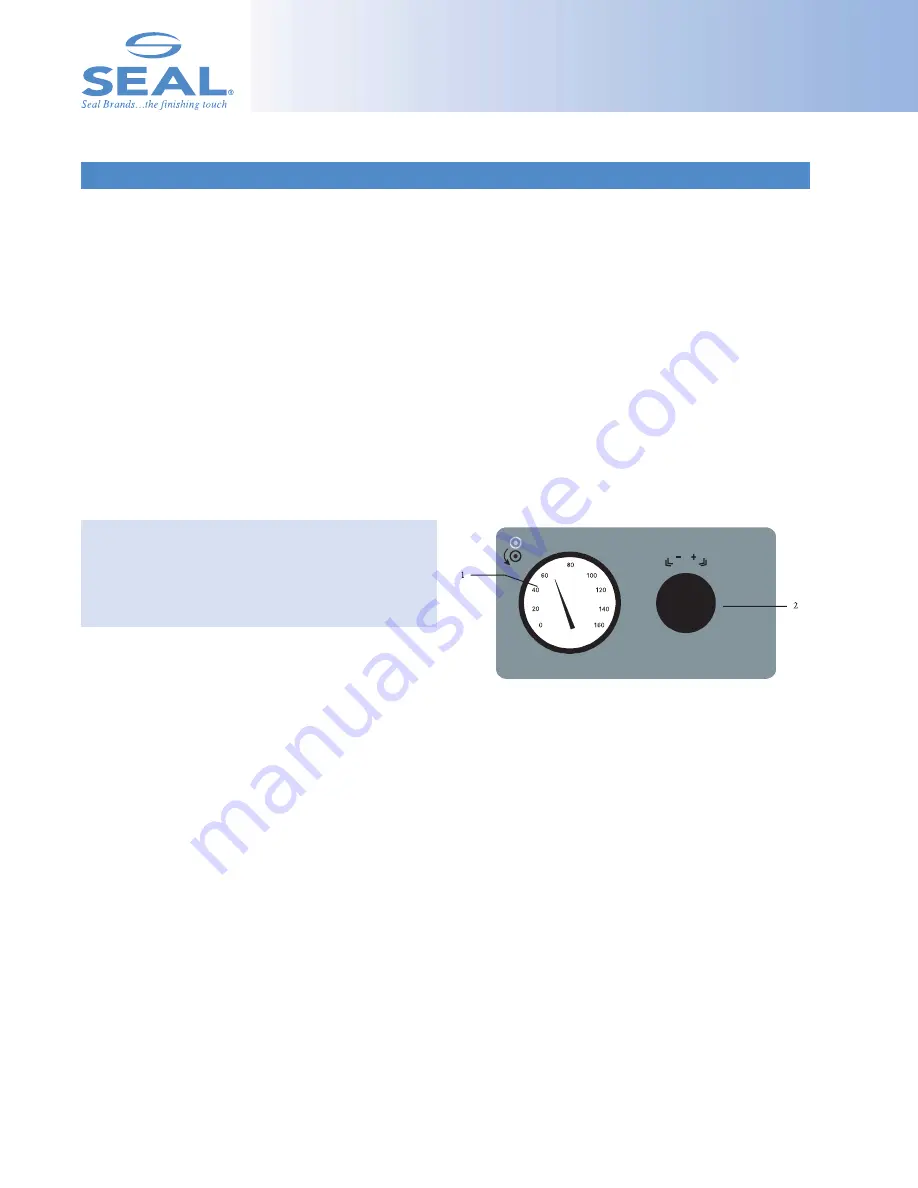
C L U T C H C O N T R O L P A N E L
14
The Clutch Control Panel is located on the left-side
cabinet when facing the rear of the laminator. The
operator can adjust the amount of tension that is
directly applied to the laminate between the main
and pull rollers. The amount of tension applied
affects the output and extreme pull tension will
stretch the hot films causing outfeed waves in the
finished product. This is a factor with films such as
Print Guard
®
, which stretches easily. Excessive tension
will also cause downward curl in the finished prod-
uct. The standard setting for normal operation is
40-60 PSI.
IMPORTANT! Excessive pull clutch tension will cause
premature wear to the drive system and may cause
damage to the laminator. Use the minimum amount
required for the laminating process.
1. AIR PRESSURE GAUGE
Indicates the PSI reading for the pulling tension of the
bottom pull roller. The standard setting for normal opera-
tion is 40-60 PSI.
2. AIR REGULATOR KNOB
This knob adjusts the pulling tension of the bottom pull
roller. Pull out the knob and turn to adjust; push back in
to set. Turn clockwise to increase the amount of pull ten-
sion and turn counter-clockwise to decrease the amount.
Figure 7. Clutch Control Panel