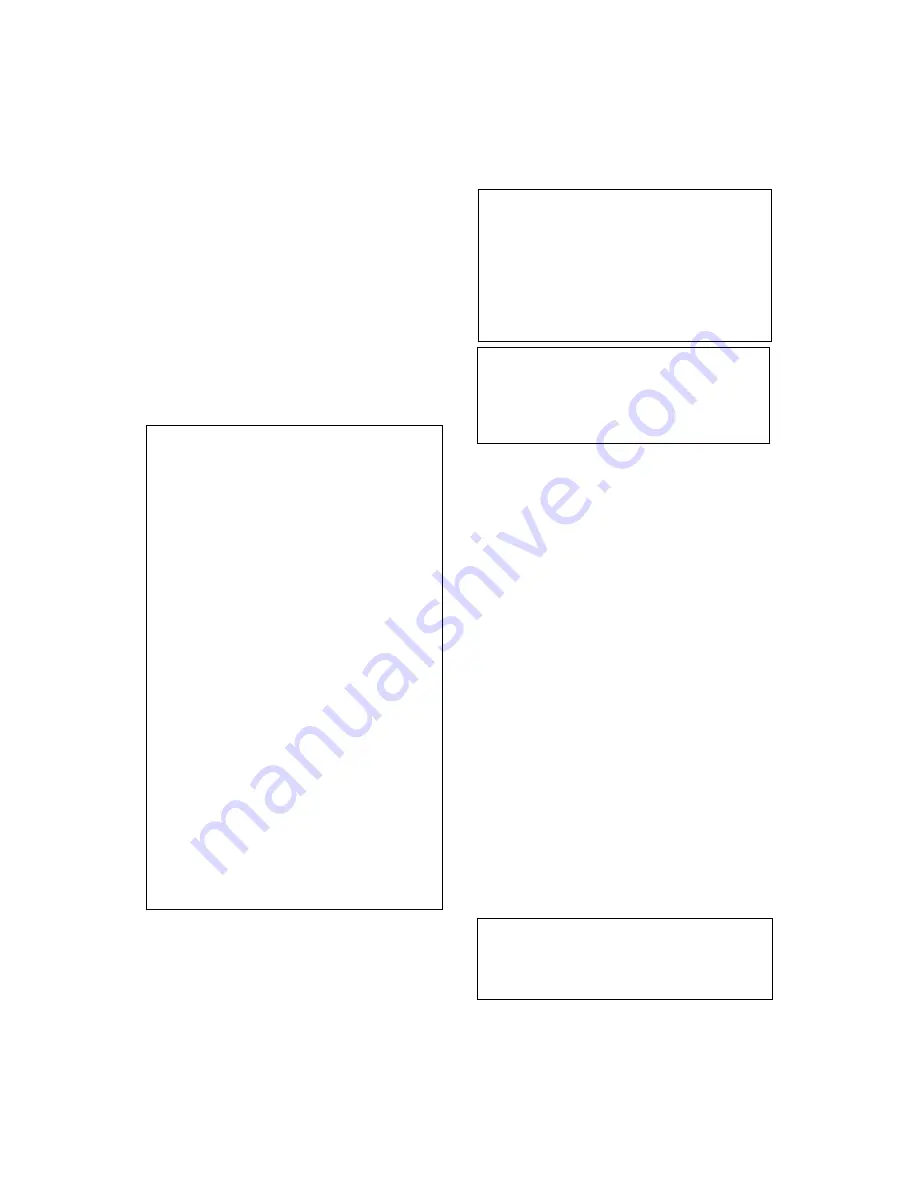
Page 27
Page 27
and between 9.5 and 10.5 bar (135
÷
150 psig) in
the water cooled version, being controlled by the
temperature sensor probe located within the
condenser fins (air cooled version) or, on the
condenser tube coil (water cooled version).
On the air cooled version, the condenser tempe-
rature sensor, when senses a rising of the
condenser temperature beyond the pre-fixed
limit, changes its electrical resistance and
transmits a low voltage power flow to the Micro
Processor of P.C. BOARD which in turn
energizes, through a TRIAC, the FAN MOTOR.
