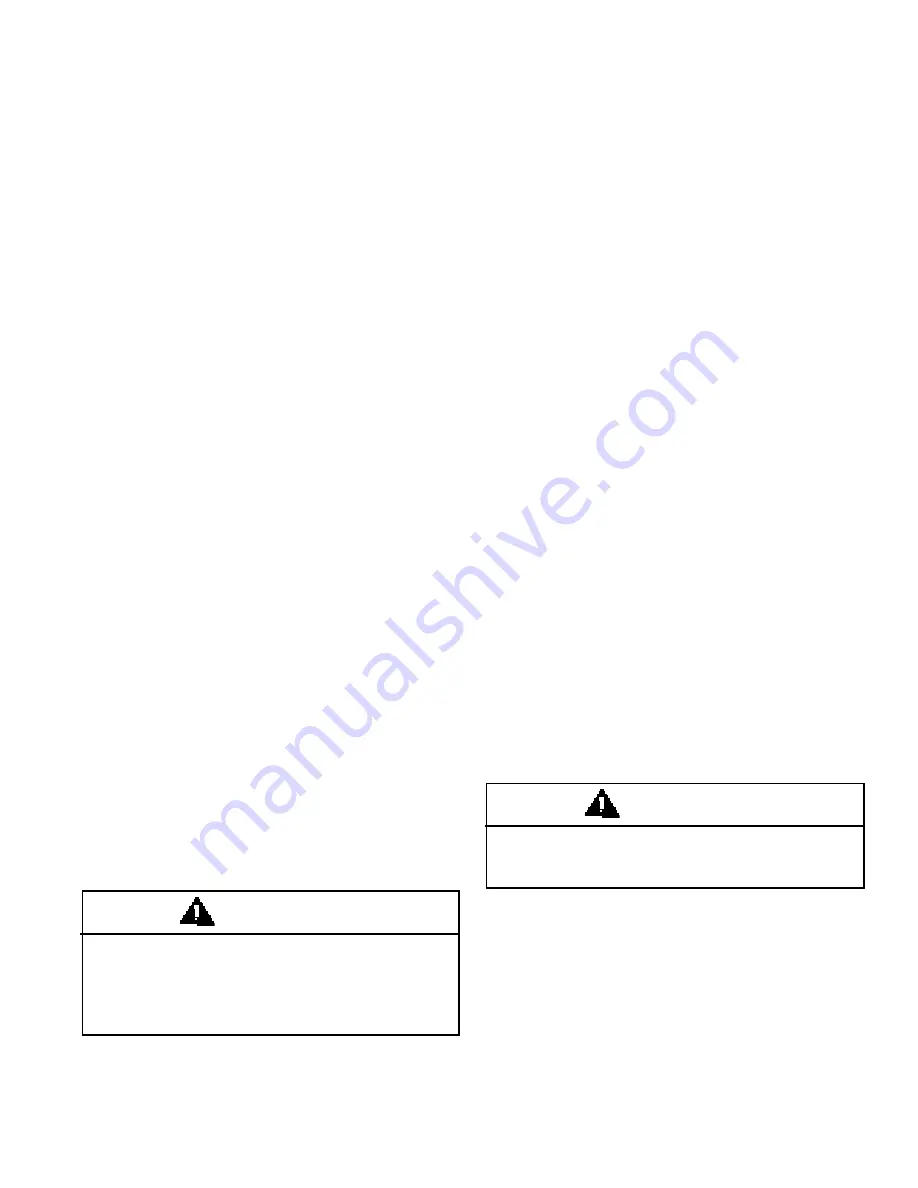
Page 11
MAINTENANCE
GENERAL: Maintenance services required on traverses
are, for the most part, simple periodic inspections and
adjustments. Procedures for lubrication, routine
adjustments and replacement of parts, if required, are
described in the following paragraphs.
LUBRICATION: Motor bearings are lubricated for the life of
the bearing and require no additional lubrication.
Axle bearings require regular lubrication. Lubricate through
grease fittings on trucks with a N.L.G.I. #1 grease.
