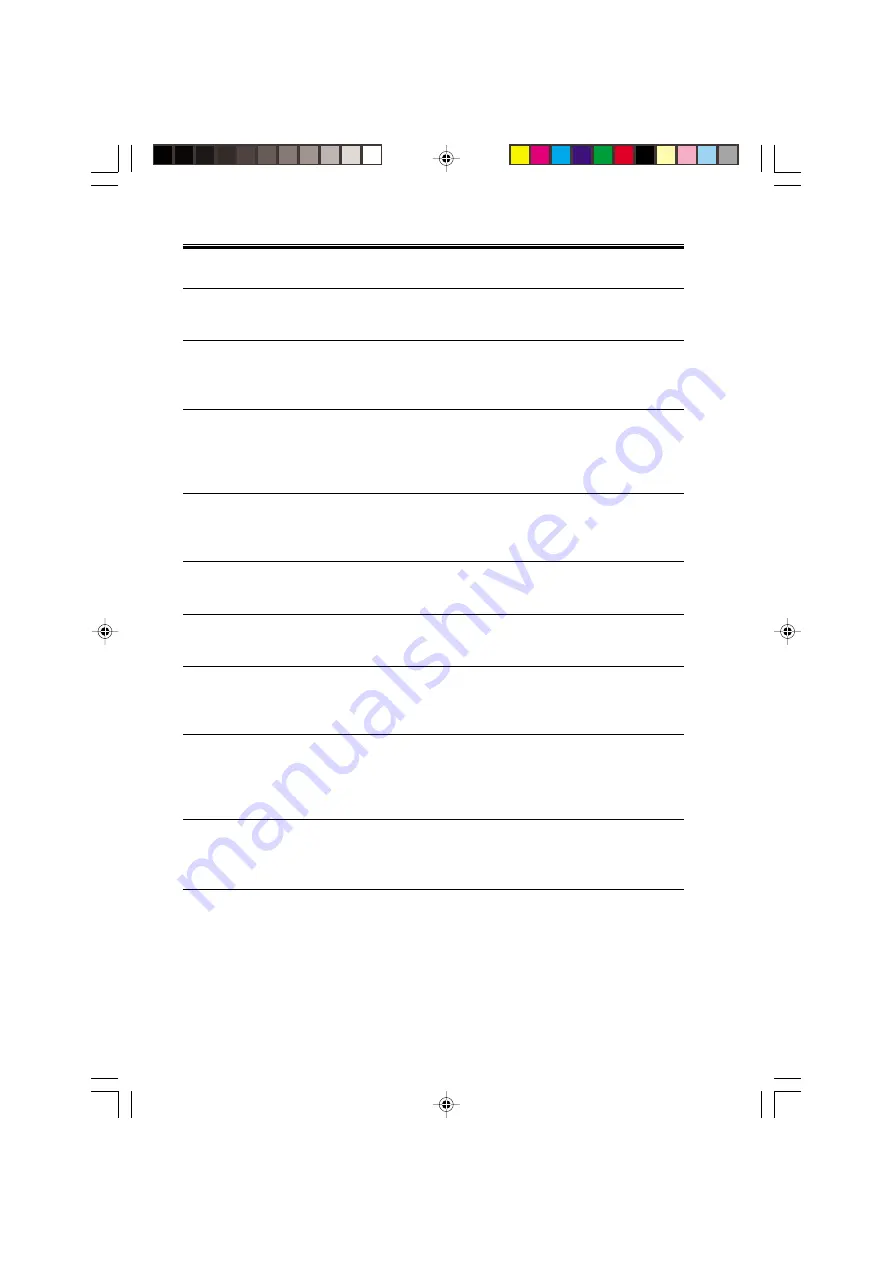
5-24
CHAPTER 5 TROUBLESHOOTING
COPYRIGHT © 2001 CANON INC.
2000 2000 2000 2000
CANON SADDLE FINISHER G1 REV.0 MAR. 2001
4.1.15 E550, Finisher Unit Power Supply Fault (detail code: 10)
Finisher controller PCB, Host machine DC controller PCB
1) Turn off and then on the host machine. Is the problem corrected?
YES: End.
Wiring
2) Is the wiring between the finisher controller PCB and the host ma-
chine DC controller PCB normal?
NO:
Correct the wiring.
Power supply
3) Measure the voltage between CN1-1 (+) and CN1-3 (-)/CN2-1 (+)
and CN2-3 (-) on the finisher controller PCB. Is it 24 VDC?
YES: Replace the finisher controller PCB.
NO:
Replace the host machine DC controller PCB.
T05-401-15
4.1.16 E577, Paddle Motor Fault (detail code: 01/02/03/04)
Paddle home position sensor (PI2)
1) Check the paddle home position sensor. Is the sensor normal?
NO:
Replace the sensor
Swing guide home position sensor (PI3)
2) Check the swing guide home position sensor. Is the sensor normal?
NO:
Replace the sensor.
Wiring
3) Is the wiring between the finisher controller PCB and the paddle
motor normal?
NO:
Correct the wiring.
Paddle, Swing guide assembly
4) Try turning the paddle motor clockwise and counterclockwise by
hands. Is there mechanical tapping in the rotation of the paddle or
the up/down movement of the swing guide?
YES: Correct the mechanical mechanism.
Paddle motor (M2), finisher controller PCB
5) Try replacing the paddle motor. Is the problem corrected?
YES: End.
NO:
Replace the finisher controller PCB.
T05-401-16
Chap05.p65
3/28/01, 12:11 PM
24