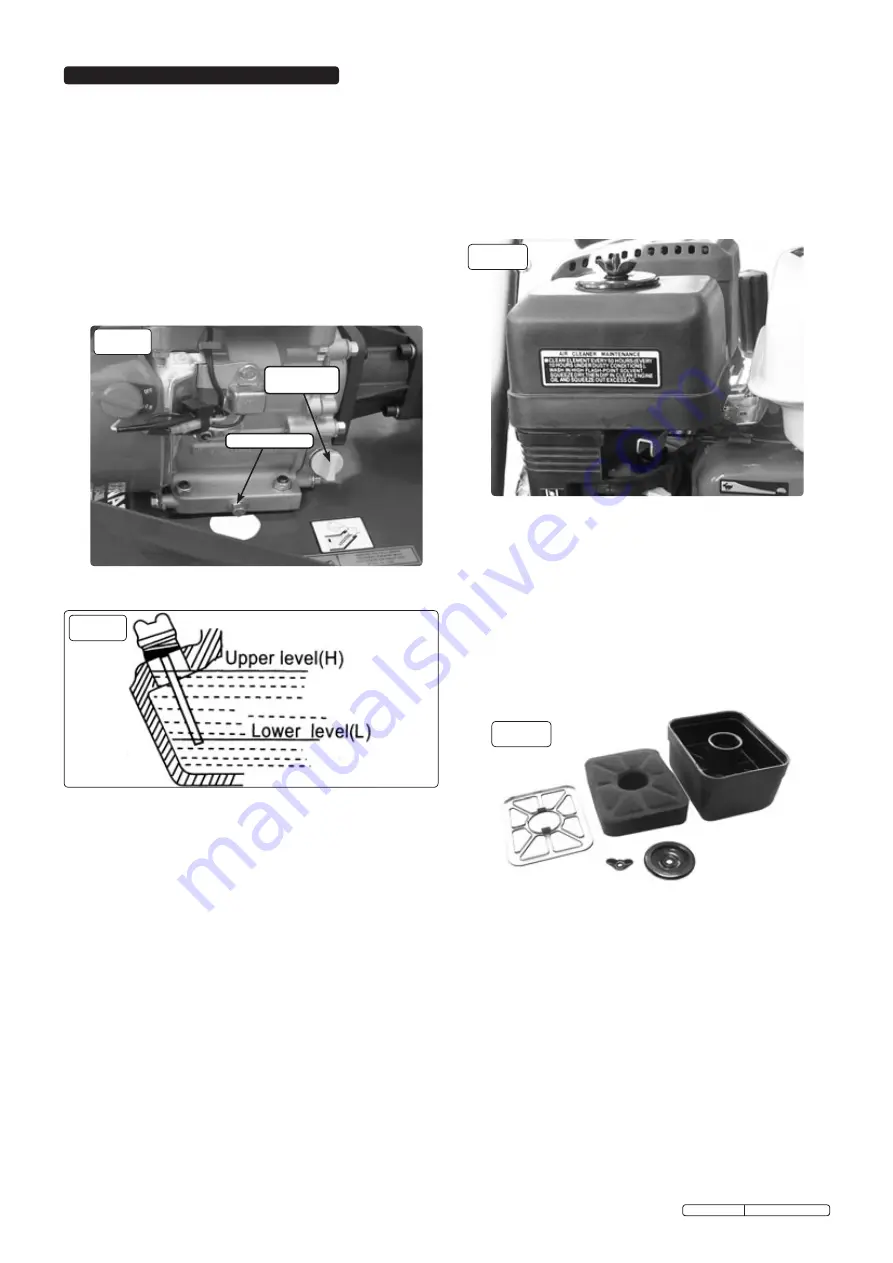
7. MAINTENANCE (ENGINE)
7.1
Change engine oil after the first 20 hours of operation.
