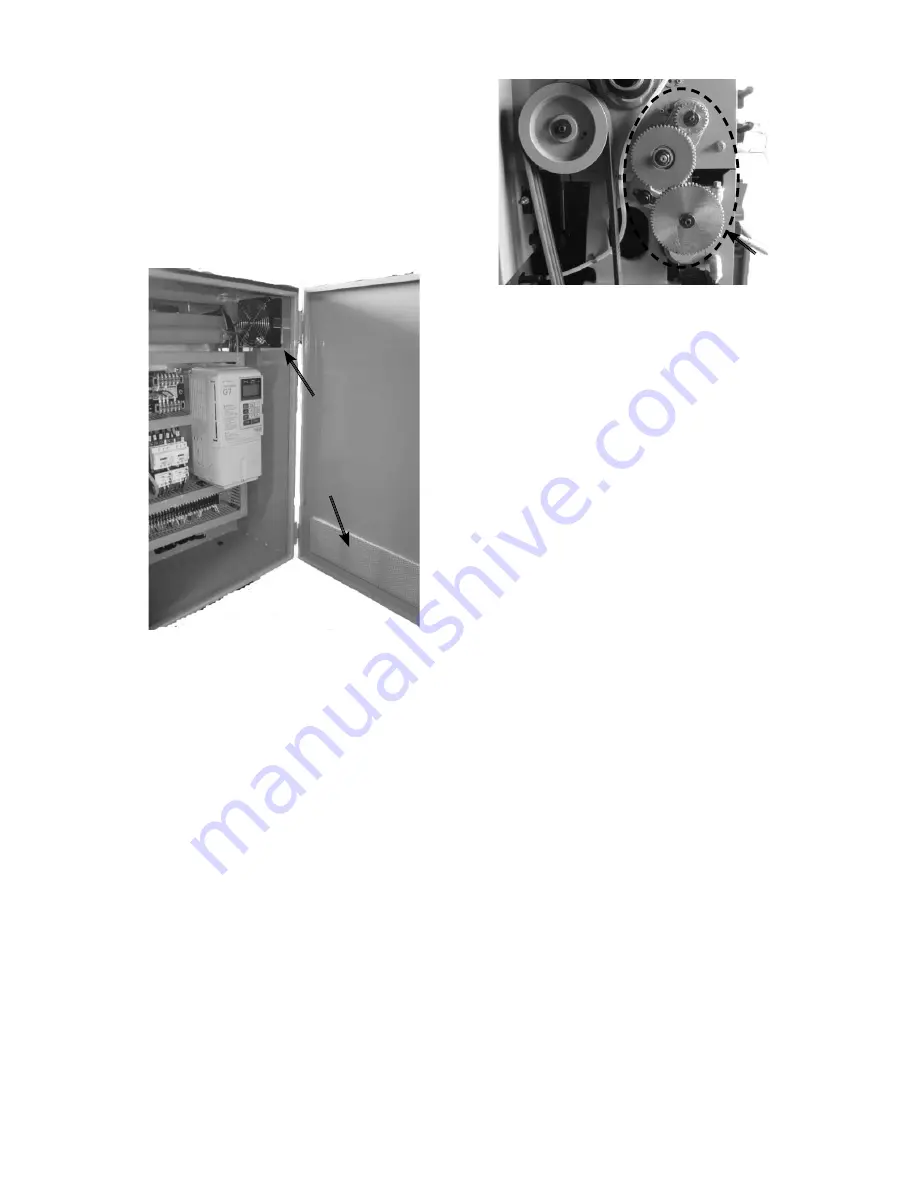
-30-
Cleaning Electrical Box Filter
The door of the electrical box contains an air
fi
lter (
Figure 80 ) to prevent dust from entering the box as
the cooling fan pulls in cool air to reduce heat.
The air
fi
lter should be cleaned on a monthly basis to
ensure proper air circulation in the electrical box. A
clogged air
fi
lter will not allow the cooling fan to do its
job, which could result in a decreased lifespan of the
electrical components.
Handling & Care
Make sure to clean and lubricate any gears you install
or swap. Unless you are very careful during handling
and storage, the coating of grease on the gears will
easily pickup dirt or debris, which can then spread to
the other gears and increase the rate of wear.
Make sure to the cover remains installed whenever
possible to keep the gears free of dust or debris from
the outside environment.
Lubricating
1. Disconnect Lathe from POWER !
2. Remove the headstock side cover and all the end
gears shown in Figure 81.
3. Clean the end gears thoroughly in mineral oil to
remove all the old grease. Use a small brush if
necessary to clean between the teeth.
4. Clean the shafts from which the end gears were
removed, and wipe up any old grease splatters
in the vicinity and on the inside of the headstock
cover.
5. With clean hands, apply a thin layer of grease on
both sides of the gears. Make sure to get grease
between the gear teeth, but not so much that it
fi
lls the voids between the teeth.
6. Install the end gears and mesh them together
with an approximate backlash of 0.127mm. Once
the gears are meshed together, apply a small dab
of grease in the crux of where the gears mesh
together—this grease will spread around when
the gears start moving and re-coat any areas
scraped off during installation.
Annual Maintenance
Once a year, remove all the end gears, clean them
thoroughly, and apply a new coating of grease. Even
if the headstock side cover has been kept in place
throughout the year, it is still possible for dust from the
V-belts to build-up in the grease, and the grease may
also start to break down with extended or heavy use.
Figure 80. Electrical box cooling fan and
fi
lter.
Cooling Fan
Filter
End Gears
Figure 81. Location of end gears that require
grease.
To clean the
fi
lter :
1. Disconnect Lathe from POWER !
2. Put on a dust mask or respirator to reduce your
risk of inhaling
fi
ne dust.
3. Open the electrical box door, and remove
electrical box air
fi
lter.
4. Use compressed air to blow dust out of the
fi
lter.
Make sure to blow the dust from the clean side (
the side facing inward ) of the
fi
lter so you do not
drive dust farther into the
fi
lter.
5. Re-install
fi
lter and close electrical box door.
End Gearing
The end gears, shown in Figure 81, should always
have a thin coat of heavy grease to reduce the
minimize/prevent corrosion, noise, and wear. Care
must be taken to avoid over-greasing because excess
grease may be
fl
ung onto the V-belts, which will
reduce optimal power transmission from the motor.