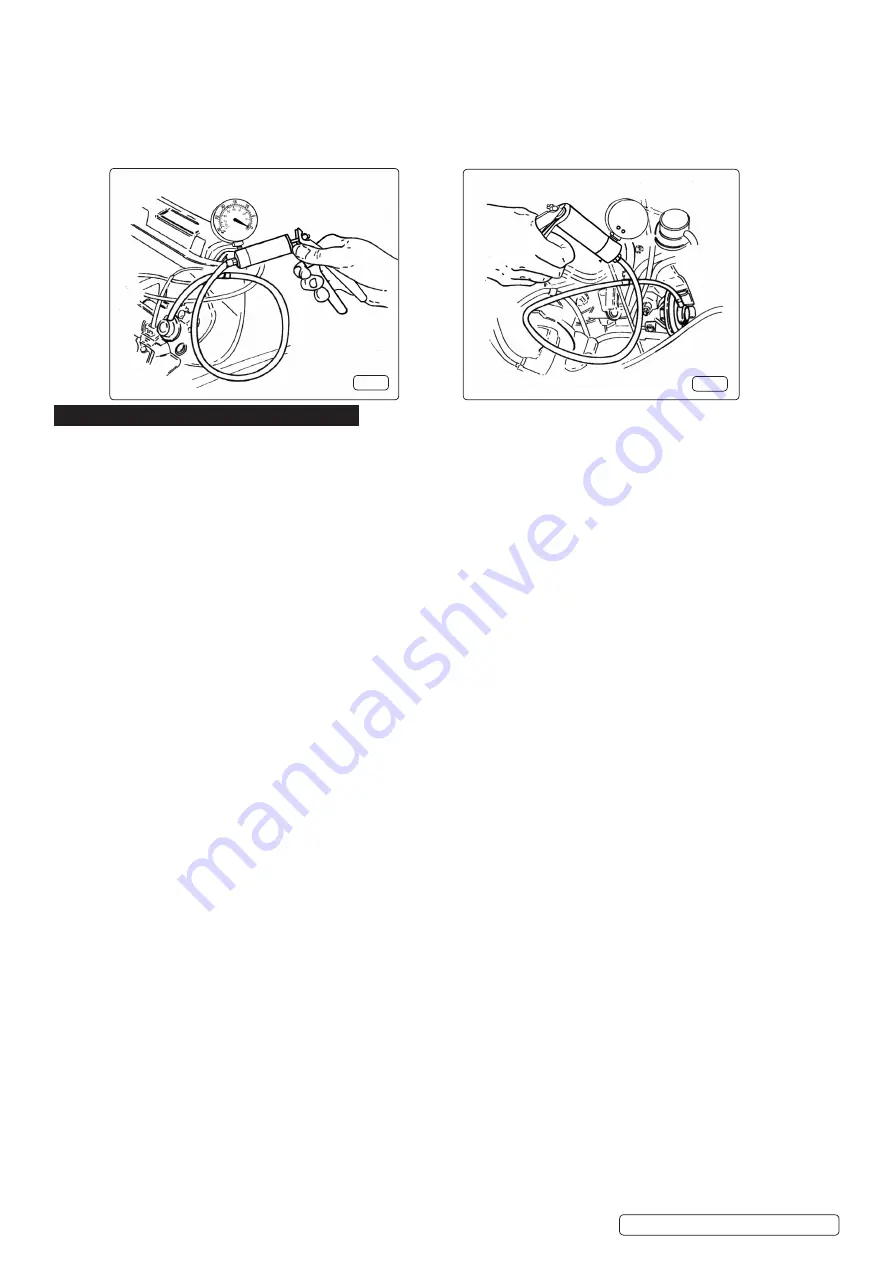
remove and block off the vacuum supply line to the pressure regulator, connect and operate the VS402 vacuum pump (fig.5) to
simulate vacuum pressures in accordance with the manufacturer’s specifications and note variation in fuel pressure reading.
6.4.
Testing Emission Control Exhaust Gas Reclrculation Valves (EGR)
6.4.1.
Start engine and run at idle until normal operating temperature is reached. Remove the vacuum line from the EGR valve and attach the
VS402 vacuum tester kit (fig.6). Operate the hand pump to apply approximately 15inHg of vacuum. If the EGR Valve is working
correctly the engine idle will become rough. If the idle remains unchanged the valve is possibly seized in the closed position. If
the vacuum is not held, the diaphragm in the valve has failed.
7. ADDITIONAL VACUUM SYSTEMS
7.1.
Testing One-Way Valves
7.1.1.
