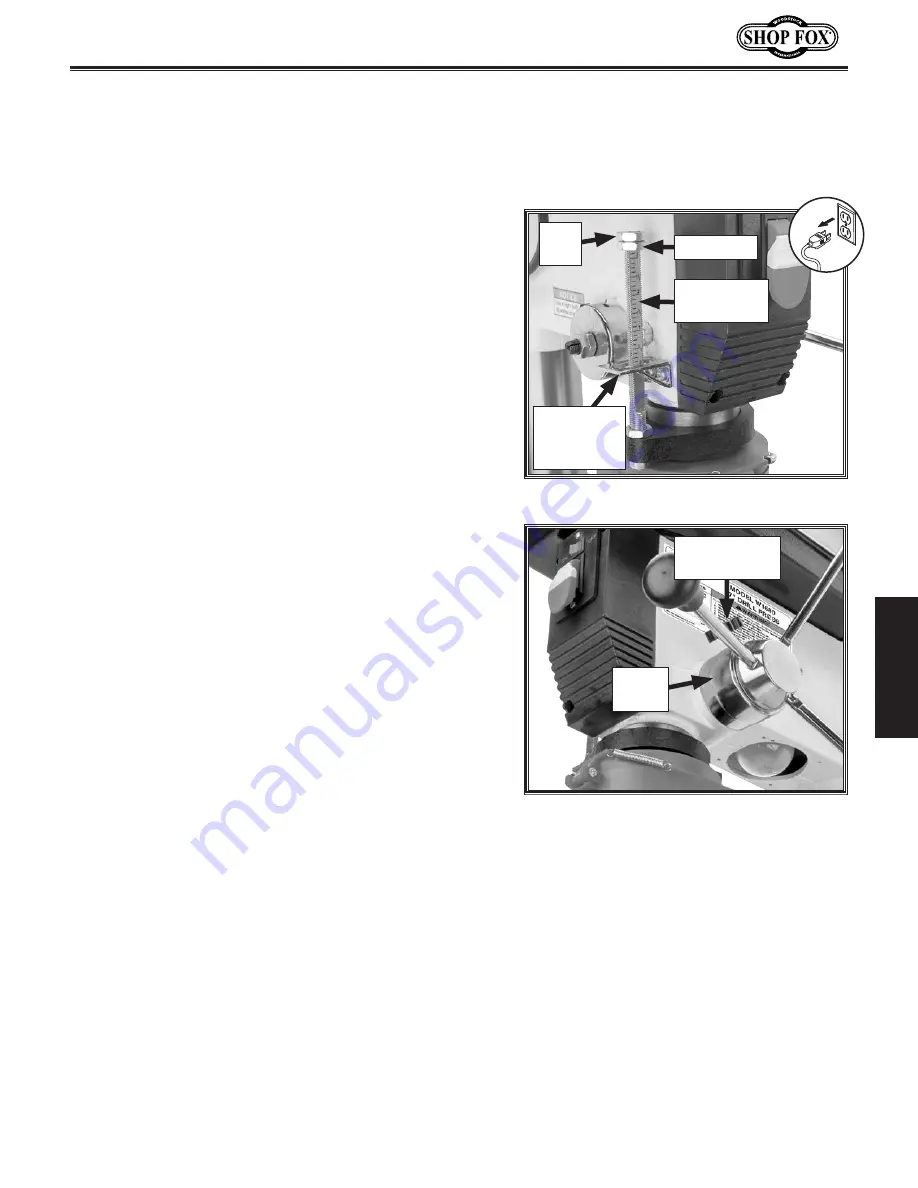
-33-
Model W1680 (For Machines Mfd. Since 06/22)
O
PE
R
ATIO
NS
Adjusting.Depth.Stop
The Model W1680 has a depth stop that allows you to drill
repeat non-through holes to the same depth every time.
The scale and indicator shows the depth in inches.
Figure.35..
Depth stop components.
Depth Nut
Depth Stop
Stud
Depth Stop
Indicator
Bracket
Jam
Nut
To.adjust.depth.stop,.do.these.steps:
1.
DISCONNECT MACHINE FROM POWER!
Items.Needed.
Qty
Open-End Wrenches 18mm ....................................2
Scrap Stock .......................................... As Needed
2.
Loosen depth collar lock knob (see
Figure
36
).
3.
Use spindle handles to lower drill bit to desired
depth.
4.
Turn depth collar all the way clockwise (see
Figure
36
), then tighten depth collar lock knob to keep
spindle in lowered position.
5.
Thread depth nut down against indicator bracket.
6.
Adjust jam nut down against depth nut to secure
position.
7.
Loosen depth collar lock knob to release spindle.
8.
Drill hole in scrap stock to check adjustment before
drilling into workpiece.
Figure.36..
Location of depth collar lock
knob.
Depth Collar
Lock Knob
The depth stop consists of a stud attached to the quill
with a depth nut that can be lowered or raised against a
stop bracket indicator to control drilling depth.
Figure
35
shows the various components of the depth stop.
Depth
Collar