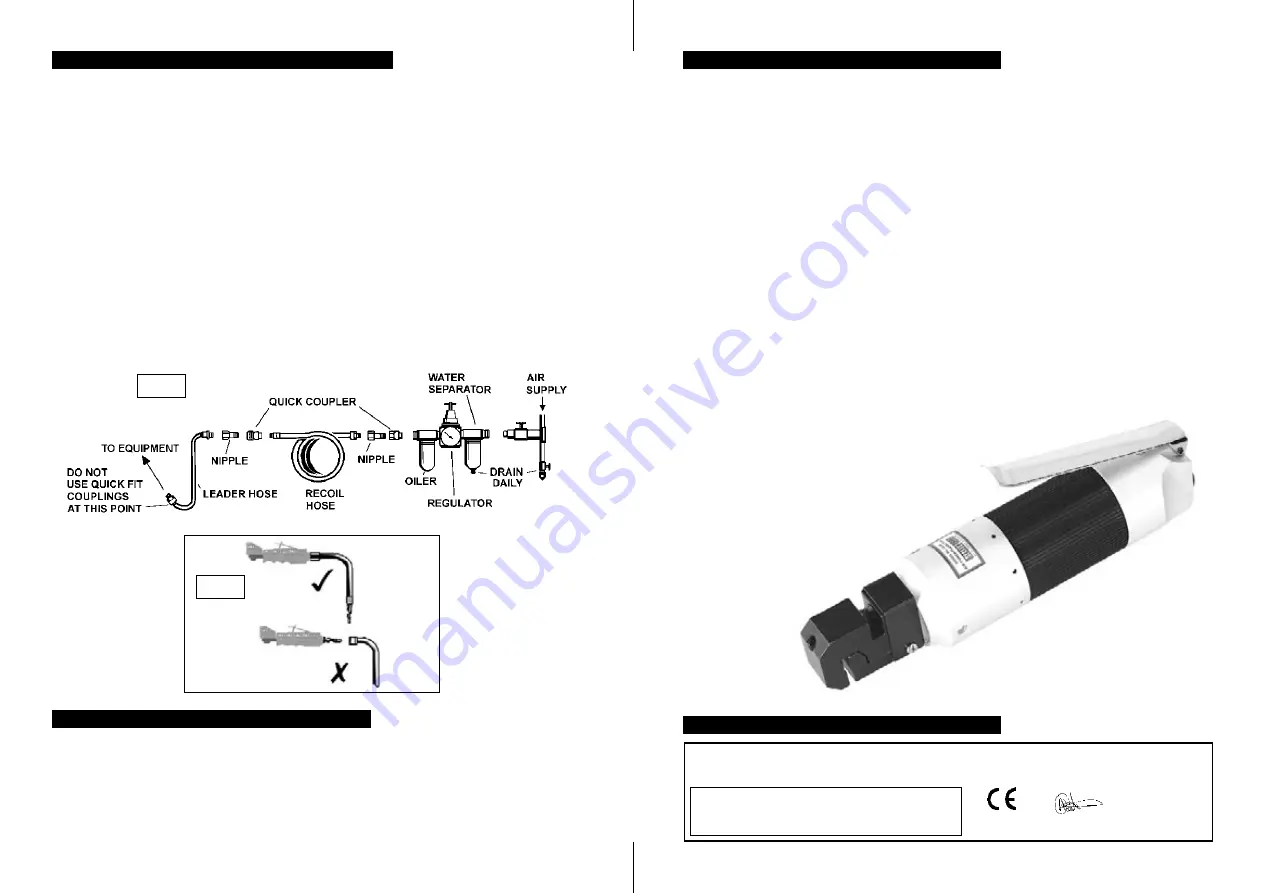
3.1. Air Supply
3.1.1. Ensure that the tool air valve is in the "Off" position before connecting to the air supply.
3.1.2.
p
WARNING!
Ensure the air supply is clean and does not exceed 90 psi (6.2 bar) while
operating the tool. Too high an air pressure and/or unclean air will shorten the life of the tool
due to excessive wear and may be dangerous causing damage and/or personal injury.
