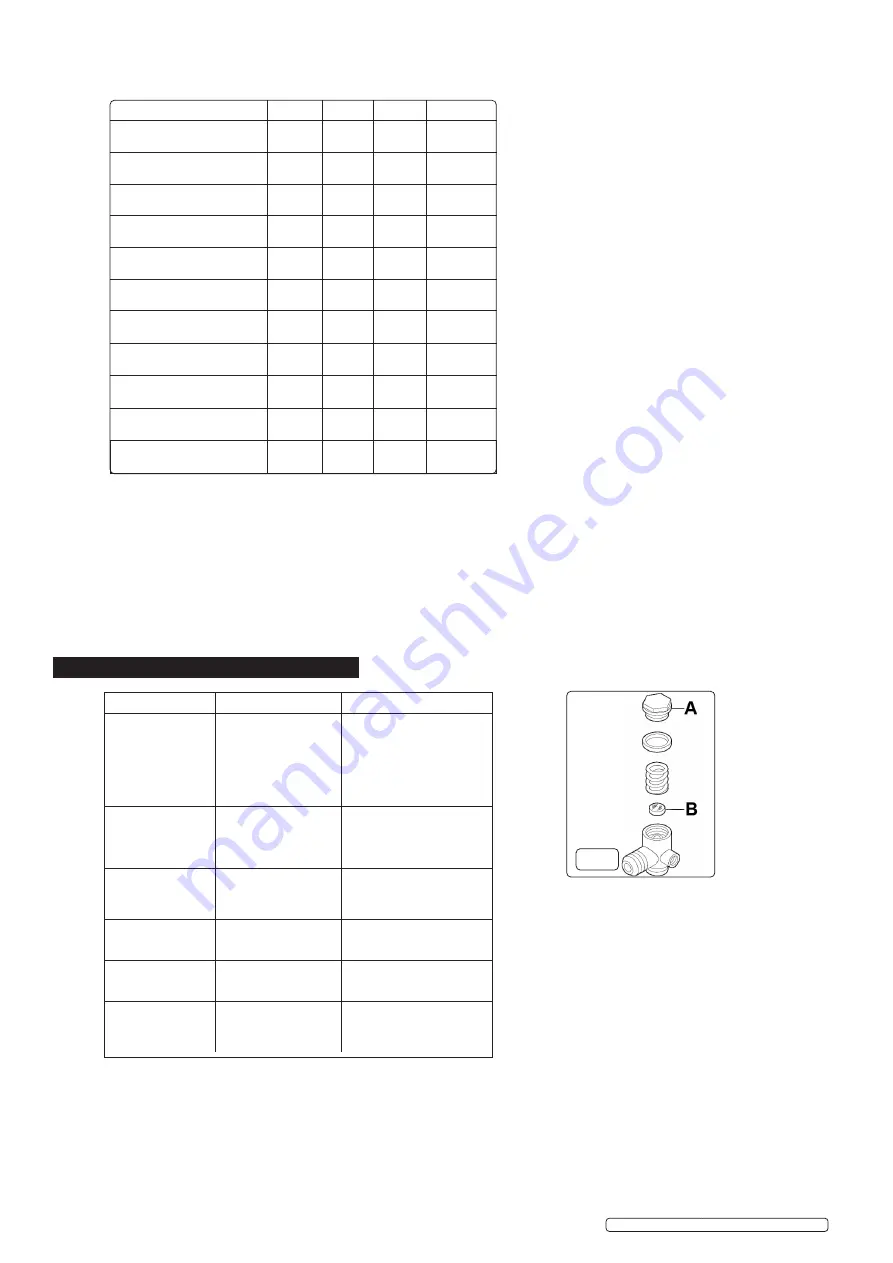
Original Language Version
© Jack Sealey Limited
c) Check all tube fittings and electrical connections.
d) Inspect pressure tank inside and out for damage or corrosion.
6.7.
MAINTENANCE SCHEDULE
6.8.
RECOMMENDED OILS
Synthetic oil suitable for temperatures ranging from -5°C to 45°C: Viscosity 5W50. We
DO NOT
recommend using mineral oil in
these compressors.
Part No. Qty. Description
FSO1 1ltr x 12 Compressor oil fully synthetic
FSO1S 1ltr x 1 Compressor oil fully synthetic
FSO5 5ltr x 1 Compressor oil fully synthetic
IMPORTANT WARNING
- Air contaminants taken into the compressor will affect optimum performance. Example: Body filler
dust or paint overspray will clog the pump intake filter and may cause internal damage to pump/motor components. Please note
that any parts damaged by any type of contamination will not be covered by warranty.
7. TROUBLE SHOOTING
Fault
Cause
Remedy
Pressure drop in the
tank.
Air leaks at
connections.
Run compressor to max.
pressure, switch off.
Brush soap solution over
connections and look for
bubbles. Tighten connections
showing leaks. If problem
persists contact Authorised
Service Agent.
Pressure switch
valve leaks when
compressor is idle.
Non-return valve seal
defective.
Discharge all tank pressure.
Referring to fig.4, and fig.9,
unscrew valve cap 'A'. Clean
rubber disc 'B' and its seat.
Refit all parts accurately.
Compressor stops
and does not restart.
Power failure.
Motor failure.
Check electricity supply and
fuse.
Contact Authorised Service
Agent.
Compressor does
not stop at max
pressure.
Pressure switch fault.
Contact Authorised Service
Agent.
Compressor does
not reach max
pressure.
Filter clogged.
Head gasket or valve
fault.
Replace filter element.
Contact Authorised Service
Agent.
Compressor noisy
with metallic knock.
Low oil level.
Bearing or piston
damage.
Turn off and top up oil
immediately.
Contact Authorised Service
Agent.
SAC20030B, SAC15030B Issue: 1 08/03/21
Maintenance Operations
Weekly 50hrs
100hrs
400 hrs
Drain condensation
•
Check oil level
•
Clean intake filter
•
Check for oil leaks
•
Replace oil
•
Check cut-out
•
General cleaning of
compressor
•
Replace air filter
•
Check tube fittings and
electrical connections
•
Internal & external
inspection of tank
•
Check and adjust belt
tension
•
fig.9