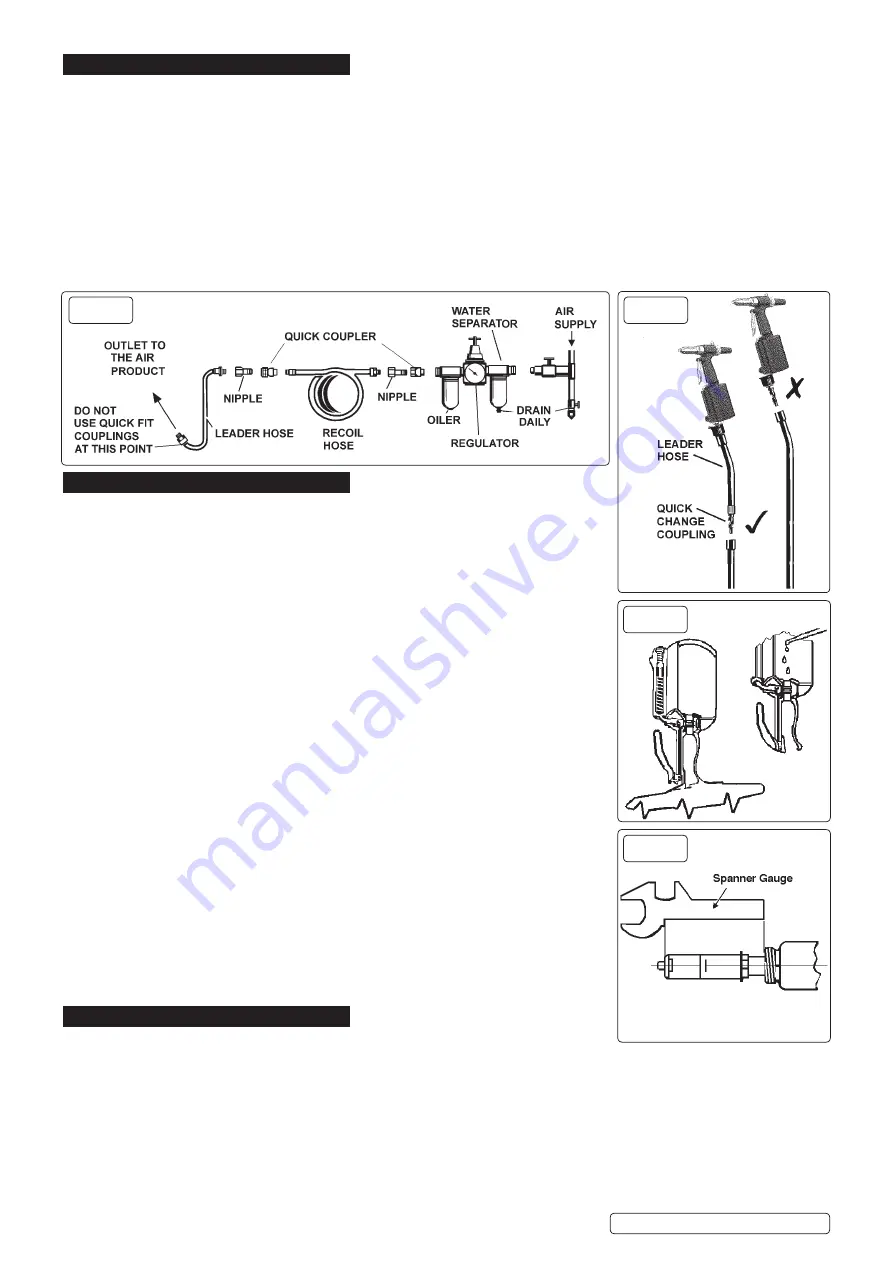
4. AIR SUPPLY
WARNING!
Ensure the air supply is clean and does not exceed 90psi while operating the riveter. Too high an air pressure and unclean
air will cause excessive wear, and may be dangerous, causing damage and/or personal injury.
4.1.
Ensure the riveter air valve (or trigger) is not depressed before connecting to the air supply.
4.2.
You will require an air pressure between 70-90psi, and an air flow according to the specification above.
4.3.
Drain the compressor daily. Water in the air line will damage the riveter and invalidate your warranty.
4.4.
