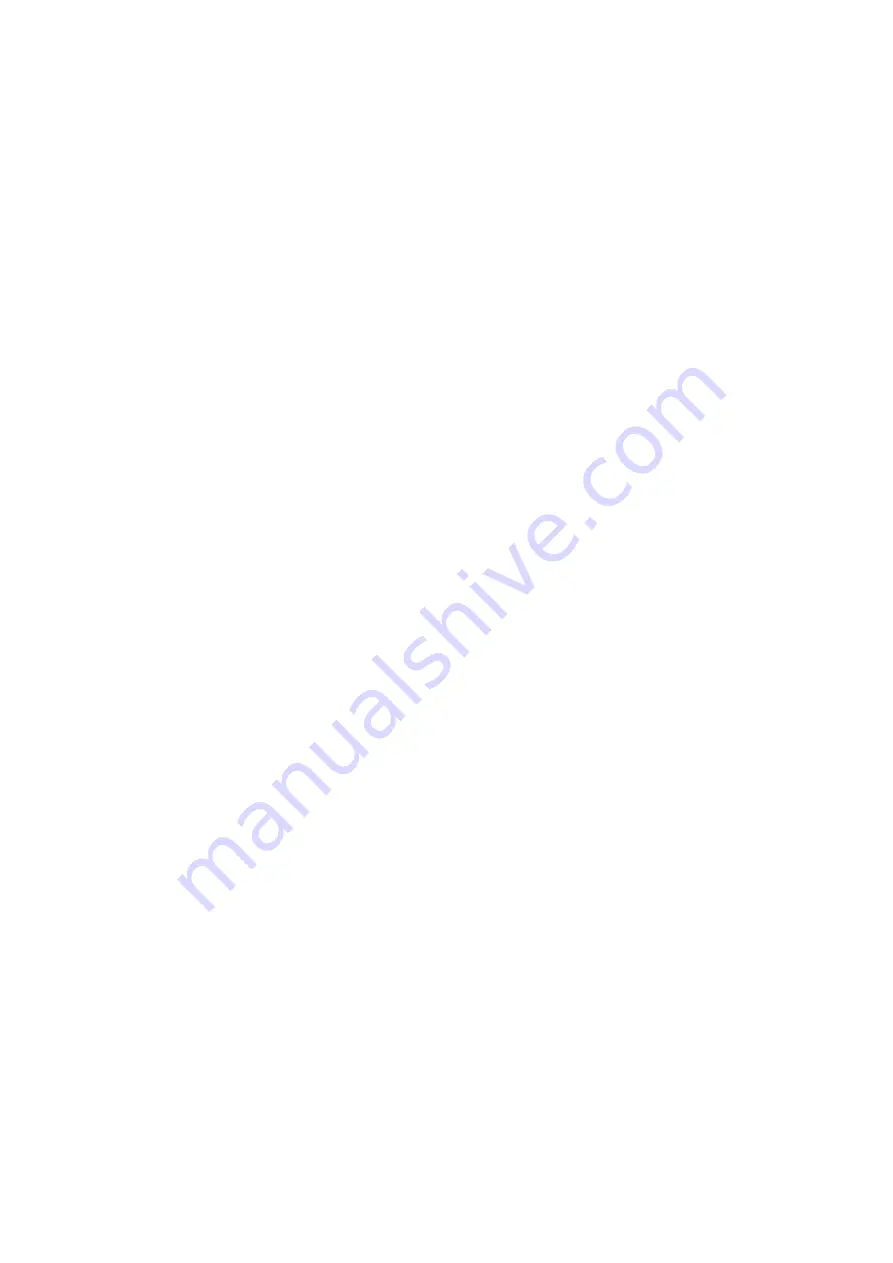
TA Operation/Maintenance Instructions Page 15 of 36
6.9 Blade Changing
Saws should be regularly examined to check that the plate is free from cracks and is true,
that the tips are firmly held in position and damage free. The teeth should be sharpened
the moment they become dull. The Grinding of TCT Sawblades requires specialised
equipment. This creates a tendency to retain the blade in the saw long after initial dulling
takes place. This is a false economy.
To remove the sawblade first isolate the machine, then remove the gap plate. Loosen
screw ‘A’ on the sawguard and tilt the front of the guard upward to expose the blade.
Rotate the blade until one of the holes in the saw spindle (behind the fixed collar) is
exposed through the slot in the cradle plate. Slide the spindle lock bar down the slot and
into the exposed hole. This will prevent the spindle from rotating. Use the Saw Spanner
provided to loosen and remove the securing nut. Note the direction of the thread, left
hand. Finally remove the loose saw collar and blade. The use of a wire hook for
transferring the saw to the tool room reduces the risk of cut fingers and damaged saw
teeth (if the blade is dropped when carrying it by hand).
To replace the blade clean both saw collars, ensure that the sawblade being fitted is
clean and sharp, and place onto the spindle ensuring that the direction of rotation is
correct.
Replace the loose saw collar and saw nut and tighten.
Important: Remove the spindle lock bar prior to replacing the gap plate, levelling the
sawguard, and re-
tightening screw ‘A’.
7.0 Blade Selection
The machine’s designation (e.g. TA315) indicates maximum sawblade diameter in mm.
Spindle speed is set accordingly, and we do not recommend the use of smaller diameter
sawblades, which require a much faster running speed. When using a smaller diameter
sawblade , be sure that its rpm rating is correct for the saw. The blade’s peripheral speed
will decrease. This means that feed speed (speed at which stock goes through the blade)
will also decrease. This could mean increased friction and burning. Smaller diameter
blades should have fewer teeth than the larger diameter blade that has been removed.
Do not attempt to use a blade that is less than 200mm dia on the TA315.
All blades will require a 30mm bore and a 14mm pinhole (25mm from centre to centre).
Selecting the correct blade for each operation is an essential link in the sawing process.
Your guarantee will be invalidated if you do not select the correct cutting tools.
The sawblade supplied with the machine is a 32-tooth tungsten carbide tipped anti-kick
back blade, with alternate top bevel and raker teeth to give a good finish for both ripping
and crosscutting applications. Its anti-kick back feature limits the size of bite any tooth can
take, and therefore the grip that the saw has on the wood, giving the operator better
control of the stock. It does however make the blade unsuitable for deep ripping. When
cutting material in excess of 76mm, use a blade which is expressly designed for this
purpose. Misuse will put undue load on the motor, which could cause long-term damage
to the motor windings.
Tungsten Carbide Tipped sawblades will stay sharp for much longer than conventional
saws and will produce a much higher quality of cut. The following table gives examples of
the type of TCT blades available, and their applications:
Содержание TA315
Страница 1: ...TA315 TILT ARBOR SAWBENCH OPERATION AND MAINTENANCE INSTRUCTIONS MACHINE SERIAL NO TAH...
Страница 33: ...TA Operation Maintenance Instructions Page 33 of 36 10 2 TA315 Three Phase Wiring Diagram...
Страница 34: ...TA Operation Maintenance Instructions Page 34 of 36 10 2 TA315 Single Phase Wiring Diagram...