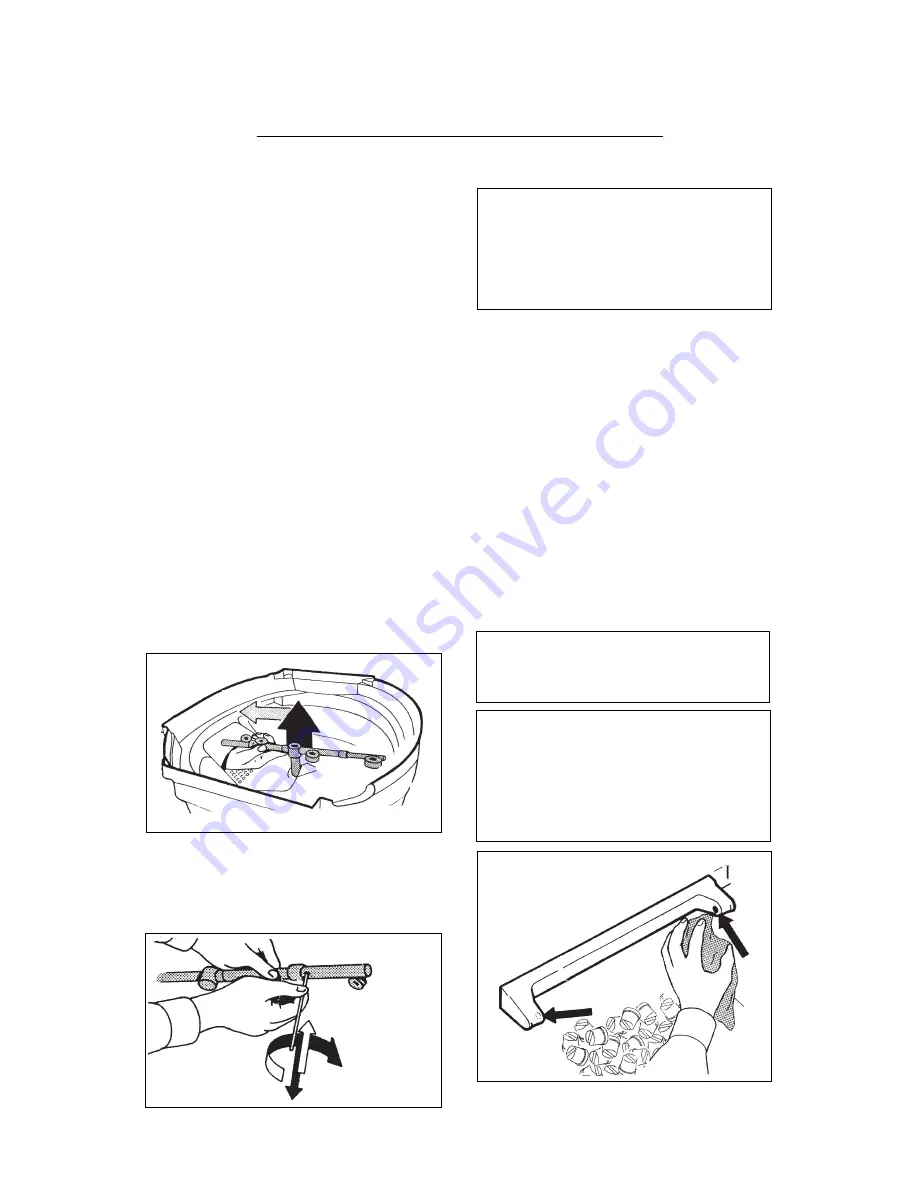
Page 31
Page 31
MAINTENANCE AND CLEANING INSTRUCTIONS
A.
GENERAL
The periods and the procedures for maintenance
and cleaning are given as guides and are not to
be construed as absolute or invariable.
Cleaning, especially, will vary depending upon
local water and ambient conditions and the ice
volume produced; and, each icemaker must be
maintened individually, in accordance with its
particular location requirements.
B. ICEMAKER
The following maintenance should be scheduled
at least two times per year on these icemakers.
1 .
Check and clean the water line strainer.
2.
Check that the icemaker is levelled in side
to side and in front to rear directions.
3.
Clean the water system, evaporators, bin
and spray bar/s using a solution of SCOTSMAN
Ice Machine Cleaner.
Refer to procedure C cleaning instructions and
after cleaning will indicate frequency and proce-
dure to be followed in local areas.
4.
Reach the water spray bar from the inside of
the freezing chamber lifting it from its seat with its
bottom race washer.
Dip it into a tray filled with cleaning solution then
rinse it under a tap water stream.
With a pick clean the orifice of the water stream
jet that propells the spray bar.
NOTE. Cleaning requirements vary according
to the local water conditions and individual
user operation. Continuous check of the clarity
of ice cubes and visual inspection of the
water spraying parts before and after cleaning
will indicate frequency and procedure to be
followed in local areas.
5.
With the ice machine and fan motor OFF on
air cooled models, clean condenser using vacuum
cleaner, whisk broom or non metallic brush taking
care to do not damage both the condenser and
ambient temperature sensor probes.
6.
Check for water leaks and tighten drain line
connections. Pour water down through the
storage bin drain line to be sure that drain line is
open and clear.
7.
Check size, condition and texture of ice
cubes. Perform adjustment of DIP SWITCH keys
as required.
8.
Check the ice level control sensor to test
shut-off. Put some ice cubes between the light
source and the receiver so to cut off the light
beam for at least one minutes.
This should cause the ice maker to shut off and
the light-up of the 2nd LED (yellow light).
IMPORTANT. Perform the above check only
at the end of harvest cycle or at the beginning
of freezing cycle in order to do not cause to
the unit to make a double freezing cycle.
NOTE. Within few seconds after the removal
of the ice cubes from the Infrared sensing
light the icemaker restarts in freezing cycle.
The ice level control uses devices that sense
light, therefore they must be kept clean
enough so they can "see".
Every month clean/wipe the sensing "eyes"
with a clean soft cloth.
9. Check for refrigerant leaks.
Содержание MXG 327
Страница 4: ...Page 3 Page 3...
Страница 20: ...Page 18 Page 18...
Страница 29: ...Page 27 Page 27 WIRING DIAGRAM MXG 327 427 437 A 230 50 1...
Страница 30: ...Page 28 Page 28...