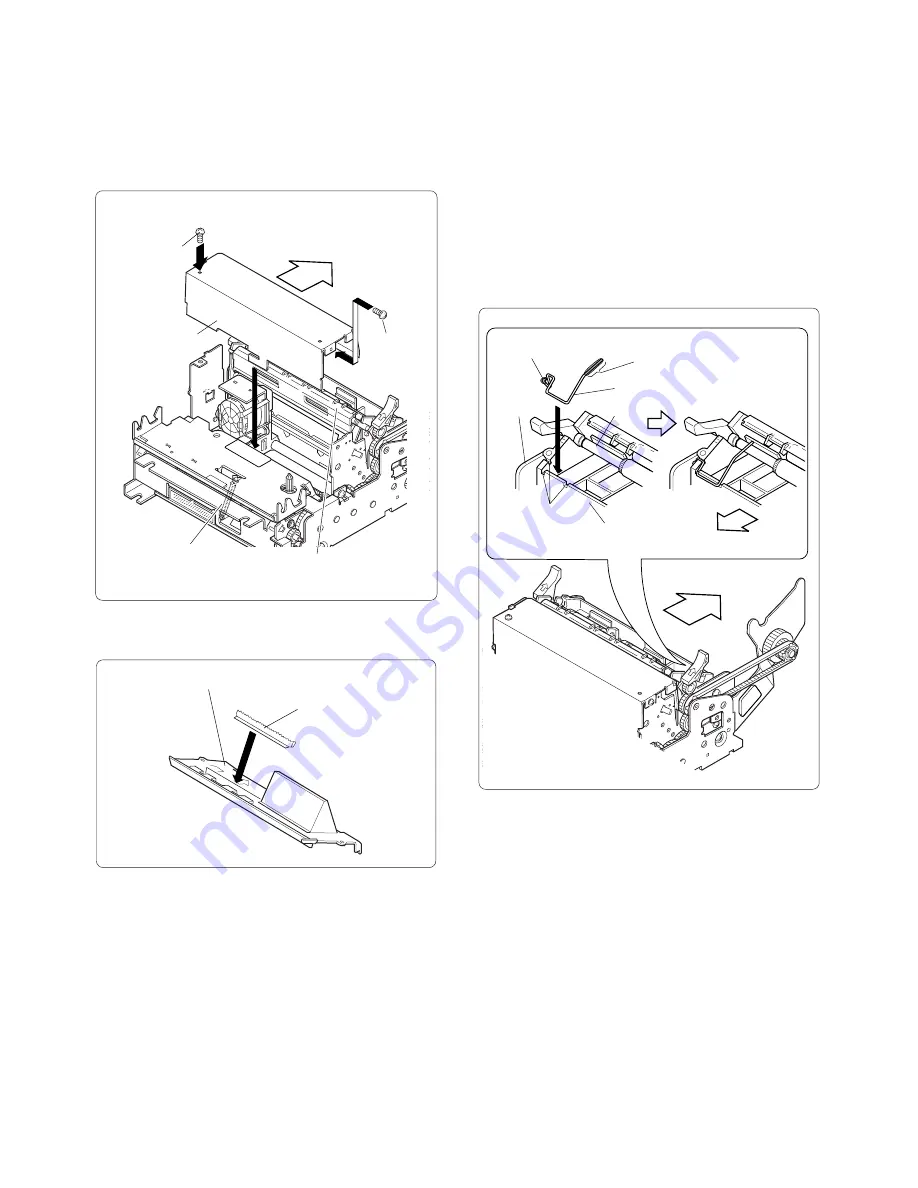
22
(68)
Note: 1. Insert the grounding spring between the
right side of the PF housing assembly and
the right side plate of the main frame
assembly.
2. Fit the bent sections of the grounding
spring into the positioning slits on the PF
housing assembly.
3. The bent tip of the grounding spring must
contact the PF shaft.
Rear
PF housing assembly
Right
side plate
Grounding spring
PF shaft
Positioning slit
Rear
Bent tip
(Apply EPINOC AP-1)
Protrusion
(Apply EPINOC AP-1)
(67) Mount the manual cutter on the 2-station housing cover.
2-station housing cover
Manual cutter
(65) Insert the ribbon plate spring in the ribbon plate
assembly and the main frame assembly front center.
(66) Mount the head cover on the main frame assembly
and fasten with fastening screws (M3x5).
Note:
While installing, the PF housing assembly
should be open.
Rear
Fastening screw
Fastening
screw
Head cover
Ribbon plate spring
PF housing assembly
Install the grounding spring in the PF housing
assembly.