When the opposite situation occures, i.e. the
condenser temperature gets below the pre-fixed
limit, the temperature sensor changes again its
electrical resistance reducing therefore the
current flow to the P.C. BOARD to cause the fan
motor temporary cut-off.
NOTE. In case the condenser temperature
probe senses that the condenser temperatu-
re has rised to 70
°
C (160
°
F) - on air cooled
versions - or 60
°
C (140
°
F) - on water cooled
versions - for one of the following reasons:
CLOGGED CONDENSER (Air cooled
version)
INSUFFICIENT FLOW OF COOLING
WATER (Water cooled version)
FAN MOTOR OUT OF OPERATION (Air
cooled version)
AMBIENT TEMPERATURE HIGHER THEN
40
°
C (100
°
F)
it causes the total and immediate SHUT-
OFF of the machine in order to prevent the
unit from operating in abnormal and
dangerous conditions.
When the ice maker stops on account of this
protective device, there is a simultaneous
glowing of the RED LED, warning the user of
the Hi Temperature situation.
After having eliminated the source of the
condenser hi-temperature, to restart the
machine it is necessary to unplug (wait few
seconds) and plug in again the unit. The ice
machine resumes its normal operation by
going through the 5 minutes water filling
phase.
At the start of the freezing cycle the refrigerant
suction or lo-pressure lowers rapidly to 1 bar -
14 psig then it declines gradually - in relation with
the growing of the ice thickness - to reach, at the
end of the cycle, approx. 0
÷
0,1 bar - 0
÷
0,3 psig
with the cubes fully formed in the cup molds.
The total length of the freezing cycle ranges from
20 to 25 minutes.
DEFROST OR HARVEST CYCLE
(Fig.E and G)
As the electronic timer has carried the system
throughout the second phase of freezing cycle,
the defrost cycle starts.
ATTENTION. In case the unit is able to
reach 0
°
C (32
°
F) evaporating temperature
within 15 minutes, but after 45 minutes
from the beginning of the freezing cycle it
has not yet reached the evaporator tem-
perature of -15
°
C (5
°
F) the machine goes
straight into the defrost cycle omitting
the timed portion of the freezing cycle
relied to the setting of the first four DIP
SWITCHES.
NOTE. The length of the defrost cycle (not
adjustable) is related to the length of the
second phase of freezing cycle T2. (Time to
drop the evaporating temperature from 0
°
C
(32
°
F) - small Red LED blinking - to -15
°
C
(5
°
F) small Red LED ON steady.
The electrical components in operation during
this phase are:
COMPRESSOR
CONTACTOR COIL (EC 125-175 only)
WATER INLET VALVE
HOT GAS VALVE
WATER DRAIN VALVE
and the
WATER PUMP
on the first 15 seconds.
The incoming water, passing through the water
inlet valve and the flow control, runs over the
evaporator platen and then flows by gravity
through the dribbler holes down into the sump/
reservoir. (Fig. F and H )
The water filling the sump/reservoir forces part of
the surplus water from the previous freezing
cycle to go out to the waste through the overflow
pipe. This overflow limits the level of the sump
water which will be used to produce the next
batch of ice cubes.
Meanwhile, the refrigerant as hot gas, discharged
from the compressor, flows through the hot gas
valve directly into the evaporator serpentine by-
passing the condenser.
The hot gas circulating into the serpentine of the
evaporator warms up the copper molds causing
the defrost of the ice cubes. The ice cubes,
released from the cups, drop by gravity onto a
slanted cube chute, then through a curtained
opening they fall into the storage bin.
NOTE. The length of the defrost cycle,
factory set, changes in accordance with the
duration of the second portion of the freezing
cycle (Time T2) that is related to the ambient
temperature.
At the end of the defrost cycle, the hot gas valve,
the water inlet valve and the water drain valve
close and the machine starts again a new freezing
cycle.
Содержание EC 105
Страница 25: ...Page 25 Page 25 FIG A FIG B FIG C FIG D ...
Страница 26: ...Page 26 Page 26 FIG E FIG F FIG G FIG H ...
Страница 36: ...Page 36 Page 36 WIRING DIAGRAM EC 45 55 85 105 AIR WATER COOLED 230 50 60 1 ...
Страница 37: ...Page 37 Page 37 WIRING DIAGRAM EC 125 175 AIR WATER COOLED 230 50 60 1 ...