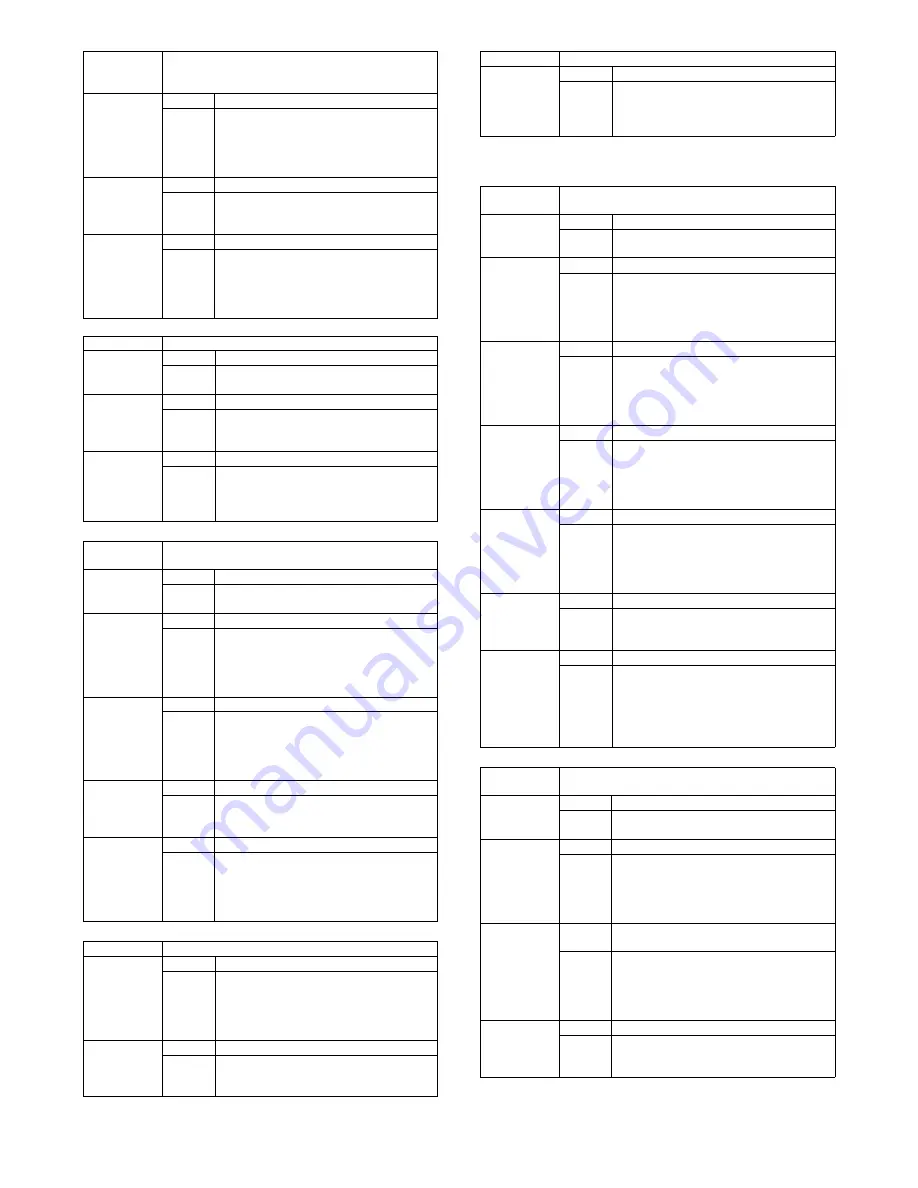
MX-FN10 SELF DIAG MESSAGE AND TROUBLE CODE 9 – 3
5. Load tray
Case4
Cause
Rear alignment plate HP sensor
Check &
Remedy
Measure the voltage at TP32 on the finisher
control PWB to confirm that it is 1V or less
when transmitting, and 3.3V
5% when
interrupted. If the voltage is outside the range,
replace the sensor.
Case5
Cause
Electric cable, connector trouble
Check &
Remedy
Check conduction between connector
terminals. If there is no conduction, replace
the electric cable.
Case6
Cause
Finisher control PWB trouble
Check &
Remedy
If the motor does not operate properly in the
motor single operation mode, replace the
finisher control PWB. Also in the sensor
check, if it is normal but the trouble still
remains, replace the finisher control PWB.
Phenomenon
Poor alignment of paper on the process tray
Case1
Cause
Process bundle holding solenoid trouble
Check &
Remedy
Check conduction of the coil. If there is no
conduction, replace.
Case2
Cause
Electric cable, connector trouble
Check &
Remedy
Check conduction between connector
terminals. If there is no conduction, replace
the electric cable.
Case3
Cause
Finisher control PWB trouble
Check &
Remedy
If the solenoid does not operate properly in
the single operation mode, or if the trouble
remains even tough the solenoid operates
properly, replace the finisher control PWB.
