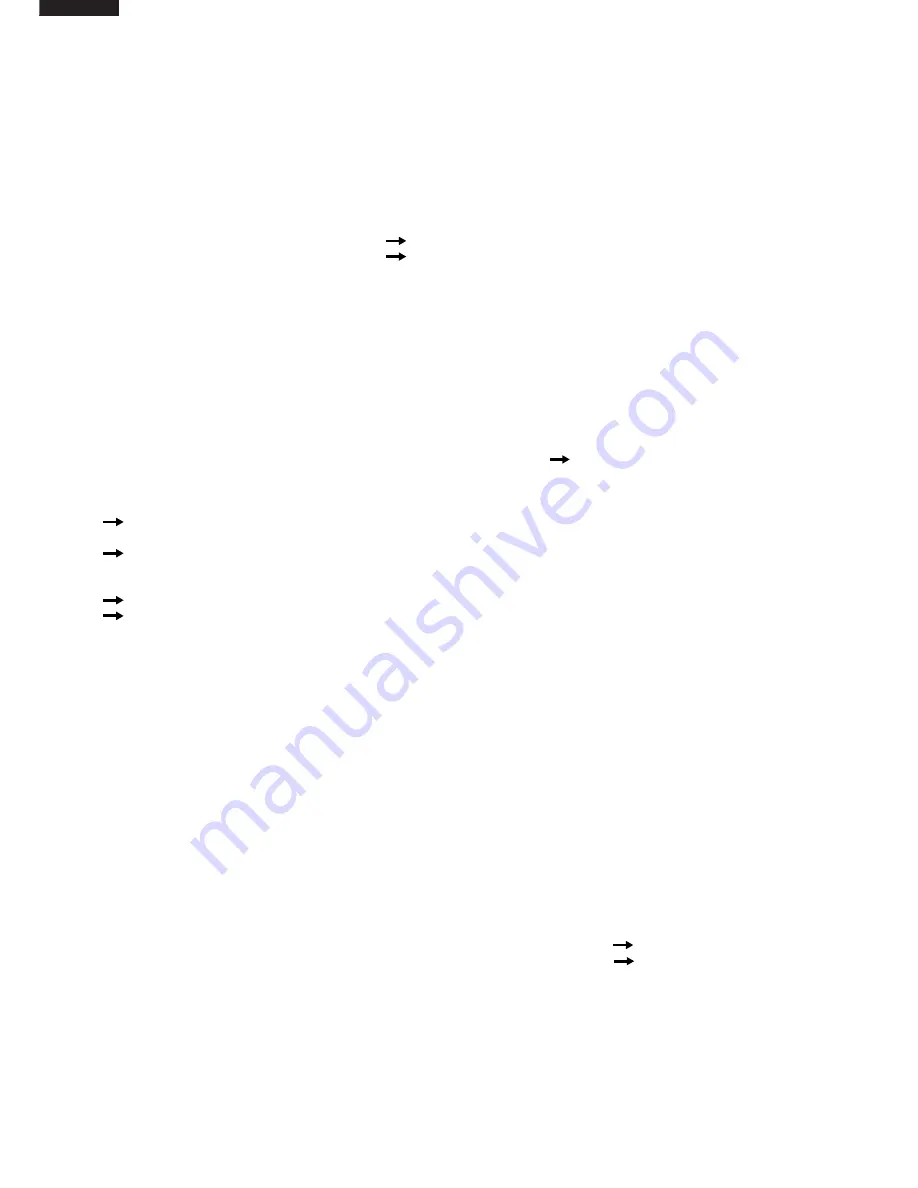
14
FU-40SE-TA
10) Odour sensor circuit
The pulse signal, which is the odour sensor drive signal, is output from the pin 37 of the microcomputer LSI1, and
the odour sensor is pulse-driven on the circuit of Q71, Q72, R73, R74, R76, and C73.
The sensor output signal is input into the pin 27 (A/D conversion terminal) of the microcomputer via R71 and C71.
<Principle of odour sensor>
The metal oxide semiconductor in this sensor reacts to ammonia, hydrogen, and alcohol, and changes the
resistance.
Weak odour : high resistance
high voltage
Strong odour : low resistance
low voltage
<Control>
After turning the power on, the value obtained 25 seconds after starting the first operation (for 30 seconds, the clean
sign of three colors for stabilization is lit one by one) is set as the reference value and the contamination is decided
in relative comparison between the values detected at an interval of approximately one second and the reference
value.
According to the contamination level, the clean sign is displayed, the fan motor is controlled, or the cluster mode is
switched.
Although the odour sensor is always activated during operation, it is deactivated while the operation is stopped to
cut down the standby power consumption.
However, if it comes to a complete stop, the readingcondition is altered in the next operation.
Therefore, it is activated for one minute in every ten minutes to keep the operating conditions.
Reference value: if the current level is cleaner than the reference value
the reference value is changed to the
current value immediately.
If the current level is dirtier than the reference value and the contamination level changes
(such as suddenly increased odour of cigarette smoke)
the reference value remains the same, but the clean sign is changed to indicate the air is contaminated
(orange or red, depending on the level).
the value in the clean condition (green) is adopted as a new reference value.
If the current level is dirtier than the reference value and the contamination level does not change
(Natural change only)
the reference value remains the same.
the value in the cleanest condition at eight-minute intervals is adopted as a new reference value.
11) Buzzer drive circuit
The " H " / " L " signals output from the pin 34 of the microcomputer LSI1 drive the digital transistor Q51 and sound
the buzzer BZ1.
12) Fan motor drive circuit
The fan motor has four input terminals and one output terminal.
Vm (CN-C7 pin)
: DC voltage input to be the source of motor rotation. (Vm = approx. DC310-340V)
Vm created by the power supply circuit is directly input and is constantly applied.
GND (CN-C5 pin) : Reference of the electric potential. All potentials such as Vm, Vcc, Vs, and PG indicate the
potential differences with GND.
Vcc (CN-C3 pin)
: DC voltage input terminal to be the power supply for the circuit that is built in the fan motor.
During operation, it turns on Q43 and Q44 by outputting the ÉÅHÉÇ signal from the pin 33 of
the microcomputer LSI1 of the fan motor, and supplies the potential almost equal to VL to the
Vcc terminal (Vcc = approx. DC15V).
Vs (CN-C2 pin)
: This input terminal controls the revolution speed of the fan motor (speed instruction signal).
After supplying Vcc during operation, the PWM (x/256ÉIs) pulse is output from the pin 6 of the
microcomputer LSI-1 and smoothed in the circuit consisting of C41, R41-43, Q41 and Q42.
Then it goes through R46 and C43 to supply the DC voltage to the Vs terminal.
(Vs = approx. DC0 É~ 6V)
When speeding up revolution: the pulse width X is widened
Vs voltage is increased
When slowing down revolution: the pulse width X is narrowed
Vs voltage is decreased
PG (CN-C1 pin)
: Fan motor revolution speed output terminal (feedback signal)
The pulse signal according to the revolution speed is output and it is input into the pin 32 of the
microcomputer LSI1 via the circuit consisting of R47, R44, R45, and C42.
The microcomputer recognizes the current revolution speed based on this PG signal, and
controls the Vs signal above to keep the speed to the designated level.