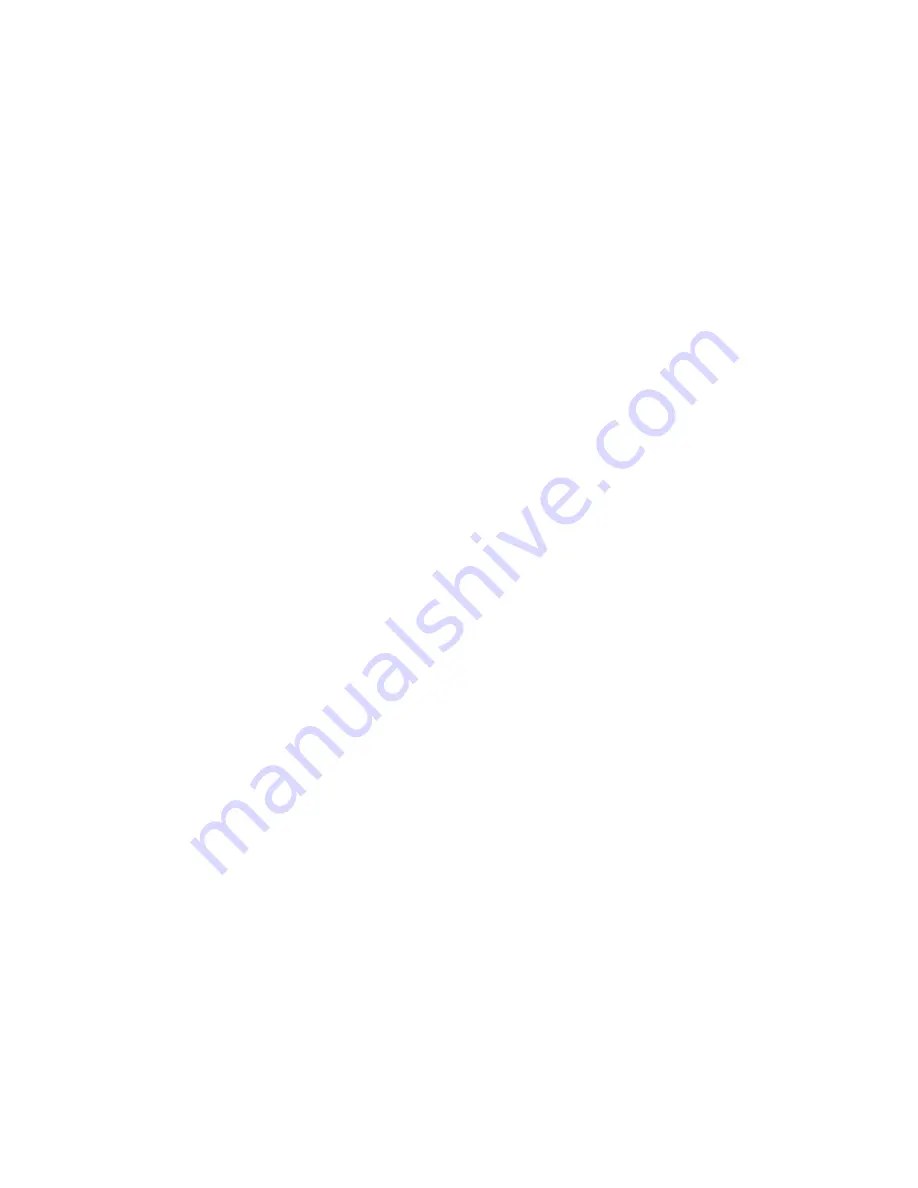
-26-
Schedule
Each operator of this machine is responsible for
ensuring proper care of the equipment. We strongly
recommend all operators make a habit of following
the daily maintenance procedures.
For optimum performance from this machine, this
maintenance schedule must be strictly followed.
Ongoing
To maintain a low risk of injury and proper machine
operation, if you ever observe any of the items below,
shut the machine down immediately and
fi
x the
problem before continuing operations :
•
Loose mounting bolts or fasteners.
•
Worn, frayed, cracked, or damaged wires.
• Guards
removed.
•
Limit/kill switches bypassed.
• Emergency stop button not working correctly or
not requiring you to reset it before starting the
machine again.
•
A reduction in braking speed or ef
fi
ciency.
•
Headstock oil not
fl
owing against sight glass.
• Cutting
fl
uid not
fl
owing out.
•
Any other unsafe condition.
Daily, Before Operations
•
Check / add gearbox oil.
•
Check / add apron oil.
• Check
cutting
fl
uid level.
•
Lubricate the ways.
•
Put oil in the ball oilers.
•
Check / add leadscrew & feedrod bearing oil.
•
Clean / lubricate the leadscrew.
•
Turn spindle speed dial all the way down.
•
Move the power feed lever on the apron to neutral
(to prevent crashes upon startup).
•
Ensure carriage lock bolt is loose.
Daily, During Operations
• Verify headstock oil
fl
ows when power is turned
ON.
•
Verify electrical box cooling fan is operating.
• Verify headstock oil temperature is under 138°C
(170° F).
Daily, After Operations
• Vacuum/clean all chips and swarf from bed,
slides, and chip drawer.
• Wipe down all unpainted or machined surfaces
with an oiled rag.
• Depress emergency stop button and shut OFF
the main power switch (to prevent accidental
startup).
Monthly
• Drain and clean the cutting
fl
uid tank, then add
new cutting
fl
uid.
• Remove electrical box air
fi
lter and clean with
compressed air or a vacuum.
Annually ( or Semi-Annually with Hard Use )
•
Drain and clean the headstock oil reservoir, then
add new oil.
•
Change the apron oil.
•
Change the gearbox oil.
Cleaning
Regular cleaning is one of the most important steps
in taking good care of this lathe. Each operator is
responsible for cleaning the machine immediately
after using it or at the end of the day. We recommend
that the cleaning routine be planned into the work
fl
ow
schedule, so that adequate time is set aside to do the
job right.
Typically, the easiest way to clean swarf from the
bed ways and chip drawer is to use a wet/dry shop
vacuum that is dedicated for this purpose only. The
small chips leftover after vacuuming can be wiped up
with a slightly oiled rag. Avoid using compressed air
to blow off chips, as it may drive them deeper into
moving surfaces and could cause sharp chips to
fl
y
into your face or hands.
All visible swarf should be removed from the lathe
during cleaning. Remember, personal neatness gives
you personality.
Lubrication
Headstock
This headstock lubrication system is the most
important lubrication system on the machine. It
consists of an electric oil pump, a low oil pressure
kill switch, a holding tank, oil lines, and a distribution
manifold. The headstock has a series of oil lines
that direct oil to key locations, such as the spindle
bearings and headstock gearing, to ensure that they
always remain well lubricated.
The oil pump automatically turns ON and begins
oiling the headstock components when the main
power switch is turned ON and the emergency stop
button is reset. The oil is pumped before the spindle
is started to protect the spindle bearings against
potential damage from dry starts.
Checking & Adding Oil
The sight glass on the side of the headstock oil tank,
shown in Figure 68, has a dual function of showing
the oil level and temperature. When checking the oil
level, read the sight glass as you would a dipstick on
a car—the bottom line represents the minimum and
the top line represents the maximum.
Section 4 : Maintenance