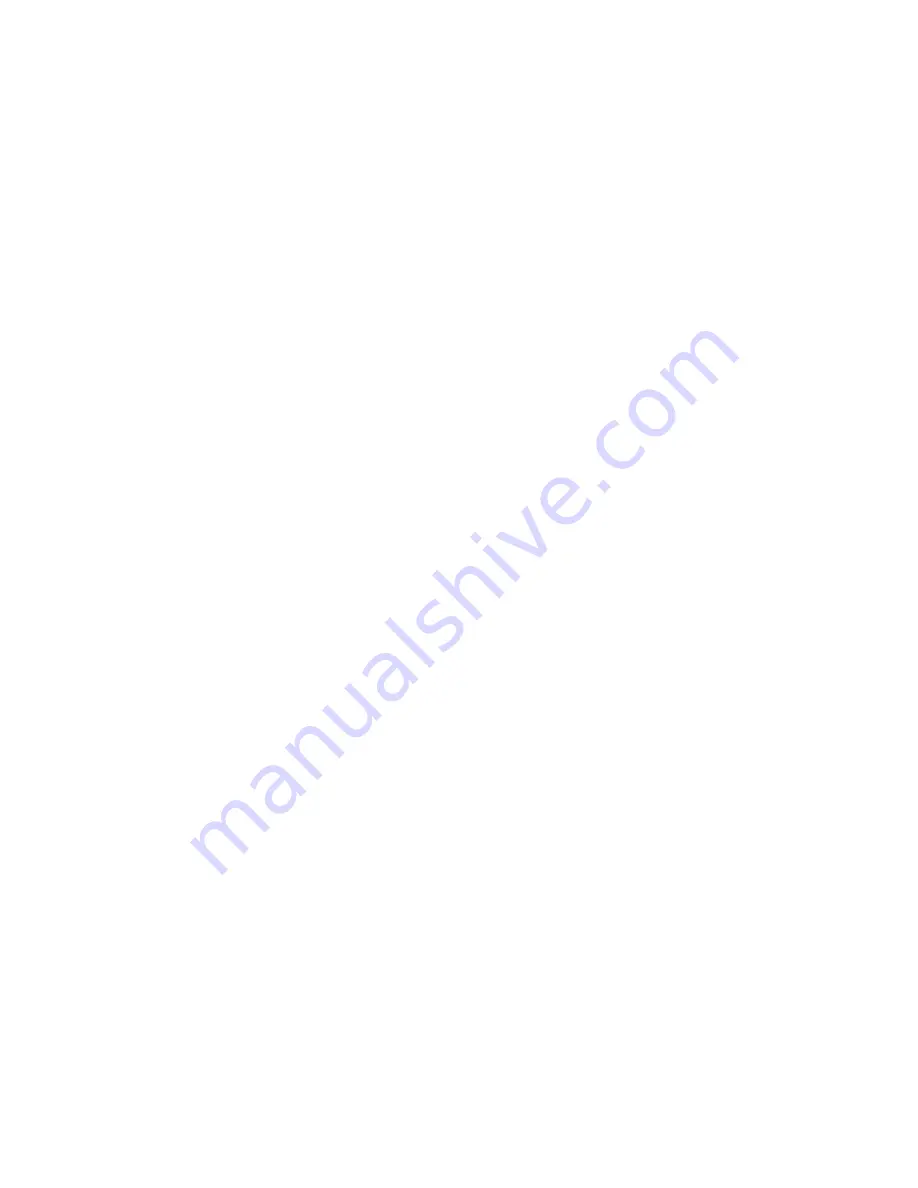
Contents
2
GA01423_002_C0 - 10/2016 - © Leybold
Page
0
Important Safety Information
4
0.1
Mechanical Hazards
4
0.2
Electrical Hazards
4
0.3
Thermal Hazards
4
0.4
Hazards Caused by Materials and Substances
5
0.5
Danger of Damages to the Pump
5
1 Description
8
1.1
Design and Operation
8
1.2
Component Designations of the Individual Pump Types
10
1.2.1 Ordering Information
10
1.3
Technical Data
11
1.3.1 Motor Data
12
1.3.2 Dimensions
15
2
Transport and Storage
18
3 Installation
19
3.1
Checking the Product
19
3.2
Conforming Use
20
3.3
Ambient Conditions
21
3.4
Setting up the Pump
22
3.5
Electrical Connections
23
3.5.1 Single-phase Motors
23
3.5.2 Three-phase Motors
26
3.6
Connection to the Vacuum System
29
4 Operation
30
4.1 Start-up
31
4.2 Pumping
32
4.3
Purge Gas Operation (pumping of vapours)
32
4.4 Shutdown
34
5 Maintenance
35
5.1
Table - Maintenance
37
5.2
Leybold Service
38
5.3
Waste Disposal
38
6 Troubleshooting
39
7
Spare Parts
40
EC Declaration of Conformity
41