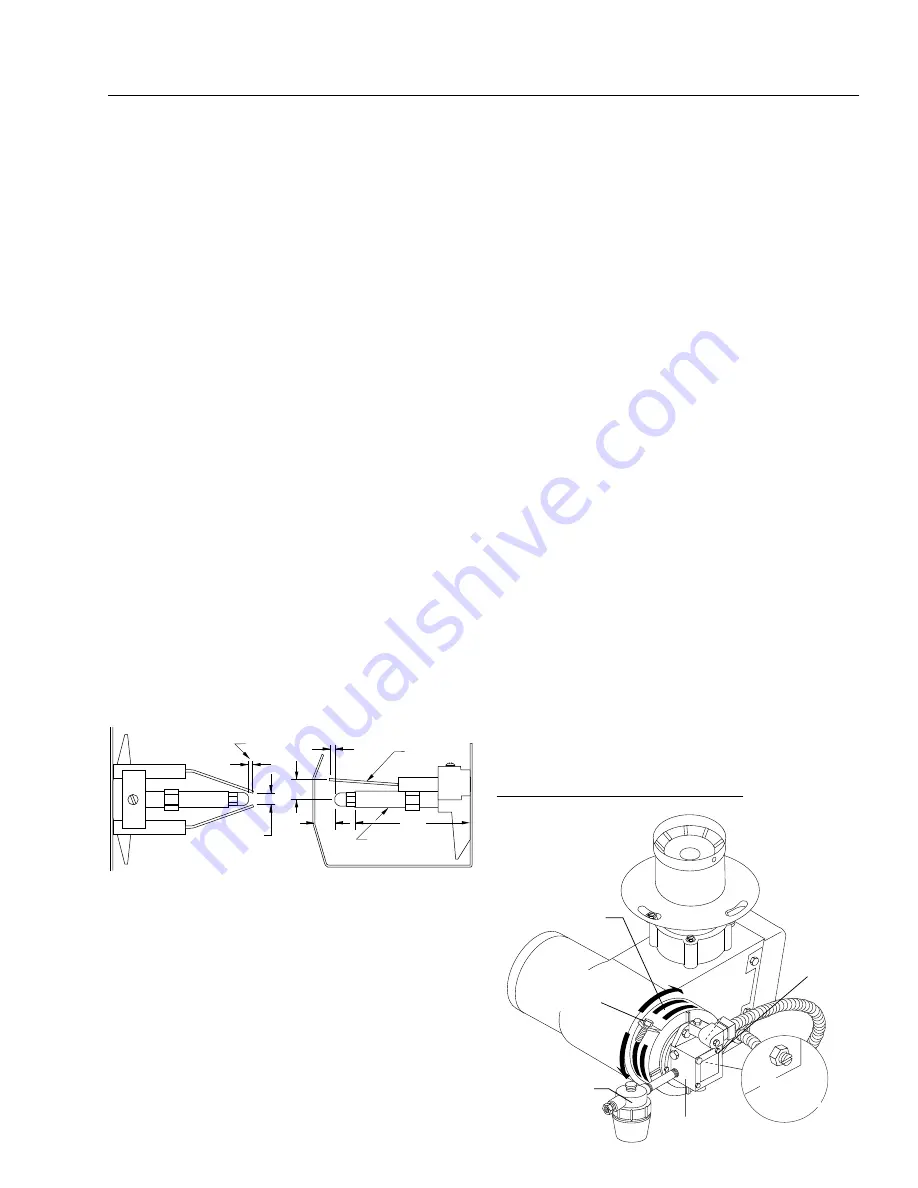
HPB SERIES PRESSURE WASHER
OPERATOR’S MANUAL
11
4. Clean, repair and replace the coil by reversing the
above steps.
Coil Reinstallation
Reinstall by reversing the above steps 4 through 1.
Rupture Disk
If pressure from pump or thermal expansion should ex-
ceed safe limits, the rupture disk will burst, allowing high
pressure to be discharged through hose to ground. When
the disk ruptures, it will need to be replaced.
Fuel:
Use clean fuel oil that is not contaminated with water
and debris. Replace fuel filter and drain tank every 100
hours of operation. Use Kerosene No. 1 or No. 2 Heating
Fuel (ASTM D306) or diesel only.
NEVER
use gasoline
in your burner tank. Gasoline is more combustible than
fuel oil and could result in a serious explosion.
NEVER
use crankcase or waste oil in your burner. Fuel unit mal-
function could result from contamination.
Ignition Circuit:
Periodically inspect wires, spring contact and electrodes
for condition, security and proper spacing.
For trans-
former test (CAUTION 10,000 VOLTS)
use defect free
insulated screwdriver and keep fingers off blade! Lay
blade across one contact: OK if arc will span 1/2" be-
tween end of blade and other contact (see illustration).
Electrode Setting:
(See illustration below)
Burner Nozzle:
Keep the tip free of surface deposits by wiping it with a
clean, solvent-saturated cloth, being careful not to plug
or enlarge the nozzle. For maximum efficiency, replace
the nozzle each season.
Fuel Control System:
The HPB utilizes a fuel solenoid valve located on the fuel
pump to control the flow of fuel to the combustion cham-
ber. This solenoid is activated by a pressure switch located
on the unloader valve. When an operator releases the trig-
Electrodes Check: Periodically check wiring connections.
If necessary to adjust electrodes, use diagram.
Gap
1/8"
3/16"
Side View
1/8"
3/8"
1/2"
2-7/8"
Electrodes
Nozzle Adapter
Top View
ger on the spray gun, the pressure drops, allowing the pres-
sure switch to activate the fuel solenoid. The solenoid then
closes, shutting off the supply of fuel to the combustion
chamber. Controlling the flow of fuel in this way gives an
instantaneous burn or no burn situation, thereby eliminat-
ing high and low water temperatures, and combustion
smoke normally associated with machines incorporating
a spray gun. Periodic inspection is recommended to in-
sure that the fuel solenoid valve functions properly. This
can be done by operating the machine and checking to
see that when the trigger on the spray gun is in the off
position, the burner is not firing.
Fuel Pressure Adjustment:
To adjust fuel pressure, turn the adjusting screw with a
5/32" allen wrench (located on the fuel pump) clockwise
to increase, counterclockwise to decrease. Do not ex-
ceed 200 PSI.
Air Adjustment
Machines are preset and performance tested at the fac-
tory — elevation 100' above sea level. A one time cor-
rection for your location will pay off in economy, perfor-
mance and extended service life. If a smoky or eye-burn-
ing exhaust is being emitted from the stack, two things
should be checked.
First, check the fuel to be certain that kerosene or No. 1
home heating fuel is being used.
Next, check the air adjustment on the burner. An oily, black,
smoky fire indicates a lack of air and the air band should
be moved to allow the air to flow through the burner. Sharp,
eye-burning white fumes indicate too much air flowing
through the combustion chamber. The air band should be
moved to allow less air to flow through the burner.
FUEL AIR ADJUSTMENT
Air Band
Pressure
Adjustment
Screw
Fuel Pump
Pressure
Gauge
Port
Air Band
Adjustment
Screw
Fuel Filter