Clean air inlet filter weekly. Recommended hook-up procedure is shown in (fig.1).
4.5.
Line pressure should be increased to compensate for unusually long air hoses (over 8 metres).
4.6.
The minimum hose diameter should be 1/4” I.D. and fittings must have the same inside dimensions.
4.7.
Keep hose away from heat, oil and sharp edges. Check hoses for wear, and make certain that all connections are secure.
4.8.
COUPLINGS
4.8.1.
Vibration may cause failure if a quick change coupling is connected directly to the air riveter. To overcome this, connect a leader
hose - Sealey model number AH2R or AH2R/38 - to the riveter. A quick change coupling may then be used to connect the leader
hose to the air line recoil hose (figs.1 & 2).
SA314.V5 | Issue 1 22/2/2019
Original Language Version
© Jack Sealey Limited
5. ASSEMBLY
WARNING! Ensure you have read, understood and applied the safety instructions.
This Tool is designed for riveting metal, primarily in workshops and garages. Not
recommended for any other use.
5.1.
FILLING WITH HYDRAULIC OIL
(Check each time before use).
5.1.1.
Disconnect the tool from the air line.
5.1.2.
Hold the tool upside-down and remove the air cylinder cap with a spanner.
5.1.3.
Remove piston set.
5.1.4.
Pump hydraulic oil into hydraulic cylinder until it overflows from the cylinder neck,
(fig.3) and wipe any excess oil away with a dry cloth.
5.1.5.
Insert hydraulic plunger into cylinder and press it in slightly.
5.1.6.
Reverse above procedure to reassemble. Slightly lubricate the inside wall of the air
cylinder.
5.2.
ADJUSTING THE STROKE
5.2.1.
Check that the hydraulic level is at its maximum (see
section
5.1.4. and fig.3).
5.2.2.
Check the jaw stroke by using the supplied wrench/gauge as in (fig.4) and adjust if
necessary (there is a 5mm tolerance).
5.2.3.
Hold the jaw case in place with a spanner and loosen the lock nut with the spanner
gauge supplied. Adjust the distance between them as required.
5.2.4.
Tighten the lock nut when adjustment is complete.
5.3.
CHANGING JAWS
5.3.1.
Disconnect the tool from the air line.
5.3.2.
Use a spanner to remove the frame head.
5.3.3.
Use both spanners to unscrew the jaw case.
5.3.4.
Remove the jaws and clean with a brush. If the teeth are blunted, replace with new jaws.
Use genuine Sealey parts only
(part No. SA314.V4-04)
.
5.3.5.
Reverse the above procedure to reassemble.
5.4.
OPERATION
5.4.1.
Be sure to select the correct nosepiece and rivet for the job; diameter and length.
5.4.2.
Insert the rivet mandrel full length into the nosepiece.
5.4.3.
Direct the nosepiece at the pre-drilled aligned holes and insert the rivet body full depth
through the elements to be joined.
5.4.4.
Squeeze the trigger until the rivet mandrel breaks.
5.4.5.
Empty the used mandrel ends from the reservoir periodically. Always replace the reservoir.
6. MAINTENANCE
IMPORTANT:
Rerer to section 5.1.
WARNING! Ensure you disconnect the tool from the air supply system before attempting any service or maintenance.
6.1.
Maintain the tool with care. Keep it oiled for optimum performance.
6.2.
Lubricate the air tool daily with a high quality air tool oil, (Sealey model no. ATO/500 or ATO/1000).
6.3.
Store the tool in a safe, dry, secure environment.
6.4.
Factors that may inhibit performance.
6.5.
Loss of power or erratic action may be caused by reduced compressor output, an excessive drain on the air line, moisture or
restrictions in air pipes or the use of hose connections of improper size. Grit or gum deposits in the tool may cut power and can be
corrected by cleaning the air strainer and flushing out the tool with gum solvent oil or an equivalent de-greaser. If all outside
conditions are in order, disconnect the tool from the air supply, disassemble and replace any worn or damaged parts with Sealey
original parts. Clean all parts, reassemble the tool and lubricate as described above. Alternatively, take the tool to your nearest
authorised service agent.
fig.1
fig.2
NOTE:
Wrench/gauge design may
differ from above.
See spare parts diagram.
fig.4
fig.3