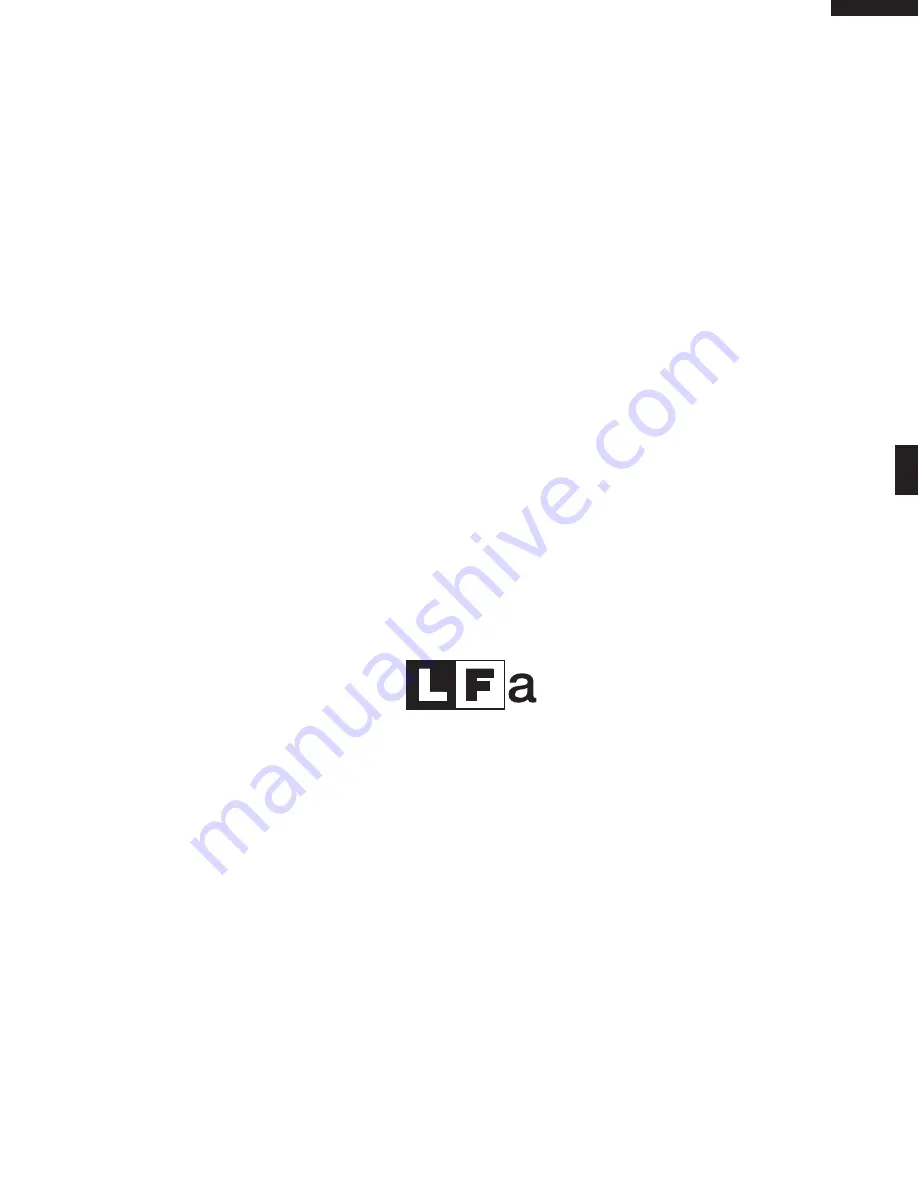
R-8000G
29
(on PWB) of the touch control panel with a jumper, which
activates an operational state that is equivalent to the oven
door being closed. As for the sensor-related controls of the
touch control panel, checking them is possible if dummy
resistor(s) with resistance equal to that of the controls are
used.
(2) Servicing the touch control panel with power supply from
an external power source:
Disconnect the touch control panel completely from the
oven proper, and short both ends of the door sensing switch
(on PWB) of the touch control panel, which activates an
operational state that is equivalent to the oven door being
closed. Connect an external power source to the power
input terminal of the touch control panel, then it is possible
to check and repair the controls of the touch control panel
it is also possible to check the sensor-related controls of the
touch control panel by using the dummy resistor(s).
3. Servicing Tools
Tools required to service the touch control panel assembly.
1) Soldering iron: 60W
(It is recommended to use a soldering iron with a grounding
terminal.)
2) Oscilloscope: Single beam, frequency range: DC-10MHz
type or more advanced model.
3) Others: Hand tools
4. Other Precautions
1) Before turning on the power source of the control unit,
remove the aluminium foil applied for preventing static
electricity.
2) Connect the connectors of the key unit to the control unit
being sure that the lead wires are not twisted.
3) After aluminium foil is removed, be careful that abnormal
voltage due to static electricity etc. is not applied to the input
or output terminals.
4) Attach connectors, electrolytic capacitors, etc. to PWB,
making sure that all connections are tight.
5) Be sure to use specified components where high precision
is required.
1. Employing lead-free solder
“Main PWB” of this model employs lead-free solder. The LF symbol indicates lead-free solder, and is attached on the PWBs and
service manuals. The alphabetical character following LF shows the type of lead-free solder.
Example:
Indicates lead-free solder of tin, silver and copper.
2. Using lead-free wire solder
When fixing the PWB soldered with the lead-free solder, apply lead-free wire solder. Repairing with conventional lead wire solder
may cause damage or accident due to cracks.
As the melting point of lead-free solder (Sn-Ag-Cu) is higher than the lead wire solder by 40˚C, we recommend you to use a dedicated
soldering bit.
3. Soldering
As the melting point of lead-free solder (Sn-Ag-Cu) is about 220˚C which is higher than the conventional lead solder by 40˚C, and
as it has poor solder wettability, you may be apt to keep the soldering bit in contact with the PWB for extended period of time. However,
since the land may be peeled off or the maximum heat-resistance temperature of parts may be exceeded, remove the bit from the
PWB as soon as you confirm the steady soldering condition.
Lead-free solder contains more tin, and the end of the soldering bit may be easily corroded. Make sure to turn on and off the power
of the bit as required.
If a different type of solder stays on the tip of the soldering bit, it is alloyed with lead-free solder. Clean the bit after every use of it.
When the tip of the soldering bit is blackened during use, file it with steel wool or fine sandpaper.
PRECAUTIONS FOR USING LEAD-FREE SOLDER
Sn-Ag-Cu