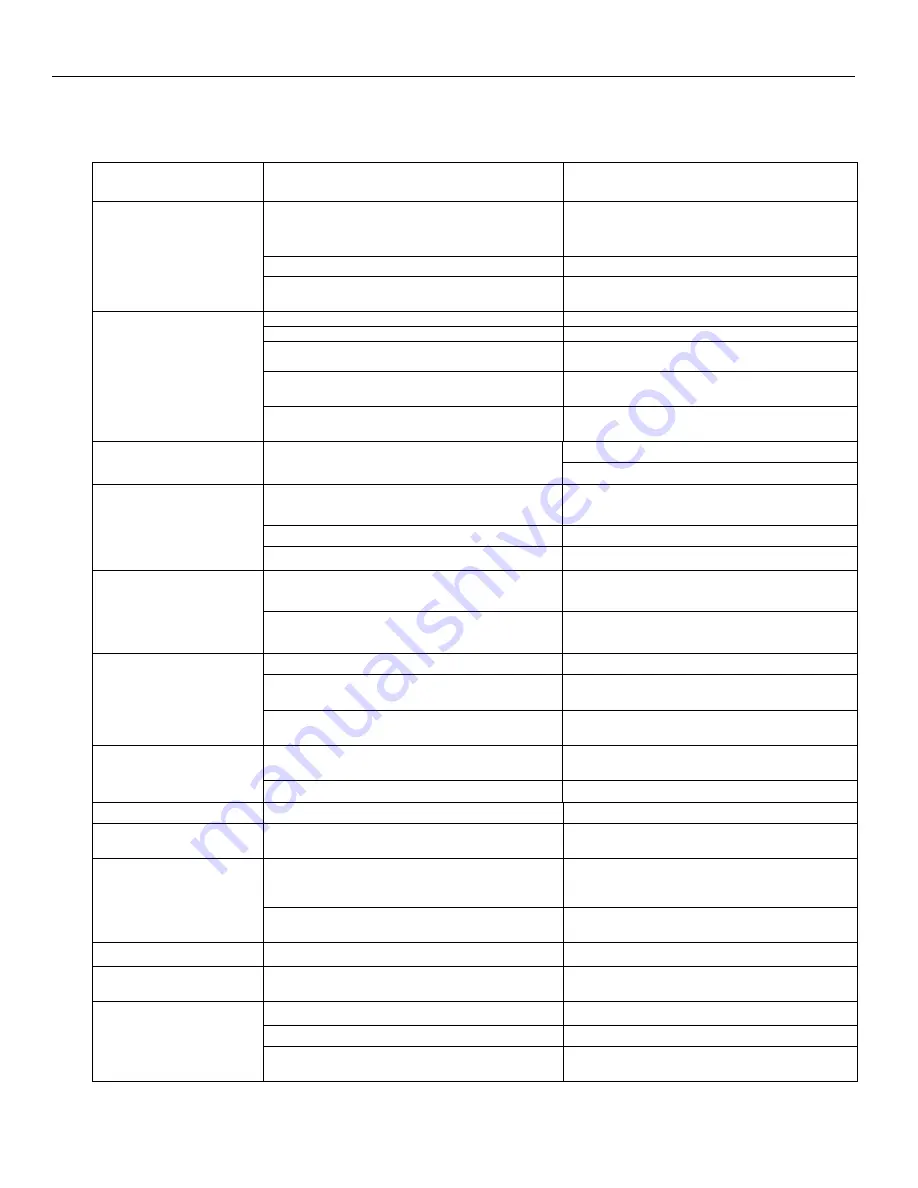
Troubleshooting Guide
19
PROBLEM
POSSIBLE CAUSE
SOLUTION
Pressure not released from rollers after machine was shut
down. The roller has an indentation where the two
rollers stayed in contact with one another.
Run machine for one or two hours with the pressure
on.
Horizontal lines may occur for the same reason.
Clean rollers with straight alcohol.
Coating is uneven
-or-
Horizontal lines are visible on
output.
If horizontal lines persist, roller may have been
permanently damaged.
Replace roller.
Rollers are not clean.
Clean rollers.
Lacquer level is too low.
Add lacquer to the correct level.
Lacquer is deteriorating (due to old age or because it has
been diluted with water).
Replace old lacquer.
Lacquer is too thick.
Restore lacquer to normal viscosity by adding a mixture
of alcohol (20%) and water (80%).
Coating is uneven
-or-
Vertical lines are visible on
output.
Lacquer is too thin
Run coating in machine with humidity dial on “0” until
coating reaches desired thickness (35-55 seconds).
Clean rollers with straight alcohol.
Random spots or marks on
output.
Dirt or dried lacquer may be stuck to the rollers. Lacquer
may have dirt in it.
Filter lacquer with paint strainer or fine wire filter.
Scraper tension is not enough.
Increase scraper tension (adjust scraper tension screws).
Scraper blade may be worn or have nicks.
Remove and replace scraper blade.
Lacquer appears on back of
image.
Scraper blade may have lacquer built up on blade.
Clean blade with alcohol.
Fans not running or defective.
Inspect fan operation and if faulty, call Technical
Service.
Prints not exiting machine.
Shutter is not open.
Open shutter, and if necessary remove jammed images
by running unit in reverse.
(Run) speed is too slow.
Increase speed.
Coating is too thin.
Run coating in machine with humidity dial on “0” until
desired viscosity is reached (35-55 sec).
Prints sticking to rubber
coating roller (common with
inkjet paper).
Set screws in gears may have come loose.
Tighten set screws making sure one set screw is on flat
side of shaft.
Not enough scraper blade tension.
Increase scraper blade tension (adjust scraper blade
screws-see page 16)
Prints wrapping around top
steel roller.
Run speed is too slow.
Increase speed.
Laminator does not turn on.
No power.
Verify that power cable is not loose.
Power switch fails to set.
Verify that the main power switch is in the “ON”
position.
Dried lacquer accumulating on roller brackets.
Clean unit. Remove and clean rollers and roller
bushings thoroughly. Inspect and clean roller brackets,
insuring there is no lacquer build-up.
Silicone roller(s) not turning.
Set screws in gears have come loose or backed out.
Tighten set screws making sure one set is on flat side of
shaft.
Motor will not run.
Blown fuse.
Check the 2.5A fuse and replace if blown.
Knocking sound or roller
hesitation.
Loose belt tension.
Remove top cover and check belt tension (should not
have any slack) Tighten is needed.
Bad connection from power source.
Ensure connection is made to nebulizer and fan.
Low water level.
Ensure 1 gallon jug is full with distilled water.
Low level light staying on.
Float directly on nebulizer may be stuck.
Free float in nebulizer to allow float to move freely up
and down.