The gearhead unit attached to the motor requires gear
case oil having a viscosity at 210½F of 125-150 ssu,
viscosity index of 90 and a pour point of 25½F (AGMA #7
Compound) at an ambient temperature of 50½ to 125½F.
For ambient temperatures outside this range, refer to the
Manufacturer for recommendations.
General oiling should be performed every three months to
prevent rusting and provide limited lubrication for points
not having lubrication fittings nor considered normal wear
points. Pins, levers, rods, hinges and other linkages and
moving parts, where rusting could occur and interfere
with normal operation, should be oiled with a few drops of
oil. (Examples include, collector pins and linkage, limit
switch linkage, cable carriers, etc. Also see instructions
furnished with hoist.)
The frequency of oil changes in the gearhead unit and
axle bearing lubrication is dependent on crane usage. The
user should establish a lubrication interval based on
individual conditions of usage and environment (including
airborne dirt, chemical dust, moisture, etc.), but this interval
should never exceed six months. Also, drain and refill
gearhead unit after first 100 hours of operation.
For hoist lubrication instructions refer to Hoist Manu-
facturer’s Service Manual.
WHEEL REMOVAL
(Refer to parts illustration, Figure 2.)
To remove wheels, follow steps 1 through 7 listed below:
1.
Remove any load from hook.
Make sure that traverse is adequately supported
so that it cannot drop when wheel is removed.
Also lock main runway disconnect switch in
open (power off) position when working on
wheels adjacent to runway conductors.
2.
Remove load from wheel axle. This can be
accomplished by jacking a small distance, just enough to
clear the wheel flanges.
3.
Wheel (Ref. No. 3) is held in position by retainers
(Ref. No. 5), locked in a groove in the axle. Remove bolts
and lockwashers (Ref. No. 6 and Ref. No. 7).
4.
Remove retainers (Ref. No. 5) by sliding them away
from the center of the axle and out of their grooves.
5.
Wheel is now free. Remove by sliding horizontally off
axle, maintaining a secure hold so that wheel does not
fall.
6.
Remove key (Ref. No. 4).
7.
Replace wheels in reverse procedure of disassembly.
Wheel at motor may be removed by using the above
procedure after the gearmotor has been removed.
AXLE REMOVAL
(Refer to parts illustration, Figure 2.)
To remove axle, follow steps 1 through 5 listed below:
1.
Remove both wheels on truck as described above.
2.
Remove spacers (Ref. No. 10).
3.
One side of truck has a retaining ring (Ref. No. 9),
securing the axle bearing (Ref. No. 8). The axle (Ref. No.
1) may be removed by pushing axle toward opposite side
of truck. Maintain a secure hold on the axle so that it does
not fall.
4.
If required, retaining ring may also be removed allowing
removal of both bearings.
5.
Replace axle in reverse procedure of disassembly.
Note that bearings are equipped with a single grease
seal. This seal must be toward the outside of the traverse.
It is recommended that bearings be replaced whenever
replacing wheels or axles.
The axle at the motor may be removed by using the
above procedure after the gearmotor has been removed.
GEARMOTOR REMOVAL
(Refer to parts illustration, Figure 1.)
Main runway disconnect switch should be locked
open (power off) before working on gearmotor.
To remove gearmotor:
1.
Disconnect wiring and conduit at conduit box on motor.
2.
Remove the two bolts and lockwashers holding the
top of the gearhead unit to the motor mounting angle (Ref.
No. 8) on the driver truck.
3.
Slide gearmotor off axle extension taking care not to
drop it.
4.
Remove key (Ref. No. 13).
5.
Reassemble in reverse.
ELECTRICAL
WARNING
WARNING
Содержание Series 700
Страница 2: ...Page 2 Figure A 12484...
Страница 4: ...Page 4 Figure C Electrical Enclosure and Resistor Mounting Arrangement...
Страница 5: ...Page 5 Figure D Ballast Resistor Mounting Arrangement...
Страница 16: ...Page 16 Figure 3 Motor and Gear Box...