3.1.3. Drain the compressor air tank daily. Water in the air line will damage the tool.
3.1.4. Clean the compressor air inlet filter weekly. Recommended hook-up is shown in fig. 1.
3.1.5. Line pressure should be increased to compensate for unusually long air hoses (over 8 metres).
The minimum hose bore should be 3/8 and fittings must have the same inside dimensions.
3.1.6. Keep the hose away from heat, oil and sharp edges. Check hose for wear, and make certain
that all connections are secure.
3.2. Couplings
Vibration may cause failure if a quick change coupling is connected directly to the tool.
To overcome this, connect a leader hose to the tool. A quick change coupling may then be
used to connect the leader hose to the air line recoil hose. See figs. 1 & 2.
3.
PREPARING FOR USE
5. MAINTENANCE
6. DECLARATION OF CONFORMITY
p
WARNING!
Ensure that you read, understand and apply the safety instructions.
4.1. Connect the tool to the air supply.
4.2. To start the tool, hold firmly and squeeze the throttle lever. The clamp will move down,
punching a hole/forming a flange, as required.
4.3. Release the lever and the clamp will rise allowing the tool to be positioned for the next operation.
4.4. After use, disconnect the tool from the air supply, clean and store in a safe, dry, childproof location.
4. OPERATION
fig. 1
fig. 2
Declaration of Conformity
We, the sole importer into the UK, declare that the product listed here is in conformity
with the following standards and directives. The construction file for this product is held by the Manufacturer and may be
inspected, by a national authority, upon request to Jack Sealey Ltd.
For Jack Sealey Ltd. Sole importer into the UK
of Sealey Power Tools.
Air Punch/Flange Tool Model: SA36.V2
98/37/EC Machinery Directive
93/68/EEC Marking Directive
27th August 2002
Signed by Mark Sweetman
SA36.V2 - 1 -290802
Note: Numbers/letters in brackets refer to those on the parts diagram.
p
WARNING!
Disconnect the tool from the air supply before changing accessories, servicing or
performing maintenance. Replace or repair damaged parts.
Use genuine parts only.
Unauthorised parts may be dangerous and will invalidate the warranty.
5.1. If the compressed air system does not have an integral oiler then lubricate the tool daily with
a few drops of Sealey air tool oil dripped into the air inlet.
5.2. Regularly check oil, and top-up if necessary, via the oil plug (13). Use Sealey Hydraulic Jack
Oil, Part No. HJO/500ML, HJO/5L or HJO/25L.
5.3. Clean the tool after use.
5.4. Loss of power or erratic action may be due to the following:
a) Excessive drain on the air line. Moisture or restriction in the air pipe. Incorrect size or type of
hose connectors. To remedy, check the air supply and follow instructions in Section 3.
b) Grit or gum deposits in the tool may also reduce performance. If your model has an air
strainer (located in the area of the air inlet), remove the strainer and clean it. Flush out
the tool with gum solvent oil or an equal mixture of SAE 10 oil and paraffin. Allow to
dry before use.
5.5. For a full service contact your local Sealey service agent.
5.6. To remove and replace the punch (6) and/or die (3) proceed as follows:
1) Remove screws (7) and slide off cover plate (8).
2) Slacken set screw (2) and strike rear edge of clamp (1) with a soft-headed hammer in
order to unscrew it from the shaft of the hydraulic piston (31). If necessary the shaft may
be locked by removing the oil plug (13) and inserting a suitable rod into a hole in the shaft.
3) Fully unscrew the clamp (1) and anvil (9) assembly from the shaft.
4) Separate the anvil (9) and the clamp (1) to replace the
punch (6) and/or die. The die (3) is a push fit in
the clamp (1) and can be tapped out via the
waste bore (A). Push/tap in the replacement.
5) Reassemble the anvil (9), clamp (1) and the
replacement punch (6) and screw onto
the shaft. Tap with a soft-headed
hammer to ensure tightness and
lock with the set screw (2).
6) Refit the cover plate (8)
and retain with
screws (7).