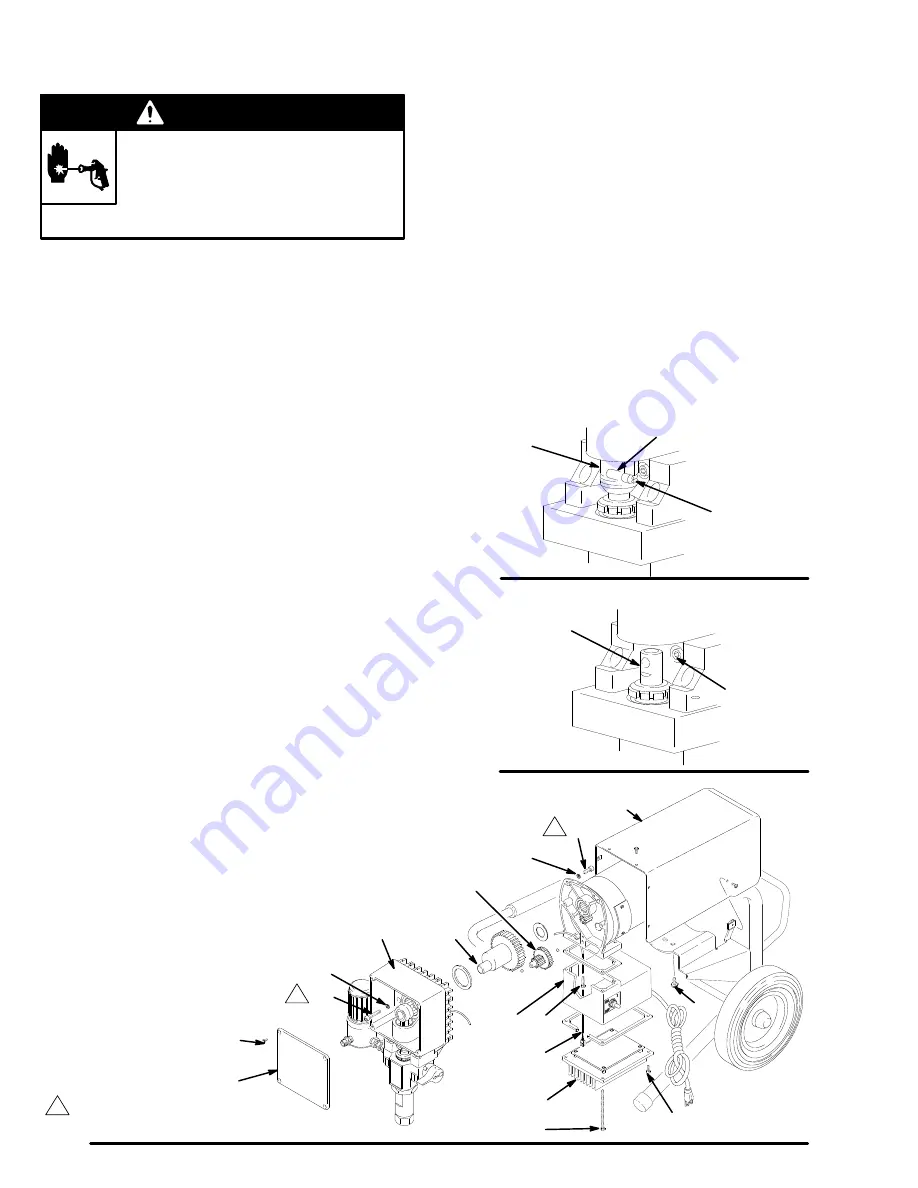
Motor
WARNING
INJECTION HAZARD
To reduce the risk of serious injury,
whenever you are instructed to relieve
pressure, follow the Pressure Relief
Procedure on page 8.
NOTE: See Fig. 26 except where noted.
1.
Try to stop the pump with the piston rod (107) in its
lowest position. To lower the piston rod manually,
remove the shroud (4) and rotate the motor fan
blades. Use a screwdriver to push the retaining
spring (18) up and push out the pin (17). See Fig.
24.
2.
Relieve pressure.
3.
Remove the motor shield (4).
4.
Lift the connecting rod. Remove the screws
(56,75) and lower the control card (47). Disconnect
the motor wires and the pressure transducer wire
(A) from the motor control board. Remove the con-
trol card (47), screws (71), and junction box (59).
Refer to Fig. 26.
5.
Remove the drive housing cover (13).
6.
Turn the displacement pump rod (107) so the pin
hole aligns with the bottom drive housing screw
(19). See Fig. 25. Remove the three drive housing
screws and lockwashers (19,6). See Fig. 25 and
26
.
7.
Remove the two motor screws and lockwashers
(5,6).
8.
Tap the lower rear of the drive housing (11) with a
plastic mallet to loosen the motor. Pull the drive
housing straight off the motor while guiding the
harness (A) from the motor. Do not allow the gear
(16) to fall. Read the CAUTION on page 28.
9.
Remove the two screws (46) and lift the motor off
the cart (1).
10. Align the new motor with the cart and reinstall the
screws (46).
11. Assemble the drive housing to the motor. Follow
steps 9 to 15 on page 28. Install the junction box.
12. Connect the wires to the control card. Refer to Fig.
13. Install the control card.
13. Connect the piston rod (107) to the drive housing;
see page 22, Installing the Pump, Step 2 and the
WARNING following it.
14. Install the shroud (4) and drive housing cover (13).
17
18
15
Fig. 24
01068
107
19,6
Fig. 25
01074
03201A
Fig. 26
1
19
6
13
34
59
56
12
16
11
4
5
6
46
Torque to 80 in–lb (9 N.m)
A
75
47
71
1
1