Many vacuum operated circuits use in-line one-way valves to apply vacuum in one direction only.
7.1.2.
To test the function of the valve remove it from the circuit. Attach the VS402 vacuum tester (fig.7) and operate pump to apply vacuum.
In one direction the valve should hold vacuum and in the opposite direction it should not.
7.2.
Testing Electrically Operated Vacuum Solenoids
7.2.1.
Electrically operated vacuum solenoids are commonly used in control circuits for air conditioning/ventilation systems, emission control
systems, idle step up systems etc. and testing the function of these when using the VS402 is extremely simple.
7.2.2.
Locate the solenoid to be tested and remove the line that goes to the component being tested. Connect the VS402 to the solenoid
port (fig.8) and start the engine. With the system turned off there should be a zero gauge reading. Now turn the system to the ‘on’ position
and a gauge reading equal to the manifold vacuum should be observed, if no reading exists remove the vacuum supply line and test for
manifold vacuum at this point. If the vacuum does exist this indicates that the solenoid is faulty or it is not receiving a ‘switch on’ voltage
(use a multimeter to test this). If no vacuum exists trace the supply line back to the vacuum source checking for kinks and breaks.
7.3.
Testing Thermal Vacuum Switches
7.3.1.
There are many vacuum controlled circuits that must only operate when the engine reaches normal operating temperature. This is done
using thermal switches that remain in an ‘off’ position until a given temperature is reached.
7.3.2.
To test this type of switch, remove the vacuum supply line coming from the manifold to the switch and test for manifold vacuum. If this
vacuum is correct refit the supply line to the thermal switch and remove the opposing line from the switch. Attach the VS402 vacuum
tester to the port (fig.9) and start the engine. With a cold engine no reading should be noted. When the engine reaches normal operating
temperature a manifold vacuum reading should be noted.
7.4.
Testing Vacuum Operated Heater Taps
7.4.1.
Climate control ventilation systems are becoming very common on newer vehicles and most of the systems use vacuum operated taps to
control the heating modes. On the majority of makes and models, the system uses vacuum to turn the heater tap ‘on’.
7.4.2.
To test these remove the supply line from the tap vacuum module and connect the VS402 vacuum tester (fig.10). With the engine at
normal operating temperature locate and feel the heater return hose. With the heater tap in the ‘off’ position, this hose should be cold.
Now operate the vacuum pump to open the tap. The gauge reading must hold. If the tap is in working order, the return hose will begin to
heat. If the hose does not begin to heat, this indicates that the tap is faulty.
7.5.
Testing Vacuum Operated Remote Central Locking Systems
7.5.1.
Some makes and models use vacuum operated bellows mounted in each door to centrally lock and unlock the vehicles doors. These
systems use either manifold vacuum stored in a reservoir for use when the engine is not running or an electrically driven vacuum pump
which operates when the doors are locked or unlocked.
7.5.2.
In either system, the VS402 vacuum tester is ideal for testing each individual door bellows. To do this, remove the door trims as
required. Remove the vacuum supply lines from the bellows and attach the VS402 vacuum tester (fig.11) and operate to apply vacuum
to the bellows. Wait for 30 seconds, no drop on the gauge should be noted. If the bellows are found to be in order attach the vacuum
supply line to the VS402 vacuum tester and operate system to test for vacuum supply. If the vacuum supply does not exist or is low
trace back down the lines to the vacuum supply looking for kinks, restrictions or cracked lines. Repair as required and retest.
7.6.
Testing Automatic Transmission Vacuum Operated Modulator Valves
7.6.1.
Automatic transmissions are normally equipped with a vacuum operated modulator valve in order for the automatic transmission to detect
engine loads and adjust shift points to suit.
7.6.2.
The VS402 vacuum tester can be used to test both that the modulation valve diaphragm is serviceable and also to simulate varying
engine loads so modulator pressure readings can be recorded. To test the modulator valve diaphragm remove the vacuum supply line
from the valve and attach the VS402 vacuum tester. Operate the vacuum pump until approximately 15inHg is achieved and monitor
the gauge reading for approximately 30 seconds. No vacuum drop should be noted.
7.6.3.
To check modulator pressure readings attach a pressure gauge to the appropriate port on the transmission. Remove the vacuum supply
line from the modulator and attach the VS402 vacuum tester (fig.12). Start and run the engine and apply vacuum pressures. Monitor
readings and confirm that these are in conformance with manufacturer specifications.
fig.6
fig.5
V
S402.V3 | Issue - 1 14/09/16
Original Language Version
© Jack Sealey Limited