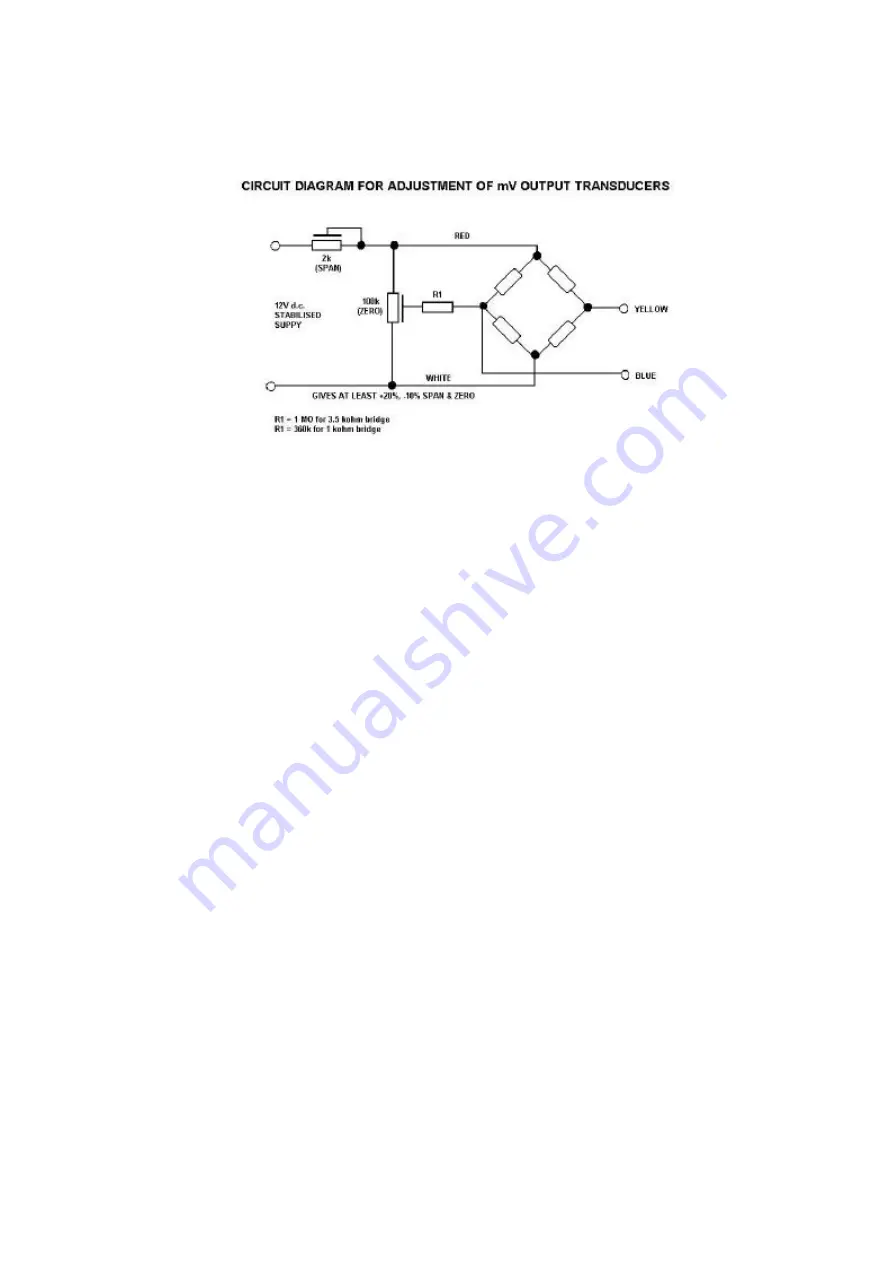
MAINTENANCE
Routine Inspection
: Not required except for periodic inspection of the cable and molding to ensure
that these are neither damaged nor softened by incompatible liquid.
If Malfunction Occurs
: Isolate the free end of the cable and measure the input and output
resistance. If vastly different from specification, either lower or higher, the strain gauge is damaged and
the instrument will have to be replaced.
If the reading is satisfactory but the operation is still suspect, join the input and output conductors
together. Using a low voltage insulation tester, measure the insulation resistance between the conductors
and the case; the reading should be 100 Mohms or greater.
DO NOT
use high voltage insulation testers or any device which generates more than 50V d.c. for this
test.
Causes of Failure
: Excess pressure of more than twice the rated range (1.5 times rated range for
Inconel "wetted parts" versions). A short duration pressure cycle having such a peak value may be
sufficient to damage the strain gauge.
The instrument may withstand some excess pressure without failure, but a change in residual output may
result. If this is not excessive the instrument may be re-zeroed externally, although other changes in
characteristics might occur which can only be determined by total re-calibration.
Failure can also occur if the system is driven into resonance by a fast pressure pulse, even though the
pulse peak is within the nominal pressure range. System resonance is sometimes referred to as "water
hammer" and is typically the result of valve slam or bounce, causing a shock wave through the system.
Use a pressure restrictor such as part number GA32 if it is suspected that adverse transient pressure
pulses are present.