Thereafter, change oil every six months or every 100 hours of
operation. Change oil more often if engine is operated under
heavy load, or in high ambient air temperatures. During
normal operation, partially burned fuel, small particles of
metal from the cylinder walls, pistons, bearings and
combustion deposits will gradually contaminate the oil. If the
oil is not changed regularly, these foreign particles can cause
increased friction and a grinding action which shortens the life
of the engine. Fresh oil also assists in cooling. Old oil
gradually becomes thick and loses its cooling ability as well
as its lubricating qualities.
fig.10
fig.11
7.2
CHECKING THE OIL LEVEL.
Ensure the unit is on a level
surface.
7.2.1 Unscrew the dipstick/oil filler cap (see fig.10) and wipe it
clean of oil. Note that the maximum oil level should be just
below the opening of the filler neck.
7.2.2 Check the oil level by seating the dipstick into the hole
without screwing it in. See fig.11 above. On removal the oil
level should be between the two marks on the dipstick. If it is
at the lowest level or below, top-up immediately with an
SAE10W30 oil.
7.2.3 Screw dipstick fully home to seal oil fill hole.
Note:
The engine is fitted with a low oil sensor which will
automatically shut the engine down in a low oil situation. The
sensor may also operate if the unit is not on a level surface.
7.3
CHANGING THE OIL.
7.3.1 Change the oil. Operate the engine for 3 minutes to warm the
oil then stop the engine using the shut down procedure
described in section 5.3. There is a hole in the chassis below
the oil drain plug. See fig.10. Place a suitable container below
the hole, remove the plug and allow the oil to drain. Replace
the drain plug and refill with fresh oil. Check the oil level using
the dipstick. Dispose of the old oil according to local authority
guidelines.
7.4
FUEL FILTER
: The fuel filter is in the neck of the fuel tank.
7.4.1 Clean it every 300 hours.
7.6
AIR FILTER.
To access the air filter element unscrew and
remove the wing nut and seal washer on the top of the cover.
Lift the air filter off its threaded mounting rod
7.6.1 Remove the metal retainer and the foam filter from the inside of
the outer air filter casing.
7.6.2 Wash the foam element with a household detergent or a high
flash-point solvent and squeeze dry. When the element is
thoroughly dry soak it in clean engine oil. Squeeze out any
excess oil, fit back into the outer casing and replace the metal
retainer.
7.6.3 Place the air filter back over the threaded rod and secure with
the seal and wing nut.
7.6.4 The foam element should be replaced after every 300 hours of
service.
fig.12
fig.13
7.5
ENGINE STORAGE.
If the unit is not to be used for more
than one month the following procedure should be followed.
7.5.1 Drain the fuel from the fuel tank, fuel line and fuel tap.
7.5.2 Ensure that the engine switch is in the off position and pull the
recoil starter handle slowly until an increase in pressure is felt
indicating that the piston has commenced its compression
stroke and leave it in this position. This closes both the intake
and exhaust valves and prevents the inside of the cylinder from
rusting.
7.5.3 Cover the unit and store it in a clean dry place that is well
ventilated and away from open flame or sparks.
Oil Drain Plug
Dipstick
and Oil Filler
7.7
CARBURETTOR.
To adjust the idling speed, turn the throttle
adjusting screw (fig.14) clockwise to increase and
anti-clockwise to decrease engine speed.
Standard idling speed:1700 +/- 15rpm
7.7.1 To clean the deposit cup (fig.14), set the fuel tap to OFF, undo
the central bolt and lower the deposit cup, take care not to spill
any fuel, dispose of old fuel in accordance with local authority
guidelines. Wash components in a non-flammable or high
flash point cleaning solvents, dry components and refit
components in reverse order. Turn fuel tap back ON and check
for leaks.
7.8
SPARK PLUG.
To remove the spark plug, pull off the spark
plug lead (fig.15) and remove the spark plug (fig.16) using the
spark plug wrench supplied (fig.18).
Note:
Care must be taken if the engine is hot due to the close proximity
of the exhaust silencer to the spark plug.
7.8.1 Clean spark plug using a wire brush and check the insulator for
damage, replace if damaged or at service schedule.
7.8.2 Check the electrode clearance (fig.17) with a feeler gauge,
adjust if required using a plug gap tool.
7.8.3 Replace spark plug and refit plug lead.
Original Language Version
PCM2500SP Issue: 2 - 16/10/09