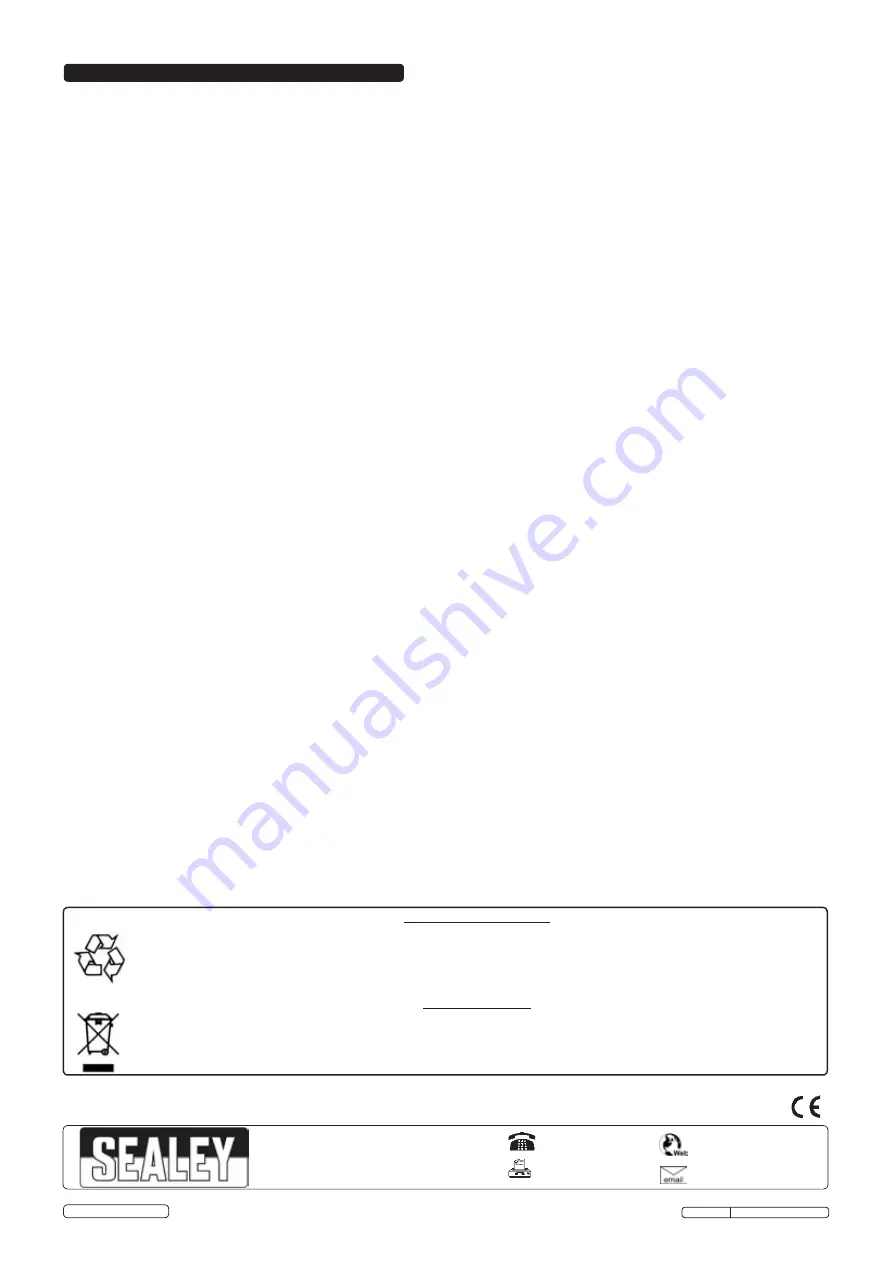
NOTE: It is our policy to continually improve products and as such we reserve the right to alter data, specifications and component parts without prior notice.
IMPORTANT:
No liability is accepted for incorrect use of this product.
WARRANTY:
Guarantee is 12 months from purchase date, proof of which will be required for any claim.
01284 757500
01284 703534
Sole UK Distributor, Sealey Group,
Kempson Way, Suffolk Business Park
,
Bury St. Edmunds, Suffolk,
IP32 7AR
www.sealey.co.uk
© Jack Sealey Limited
Environmental Protection
Recycle unwanted materials instead of disposing of them as waste. All tools, accessories and packaging should be
sorted, taken to a recycling centre and disposed of in a manner which is compatible with the environment.
When the product becomes completely unserviceable and requires disposal, drain off any fluids (if applicable)
into approved containers and dispose of the product and the fluids according to local regulations.
WEEE Regulations
Dispose of this product at the end of its working life in compliance with the EU Directive on
Waste Electrical and Electronic Equipment (WEEE). When the product is no longer required, it must be disposed
of in an environmentally protective way. Contact your local solid waste authority for recycling information.
WARNING!
Ensure that the lathe is unplugged from the power supply before attempting any maintenance.
7.1.
Before each use:
Lubricate the leadscrew bearings (oil point to left of scale at handle end and oil point behind gear D at driven end).
Lubricate the leadscrew thread and the leadscrew gears.
Lubricate the cross slide (oil point behind scale and two on front face of slide).
Lubricate the compound slide (two oil points on top face).
Lubricate the tailstock (two oil points on top face).
7.2.
Cleaning
Clean the machine after each use and oil all machined surfaces.
7.3.
Adjusting play in the slides
If any play becomes apparent in the slides adjust as follows:
a) Loosen the lock nuts (compound slide only) of the gib strip adjusting screws (fig.3.3 shows the screws for the compound slide.
Those for the cross slide are on the right-hand side of the slide, and those for the tail stock are either side of the locking lever).
b) Lightly tighten the screws equally and check that the slide will not move with normal effort on the handle.
c) Back-off each screw by ¼ of a turn (tighten the lock nuts, compound slide only).
d) Check that there is no play and that the slide moves smoothly.
e) If further adjustment is required, tighten or loosen the screws as necessary by
⅛
of a turn only and recheck.
7.4.
Headstock oil level
Headstock oil level should be at centre of sight glass (fig.4.D). If necessary top-up with a suitable oil via plug (fig.4.C)
7. MAINTENANCE
Original Language Version
SM27.V2 Issue: 2(L) - 06/03/15