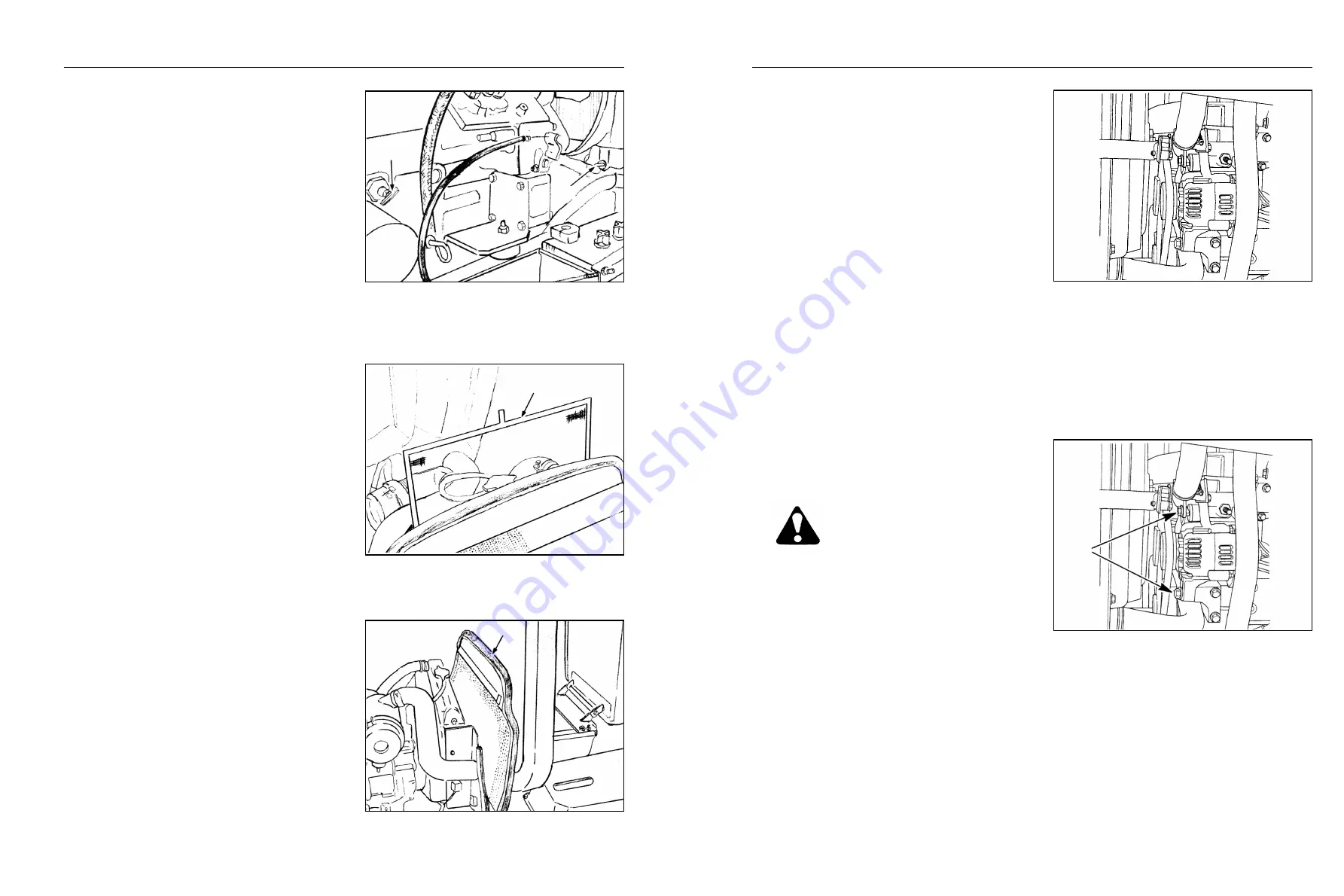
3-15
Draining and Flushing the Cooling System
NOTE: Drain and flush the radiator and
engine block every 12 months. Refill with a
50/50 mixture of permanent antifreeze and
clear water.
To drain the cooling system:
1. Use a suitable receptacle to catch the
used coolant. Remove the radiator cap
and open the radiator drain valve
B
, and
engine block drain valve
A
.
2. After the coolant has drained, place a water
hose in the radiator filler neck and run water
through the system. When water is flowing
from the block drain valve, start the engine.
When the water flowing from the drain valve,
is free of discoloration and sediment, stop the
engine and remove the hose. Allow all water
to drain from the system through the drain
valves.
3. Close the drain valve and slowly refill the
system with a 50/50 solution of permanent
antifreeze and clear water. Fill until the
coolant level is approximately 1.2 cm-2.5
cm (1/2"-1") below the bottom of the filler
neck. Do not fill beyond this level.
4. Clean the radiator cap and cap seal and
install the cap.
5. Fill the coolant recovery reservoir bringing the
fluid level up until it is between the full and
low marks on the reservoir.
6. Pull out the front screen
D
upward and
remove chaff, dust, or other foreign
substances. The foreign substances can be
dropped onto the ground through the rubber
at the lower part.
7. Pull out the radiator screen
C
and clean it.
8. Run the engine until normal operating
temperature is reached, then stop the engine.
Recheck the coolant level when the engine is
cold and add additional coolant as
necessary.
IMPORTANT: Never run the engine when the
cooling system is empty. Do not add cold water
or cold antifreeze solution if the engine is hot.
3-14
LUBRICATION AND MAINTENANCE
Fan Belt
NOTE: Check the condition of the fan belt
after every 50 hours of operation. Check fan
belt tension after every 200 hours of
operation.
A belt-driven fan located at the front of the engine
draws air through the fins of the radiator to lower
the temperature of the radiator coolant.
When 9-11 kg (20-25 lbs.) of thumb pressure is
applied midway between the belt pulleys, a
correctly tightened belt will deflect 10 mm-15 mm
(7/16"-9/16").
If the fan belt is slipping, fan efficiency is lowered,
resulting in the engine running too hot. If the belt
is too tight, the life of the alternator bearing will be
shortened. If the fan belt shows signs of cracking
or fraying, install a new one.
To adjust fan belt tension:
1. Loosen the alternator mounting bolts
A
.
WARNING: NEVER ATTEMPT TO
LOOSEN OR TIGHTEN MOUNTING
BOLTS WITH THE ENGINE RUNNING.
2. Pry the alternator away from the engine and
tighten the mounting bolts.
3. Recheck belt deflection.
FAN BEST
A
ALTERNATOR BELT TENSION ADJUSTMENT
1. Alternator Mounting Bolts
LUBRICATION AND MAINTENANCE
A
B
COOLING SYSTEM
1. Engine Block Drain Valve
2. Radiator Drain Valve
C
3. Radiator Screen
D
4. Front Screen