Phenomenon
Bundle exit is not performed properly. (The gripper
extension motor does not operate properly.)
Case1
Cause
Griper extension motor trouble
Check &
Remedy
Check conduction of the coil. If there is no
conduction, replace.
Case2
Cause
Gripper extension HP sensor trouble
Check &
Remedy
Measure the voltage at TP33 on the finisher
control PWB to confirm that it is 1V or less
when transmitting, and 3.3V
5% when
interrupted. If the voltage is outside the range,
replace the sensor.
Case3
Cause
Gripper exit sensor trouble
Check &
Remedy
Measure the voltage at TP27 on the finisher
control PWB to confirm that it is 1V or less
when transmitting, and 3.3V
5% when
interrupted. If the voltage is outside the range,
replace the sensor.
Case4
Cause
Electric cable, connector trouble
Check &
Remedy
Check conduction between connector
terminals. If there is no conduction, replace
the electric cable.
Case5
Cause
Finisher control PWB trouble
Check &
Remedy
If the motor does not operate properly in the
motor single operation mode, replace the
finisher control PWB. Also in the sensor
check, if it is normal but the trouble still
remains, replace the finisher control PWB.
Phenomenon
Paper empty in the process tray cannot be detected.
Case1
Cause
Paper detection 2 sensor trouble
Check &
Remedy
Measure the voltage at TP26 on the finisher
control PWB to confirm that it is 1V or less
when transmitting, and 3.3V
5% when
interrupted. If the voltage is outside the range,
replace the sensor.
Case2
Cause
Electric cable, connector trouble
Check &
Remedy
Check conduction between connector
terminals. If there is no conduction, replace
the electric cable.
Phenomenon
Poor alignment of paper on the process tray
(The alignment plate motor does not operate
properly.)
Case3
Cause
Finisher control PWB trouble
Check &
Remedy
When the sensor is turned ON/OFF, if the
phenomenon still remains though the sensor
level is changed, replace the finisher control
PWB.
Phenomenon
Paper surface detection is not performed properly.
(The load tray lift motor does not operate properly.)
Case1
Cause
Load tray lift motor trouble
Check &
Remedy
Check conduction of the coil. If there is no
conduction, replace.
Case2
Cause
Load tray clock sensor trouble
Check &
Remedy
Measure the voltage at TP23 on the finisher
control PWB to confirm that it is 1V or less
when transmitting, and 3.3V
5% when
interrupted. If the voltage is outside the range,
replace the sensor.
Case3
Cause
Load tray upper limit sensor trouble
Check &
Remedy
Measure the voltage at TP35 on the finisher
control PWB to confirm that it is 1V or less
when transmitting, and 3.3V
5% when
interrupted. If the voltage is outside the range,
replace the sensor.
Case4
Cause
Load tray lower limit sensor trouble
Check &
Remedy
Measure the voltage at TP28 on the finisher
control PWB to confirm that it is 1V or less
when transmitting, and 3.3V
5% when
interrupted. If the voltage is outside the range,
replace the sensor.
Case5
Cause
Load tray intermediate sensor trouble
Check &
Remedy
Measure the voltage at TP29 on the finisher
control PWB to confirm that it is 1V or less
when transmitting, and 3.3V
5% when
interrupted. If the voltage is outside the range,
replace the sensor.
Case6
Cause
Electric cable, connector trouble
Check &
Remedy
Check conduction between connector
terminals. If there is no conduction, replace
the electric cable.
Case7
Cause
Finisher control PWB trouble
Check &
Remedy
If the motor does not operate properly in the
single operation mode, replace the finisher
control PWB. If the trouble remains even
tough the sensor operates properly in the
sensor check, replace the finisher control
PWB.
Phenomenon
Paper surface detection is not performed properly.
(The load tray is not proper.)
Case1
Cause
Paper exit paper holding solenoid trouble
Check &
Remedy
Check conduction of the coil. If there is no
conduction, replace.
Case2
Cause
Paper holding HP sensor trouble
Check &
Remedy
Measure the voltage at TP13 on the finisher
control PWB to confirm that it is 1V or less
when transmitting, and 3.3V
5% when
interrupted. If the voltage is outside the range,
replace the sensor.
Case3
Cause
Paper holding paper surface detection sensor
trouble
Check &
Remedy
Measure the voltage at TP71 on the finisher
control PWB to confirm that it is 1V or less
when transmitting, and 3.3V
5% when
interrupted. If the voltage is outside the range,
replace the sensor.
Case4
Cause
Electric cable, connector trouble
Check &
Remedy
Check conduction between connector
terminals. If there is no conduction, replace
the electric cable.
Phenomenon
Paper empty in the process tray cannot be detected.
Содержание MX-FN10
Страница 52: ...Memo ...
Страница 53: ...Memo ...